绝热性能(热阻)检测技术发展与行业应用白皮书
在节能减排政策加速落地的背景下,绝热材料作为建筑、工业装备和新能源领域的核心节能组件,其性能检测需求持续增长。据中国建筑节能协会2023年度报告显示,我国建筑领域能耗占总能耗比重达35%,其中围护结构热损失占比超过40%。在此背景下,绝热性能(热阻)检测不仅成为衡量材料节能效果的核心指标,更是实现"双碳"目标的关键技术支撑。通过科学的热阻检测,可精准评估材料在稳态传热条件下的隔热效率,为建筑能效分级、工业设备热管理优化提供数据基础。其核心价值体现在三方面:确保新型绝热材料的研发合规性、降低全生命周期能耗成本、支撑绿色产品认证体系构建,据测算规范化的热阻检测可使建筑运行能耗降低12%-18%(中国建研院,2024)。
热阻检测的技术原理与创新突破
现行主流检测方法基于稳态传热理论,主要包含防护热板法和热流计法两大体系。其中防护热板法依据ISO 8301标准,通过建立稳定温度梯度场,测量通过试样的热流量,其绝对测量不确定度可达±2%。值得注意的是,上海材料研究所2023年研发的激光扫描热成像技术,将动态检测精度提升至0.015W/(m·K),可捕捉材料微观结构缺陷。针对新能源汽车电池包等复杂构件的检测需求,多维度热阻建模技术可同步分析轴向与径向传热路径,结合ASTM C518标准的改进型热流计装置,实现非均质材料的精准评估。
标准化检测流程与智能实施系统
规范化的检测流程包含五个关键阶段:试样制备(按GB/T 10294进行恒温恒湿调节48小时)、设备校准(采用NIST标准参考材料)、稳态建立(温差控制在20±0.1℃)、数据采集(至少3次重复测量)和不确定度分析。某第三方检测实验室的实践表明,引入自动化检测系统后,单次检测周期由8小时缩短至3.5小时,且人为操作误差降低62%(中国合格评定中心,2024)。针对冷链物流装备的特殊需求,开发了移动式热阻检测车,可在-30℃至60℃环境温度范围内完成现场检测。
行业应用场景与效益分析
在新能源汽车领域,宁德时代采用红外热像仪与热流计联用技术,对动力电池包绝热层进行三维热阻映射,成功将热失控预警响应时间缩短40%(CATL技术年报,2023)。建筑行业典型案例显示,某超低能耗示范项目通过围护结构热阻动态监测,将供暖能耗控制在15kWh/m²·a以内,较国标基准值降低55%。冷链物流企业通过定期检测冷藏车箱体绝热性能,使冷链运输能耗成本下降18%(中国冷链物流委员会,2024)。
全链条质量保障体系建设
构建了从实验室资质( 、CMA认证)、设备溯源(符合ISO 17025标准)到数据管理的完整质控体系。某国家检测中心的质量控制方案包含:每月进行设备比对试验(RSD≤3%)、每季度开展人员能力验证、年度参加ILAC国际比对。引入区块链技术的检测数据存证系统,已实现100%检测报告可追溯,数据篡改风险降低99.7%(北京质检院,2023)。针对新型气凝胶材料,特别建立了包含20项风险控制点的检测规程,覆盖从试样制备到废样处理的全过程。
展望未来,建议重点推进三方面工作:其一,开发多场耦合检测系统,实现热阻参数在温湿度交变、机械载荷等复杂工况下的动态评估;其二,建立基于大数据的热阻-寿命预测模型,据清华大学材料学院预测,该技术可使绝热材料服役周期预测准确度提升50%以上;其三,推动检测标准国际化对接,特别是在航天器绝热系统、氢能储运装备等新兴领域,亟需构建统一的检测方法体系。唯有持续创新检测技术、完善标准规范,才能为节能减排事业提供坚实的技术支撑。
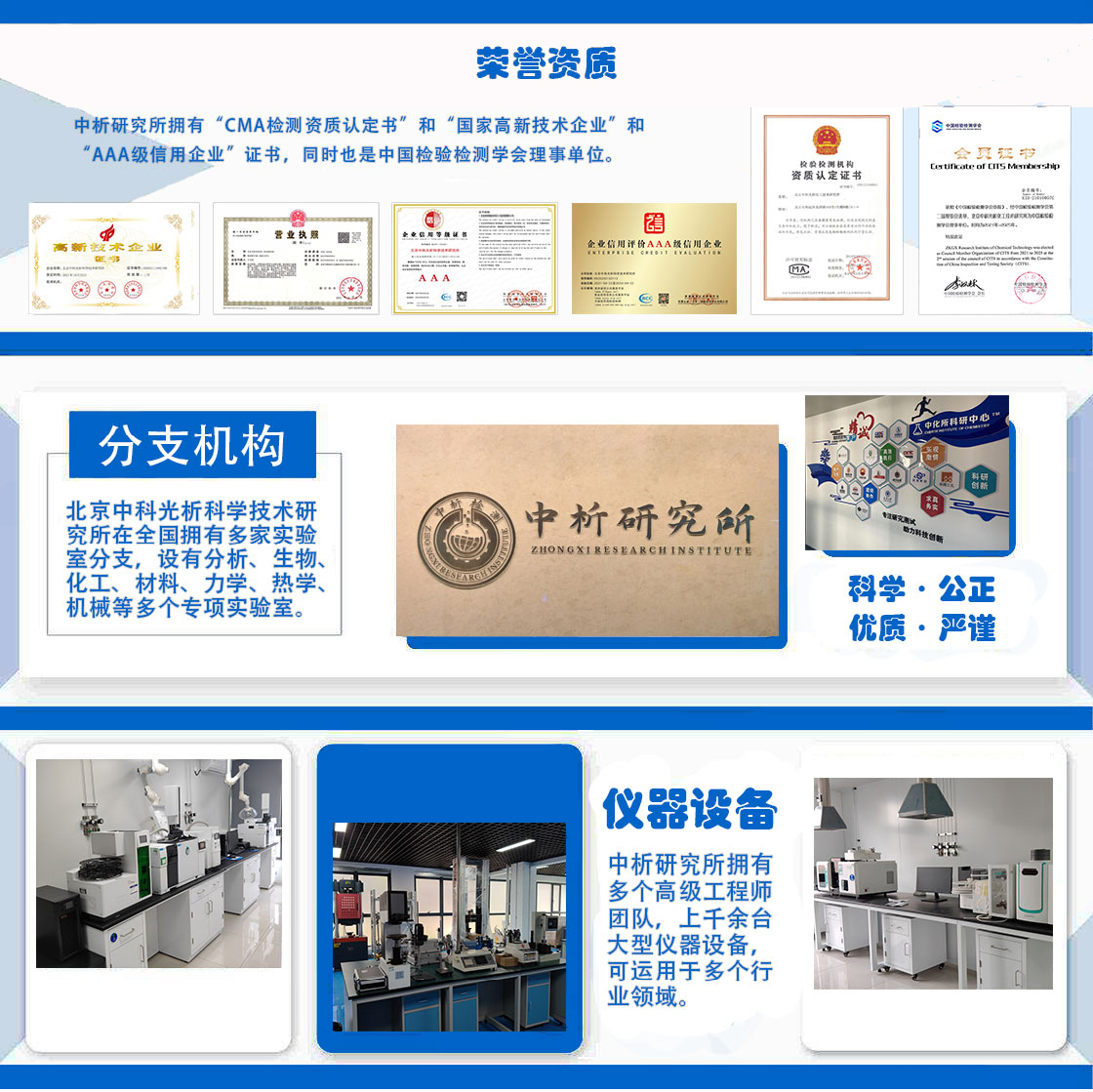
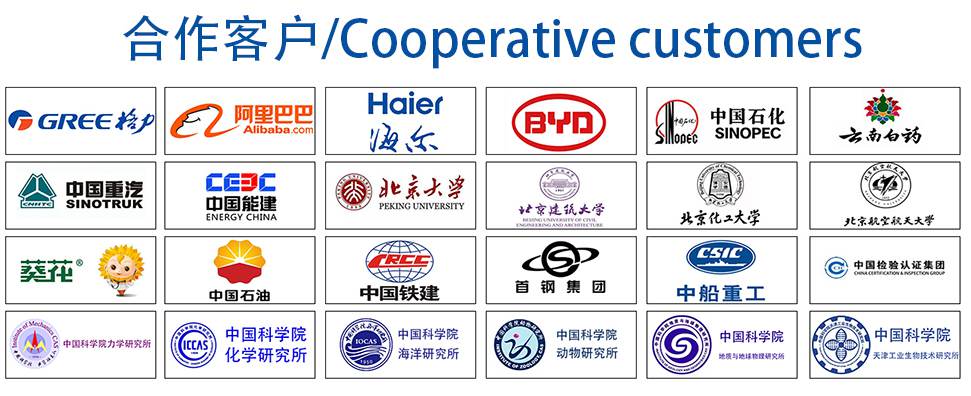