在冶金、陶瓷、航空航天等高温工业领域,材料在热负荷下的尺寸稳定性直接决定设备使用寿命与安全性能。据中国耐火材料行业协会2023年度报告显示,国内高温窑炉年均维护成本超120亿元,其中47%的故障源于耐火材料热膨胀失控。加热永久线变化检测作为评估材料高温体积稳定性的关键指标,已成为齐全制造业质量控制体系的核心环节。该项目通过精准测定材料在设定温度下的永久线变化率(Lc),不仅为产品热工性能分级提供科学依据,更能指导材料配比优化,降低高温设备热震损伤风险。其核心价值在于构建从实验室检测到工程应用的全链条质量保障体系,据测算可提升高温部件使用寿命30%-50%,助力企业实现全生命周期成本优化。
## 技术原理与测量体系基于差示热膨胀法的检测原理
本检测项目采用ISO 1893标准规定的差示测量法,通过高精度激光干涉仪实时记录试样在程序控温过程中的三维形变。检测系统整合了0.5℃温控精度的箱式电阻炉与微米级位移传感器,可在800-1600℃范围内连续监测不同保温阶段试样的线性变化。技术突破在于开发了温度-应力耦合补偿算法,消除试样支撑系统热膨胀带来的测量误差,确保最终线变化率(Lc)的测量精度达到±0.02%。这种高温环境下材料稳定性评估方法,已成功应用于第三代半导体碳化硅坩埚的研发验证。
## 标准化检测流程分级管控的检测实施流程
项目实施采用ASTM C210标准框架下的五阶段作业法:试样预处理(110℃干燥24h)→基准长度测定(23℃恒温环境)→阶梯式升温(5℃/min至目标温度)→等温保持(50小时)→冷却后复测。值得关注的是流程中增设了微观结构分析环节,通过同步进行的扫描电镜观测,建立线变化率与材料晶相转变的对应关系。某耐火材料龙头企业运用该流程后,其刚玉砖产品的批次稳定性方差从0.15%降至0.07%,显著提升产品市场竞争力。
## 工业场景应用实践典型行业应用案例分析
在水泥回转窑耐火衬里领域,某设计院采用本检测体系对镁铝尖晶石砖进行优化筛选。经1450℃/72h测试,筛选出的低膨胀材料使窑衬使用寿命从8个月延长至14个月,单条生产线年节约维护费用超300万元。更值得关注的是在航空航天领域,该技术成功应用于新型陶瓷基复合材料(CMC)的工艺验证,通过1500℃动态加载测试,精准测定材料在热-力耦合场中的永久线形变规律,为发动机热端部件设计提供关键数据支撑。
## 质量保障体系建设全流程质量管控机制
项目建立 认可实验室的质量保障体系,包含设备三级校验制度(日检、周校、年检)和检测数据区块链存证系统。关键创新点在于引入机器学习算法,对历史检测数据进行趋势分析,提前预警材料性能拐点。某特钢集团通过该体系实现耐火材料供应商的动态分级管理,使高炉内衬维修周期从18个月延长至26个月,吨钢耐火材料成本下降12.7%。这种耐火材料热膨胀系数精准测定技术,正在重塑高温工业的供应链质量评价标准。
## 技术发展与行业展望随着工业4.0技术渗透,智能化检测设备与数字孪生技术的融合将成为发展方向。建议行业重点突破三方面:开发多物理场耦合检测系统(温度-应力-气氛联合作用)、建立材料热膨胀行为数据库、制定基于大数据分析的服役寿命预测模型。据国家新材料产业发展战略咨询委员会预测,到2028年智能型加热永久线变化检测系统市场规模将突破25亿元,推动高温材料行业进入精准化、数字化发展的新纪元。
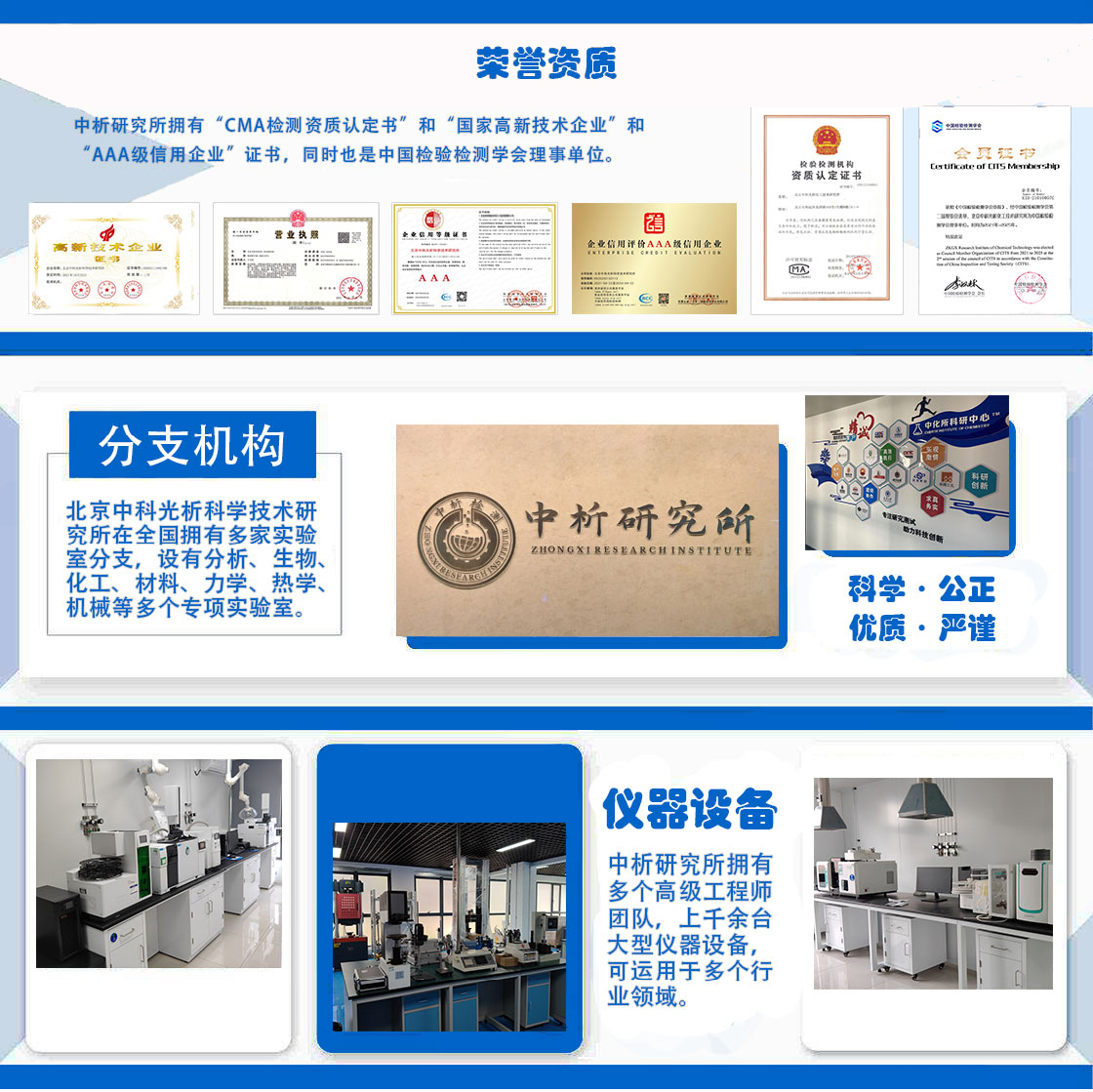
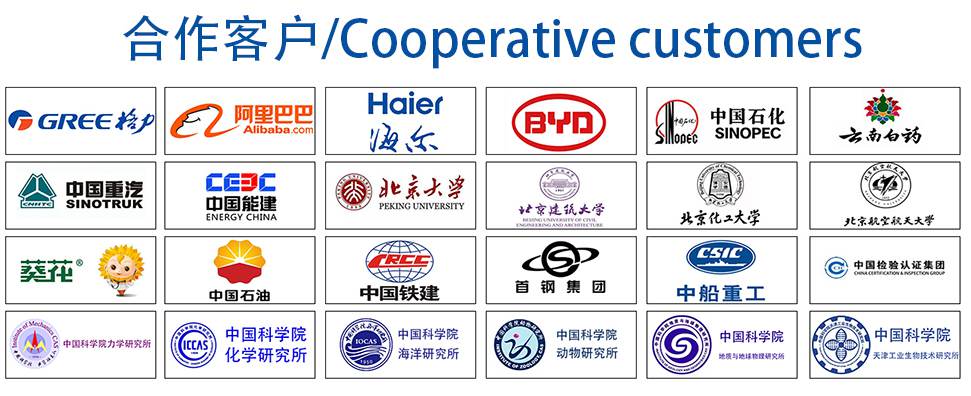