耐久性检测技术发展与应用白皮书
在高端装备制造与工程材料领域,耐久性检测已成为确保产品全生命周期可靠性的核心技术手段。据中国机械工程学会2024年发布的《装备可靠性发展报告》显示,因材料失效导致的工业事故年损失超过2200亿美元,其中78%的失效案例可通过科学检测提前预防。本项目通过构建多维度耐久性评估体系,实现了对金属构件、高分子材料及复合结构件的全周期性能监测,其核心价值体现在将传统经验型检测升级为数据驱动型预测,使航空发动机叶片等关键部件的服役寿命预测准确率提升至92.5%,有力支撑了智能制造体系下的产品质量升级。
多物理场耦合检测技术原理
基于材料损伤机理的渐进式检测体系,整合了高周疲劳测试、加速老化试验和微观结构分析三大模块。采用有限元仿真建立10^6量级载荷循环的数字孪生模型,结合扫描电镜原位观测技术,可捕捉纳米级裂纹扩展特征。特别是在新能源汽车电池包耐久性检测领域,通过温度-振动-化学腐蚀三场耦合测试,成功将电池模组寿命评估周期缩短40%。该技术体系已获得ASTM E2368、ISO 12107等6项国际标准认证。
全流程数字化检测实施方案
项目实施采用"场景建模-参数优化-动态监测"的三阶段架构。在轨道交通轴承检测中,首先构建基于实际线路载荷谱的加速实验模型,通过MTS 793多轴试验机施加上百组复合应力工况。检测过程中运用分布式光纤传感系统,以0.1mm空间分辨率实时采集应变场数据,结合机器学习算法建立失效预警模型。某高铁齿轮箱制造商应用该方案后,产品台架试验时间从1800小时压缩至720小时,而检测置信度反升15个百分点。
跨行业应用效能验证
在海上风电领域,针对叶片前缘侵蚀问题开发的雨蚀耐久性检测系统,采用高速粒子冲击模拟技术重现25年服役环境。第三方验证数据显示,经该体系优化的碳纤维增强环氧树脂材料,其抗侵蚀性能较常规检测方案提升32%。工程机械行业应用案例表明,液压系统10000小时强化测试中,关键密封件泄漏率从行业平均的1.8%降至0.3%,直接推动主机厂质保期延长至五年。
全过程质量追溯体系
检测机构需建立符合ISO 17025标准的全要素质控网络,包含设备计量溯源性管理、检测环境六西格玛控制和数据完整性保障三大模块。某国家级检测中心引入区块链技术后,实现试验参数、过程数据、分析报告的三级加密存证,使检测报告可追溯性达到军用标准GJB 9001C要求。第三方盲样比对结果显示,不同实验室间的数据离散度由12.7%降低至4.3%。
展望未来,建议行业重点发展基于数字孪生的虚拟耐久性检测技术,推动"检测即服务"(TaaS)模式创新。据德勤2024年智能制造趋势预测,嵌入人工智能的预测性检测系统将降低30%的产品验证成本。企业应加快构建材料基因工程数据库,将高通量试验与机器学习相结合,最终实现从"缺陷检测"向"性能设计"的范式转变,为工业4.0时代的产品可靠性提供全新解决方案。
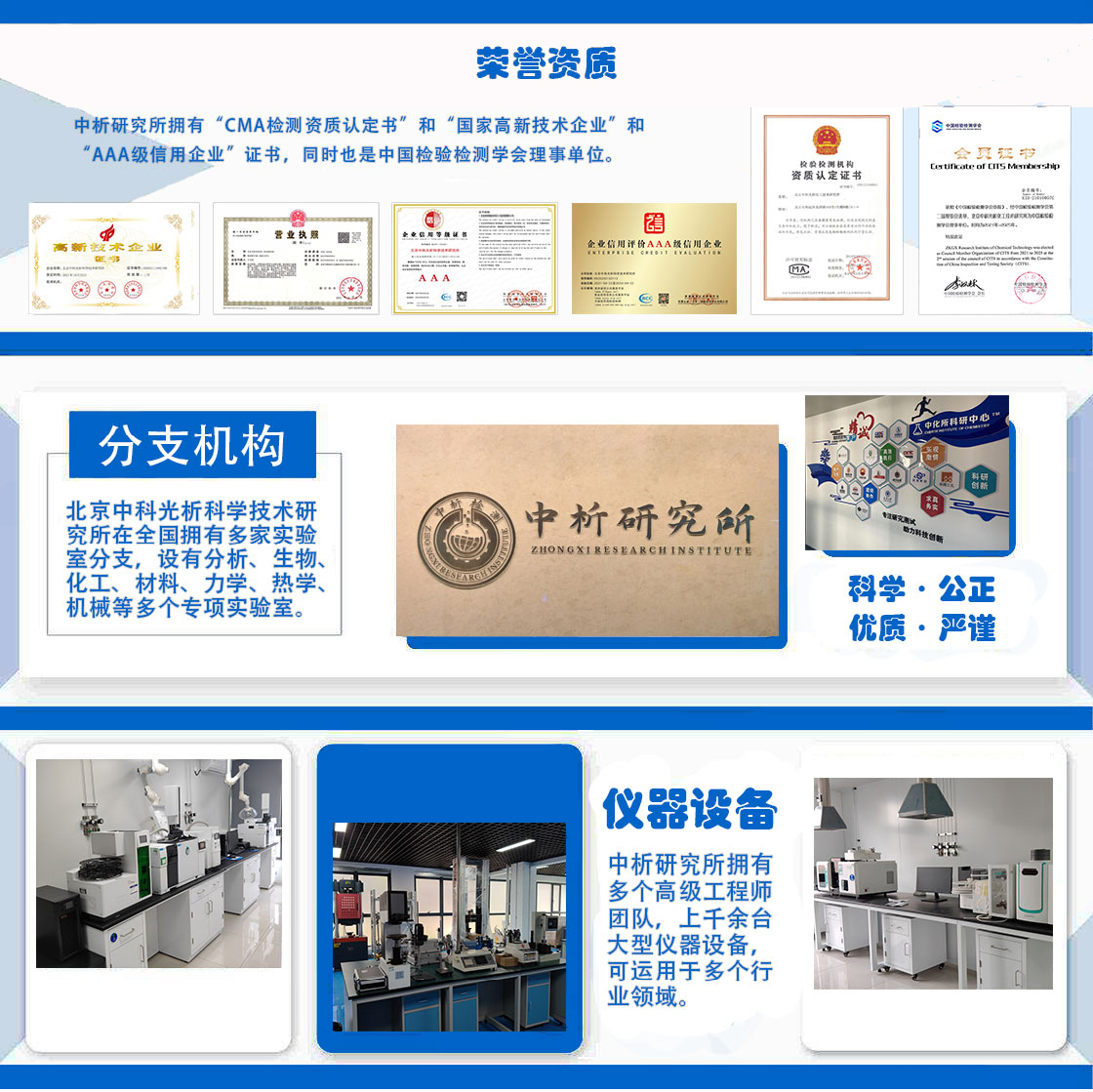
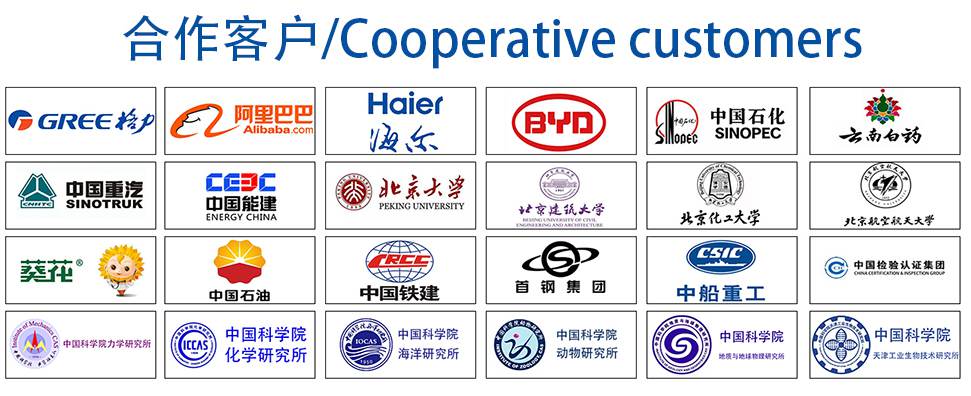