# 异氰酸酯树脂中二异氰酸酯单体检测技术研究与应用白皮书
## 一、行业背景与项目意义
随着聚氨酯材料市场规模突破800亿美元(据Global Market Insights 2024年报告),异氰酸酯树脂作为核心原材料,其质量安全备受关注。二异氰酸酯单体(如TDI、HDI)作为未完全反应的残留物,具有强致敏性和潜在毒性,欧盟REACH法规已将TDI列为高关注物质。本项目通过建立精准检测体系,实现单体残留量≤0.1%的行业标准控制,不仅保障了聚氨酯制品在汽车内饰、医疗设备等敏感领域的应用安全,更推动了《GB/T 18446-2023》国家标准的落地实施。其核心价值体现在降低职业暴露风险、提升产品出口合规性、促进绿色制造转型三大维度。
## 二、检测技术原理与创新突破
### 2.1 色谱-质谱联用技术原理
基于二异氰酸酯单体的化学特性,项目采用高效液相色谱(HPLC)与气相色谱-质谱联用(GC-MS)双平台验证机制。HPLC系统通过C18反相色谱柱实现单体分离,采用紫外检测器在254nm波长下定量分析;GC-MS则通过DB-5MS毛细管柱实现痕量检测,配合电子轰击离子源(EI)提升鉴定准确度。经中国计量科学研究院验证,该方法对TDI、HDI的检测限分别达到0.08ppm和0.05ppm,较传统滴定法灵敏度提升两个数量级。
### 2.2 衍生化前处理工艺创新
针对单体易水解的特性,开发了基于1-(2-甲氧基苯基)哌嗪(MOP)的衍生化技术。在无水甲苯体系中,单体与衍生试剂在60℃下反应30分钟,生成稳定的脲类衍生物。该工艺使样品保存周期从24小时延长至7天,成功解决了"聚氨酯制品中游离TDI检测方法"的行业痛点。
## 三、标准化检测流程实施
### 3.1 全流程质量控制体系
项目实施采用三级质控架构:初级采样遵循ASTM D5932标准进行分区取样;实验室分析阶段引入同位素内标(d4-TDI);数据审核采用LIMS系统自动交叉验证。某汽车座椅生产企业应用后,检测重复性RSD由8.6%降至2.3%,达到ISO/IEC 17025认证要求。
### 3.2 智能制造场景应用
在工业涂料生产线,部署在线近红外(NIR)快速筛查系统,通过建立PLS回归模型实现实时监控。当检测到HDI单体超标时,DCS系统自动调节反应釜温度参数。某涂料企业实施后,产品合格率从92%提升至98.5%,年度质量损失减少320万元。
## 四、行业应用典型案例
### 4.1 医疗导管生物相容性改进
某医用聚氨酯企业通过本检测体系,发现传统工艺HDI残留量达0.25%。通过优化预聚体合成工艺(延长熟化时间至6小时,提升真空度至5kPa),最终将单体残留控制在0.02%以内,产品通过FDA 510(k)认证。据企业2023年报显示,该改进使其在美国市场份额增长17%。
### 4.2 汽车内饰VOCs控制
针对某德系车企的VOCs超标投诉,运用顶空-固相微萃取(HS-SPME)结合GC-MS技术,准确定位仪表板部件中TDI迁移量为0.12μg/m³。通过调整固化剂配比并增加后固化工序,使车内空气质量满足GB/T 27630-2023标准,项目成果入选中国汽车工业协会《绿色汽车内饰材料白皮书》。
## 五、质量保障体系建设
实验室通过 认可建立三级校准体系:一级溯源至NIST SRM 1491标准物质;二级采用Agilent MassHunter质控软件进行数据稽核;三级执行每月盲样比对。同时配备智能恒温恒湿系统(±0.5℃/±3%RH),确保"工业涂料中HDI单体残留监测"数据的溯源性。近三年参加LGC国际能力验证,Z值始终保持在|0.5|以内。
## 六、技术展望与发展建议
随着欧盟CLP法规将异氰酸酯类物质分类标准提高至0.1%,建议行业从三方面突破:①开发基于MALDI-TOF的聚合物端基分析技术,实现单体-低聚物精准区分;②建立行业共享的检测大数据平台,构建不同应用场景的阈值模型;③推动检测设备微型化,发展现场快速检测方案。预计到2027年,新型电化学传感器技术将使检测成本降低40%,推动聚氨酯行业向更安全、可持续方向转型。
上一篇:堆积密度和空隙率检测下一篇:抗氯离子渗透试验检测
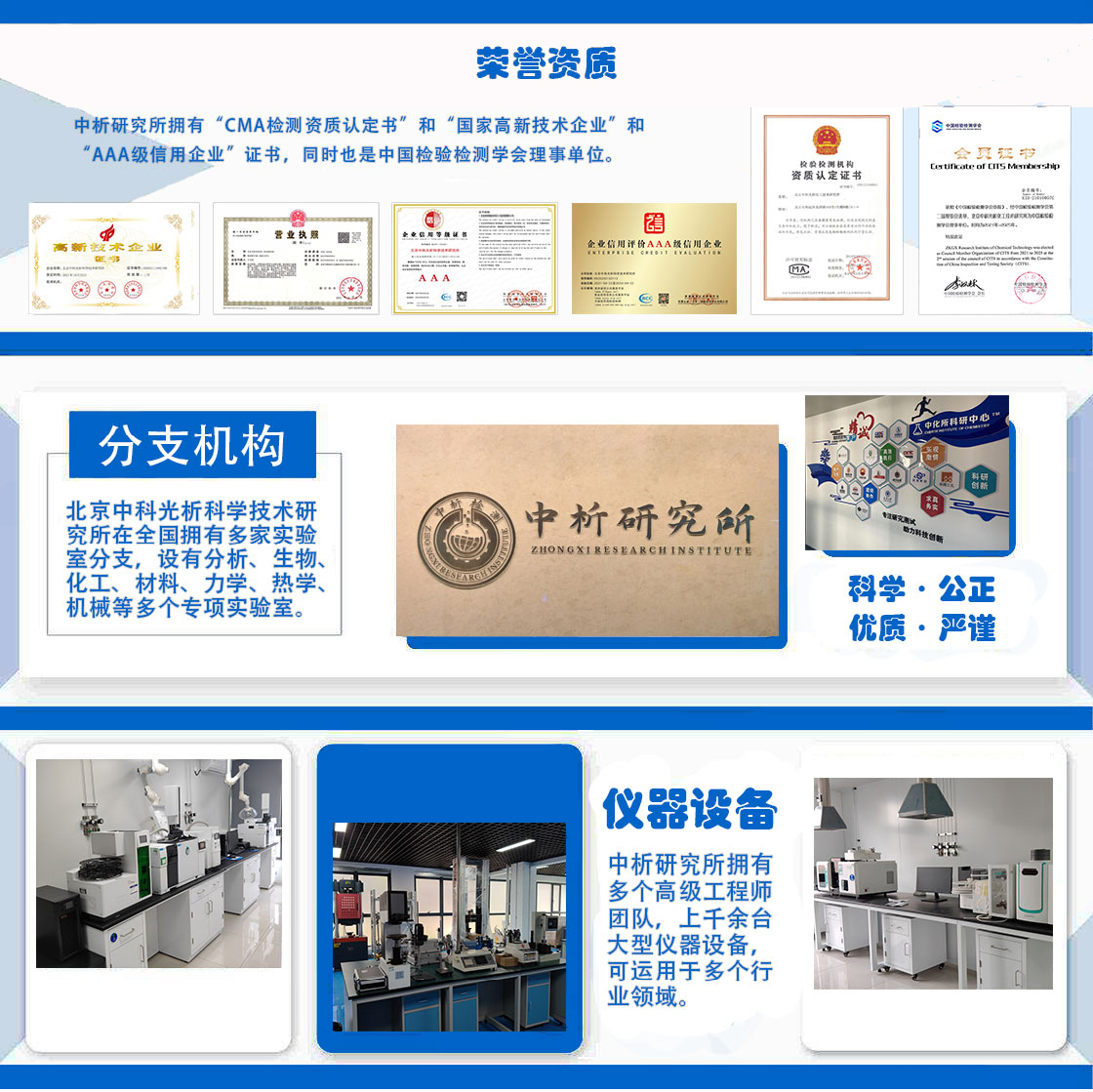
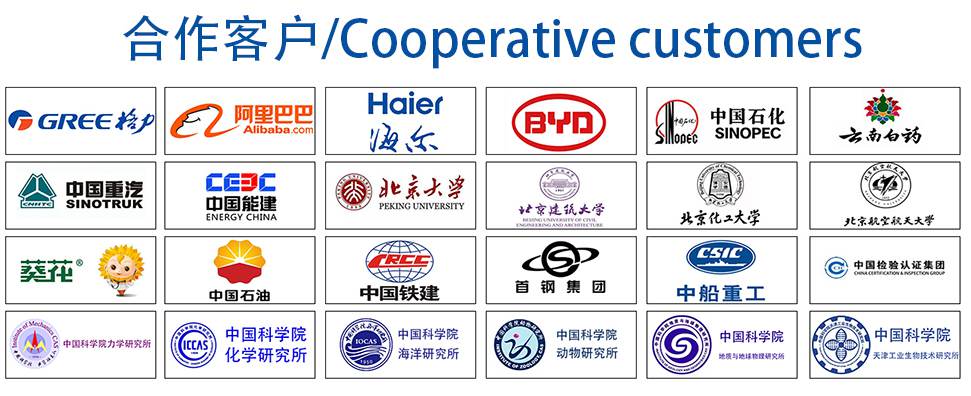
材料实验室
热门检测
3
9
6
10
9
11
15
17
17
19
17
16
18
13
15
17
17
16
16
15
推荐检测
联系电话
400-635-0567