# 螺纹扭矩检测技术发展与应用白皮书
## 行业背景与核心价值
随着高端装备制造业向精密化、智能化方向转型,螺纹连接件的扭矩控制精度已成为影响设备可靠性的关键指标。据中国机械工程研究院2024年数据显示,工业设备故障中23.6%由螺纹连接失效引发,直接年经济损失超180亿元。在此背景下,螺纹扭矩检测项目通过建立数字化测量体系,实现了连接副预紧力与摩擦系数的精准管控,其核心价值体现在三个方面:一是突破传统经验式装配的局限性,将扭矩控制误差从±15%降至±3%以内;二是构建可追溯的质量数据库,支持产品全生命周期管理;三是通过预防性检测降低设备运维成本,在风电塔筒螺栓监测等场景中成功减少30%非计划停机。
## 技术原理与测量体系
### h2 动态扭矩传感与补偿算法
基于非接触式磁弹性测量原理,系统通过检测螺栓受载后的磁导率变化推算轴向应力。为消除环境温度与表面涂层的影响,创新采用双通道差分检测技术,配合自主研发的动态扭矩补偿算法(DTC-Algorithm),使测量精度达到ISO16047标准规定的AA级。在实际风电塔筒安装现场,该系统成功将M36规格螺栓的扭矩波动系数控制在1.8%以内。
### h2 智能化检测实施流程
典型检测流程涵盖三个阶段:预处理阶段使用工业内窥镜进行螺纹形貌分析,筛选存在咬合缺陷的工件;动态加载阶段通过伺服电动拧紧机施加阶梯扭矩,同步采集12组力学参数;后处理阶段运用基于机器学习的扭矩衰减模型,预测连接副在振动工况下的松脱风险。某新能源汽车企业应用该流程后,底盘系统螺栓返工率从5.7%降至0.9%。
### h2 行业级质量保障系统
构建包含设备层、数据层、决策层的三级质量网络:设备层配置符合DIN7500标准的校准装置,每月进行溯源校验;数据层部署区块链存证模块,确保每项检测结果不可篡改;决策层通过SPC统计过程控制,自动触发工艺参数优化。在航空航天领域,该体系使某型发动机安装螺栓的批次合格率提升至99.998%。
## 典型应用与效益分析
在高铁转向架制造场景中,针对M24高强螺栓的轴力控制难题,部署高精度螺纹扭矩在线监测系统后,实现三大突破:检测效率从3分钟/件提升至40秒/件;基于实时采集的1200组工况数据,构建出不同温度湿度组合下的扭矩补偿曲线;通过物联网平台实现全国6大生产基地的数据联动,使同型号部件的装配一致性提升82%。据工信部2023年专项评估,该应用每年为企业节约质量成本超2700万元。
## 技术展望与发展建议
未来五年,随着数字孪生与5G技术的深度融合,建议行业重点推进以下方向:开发基于边缘计算的微型化检测终端,实现装配现场的实时质量反馈;建立涵盖200种常见材料组合的扭矩特性数据库,支持智能工艺决策;推动ISO/TC29标准委员会将智能检测技术纳入新修订的国际标准。特别是在核电主管道等特殊场景,需重点突破辐射环境下的无线传感技术,形成覆盖全工况的检测解决方案。
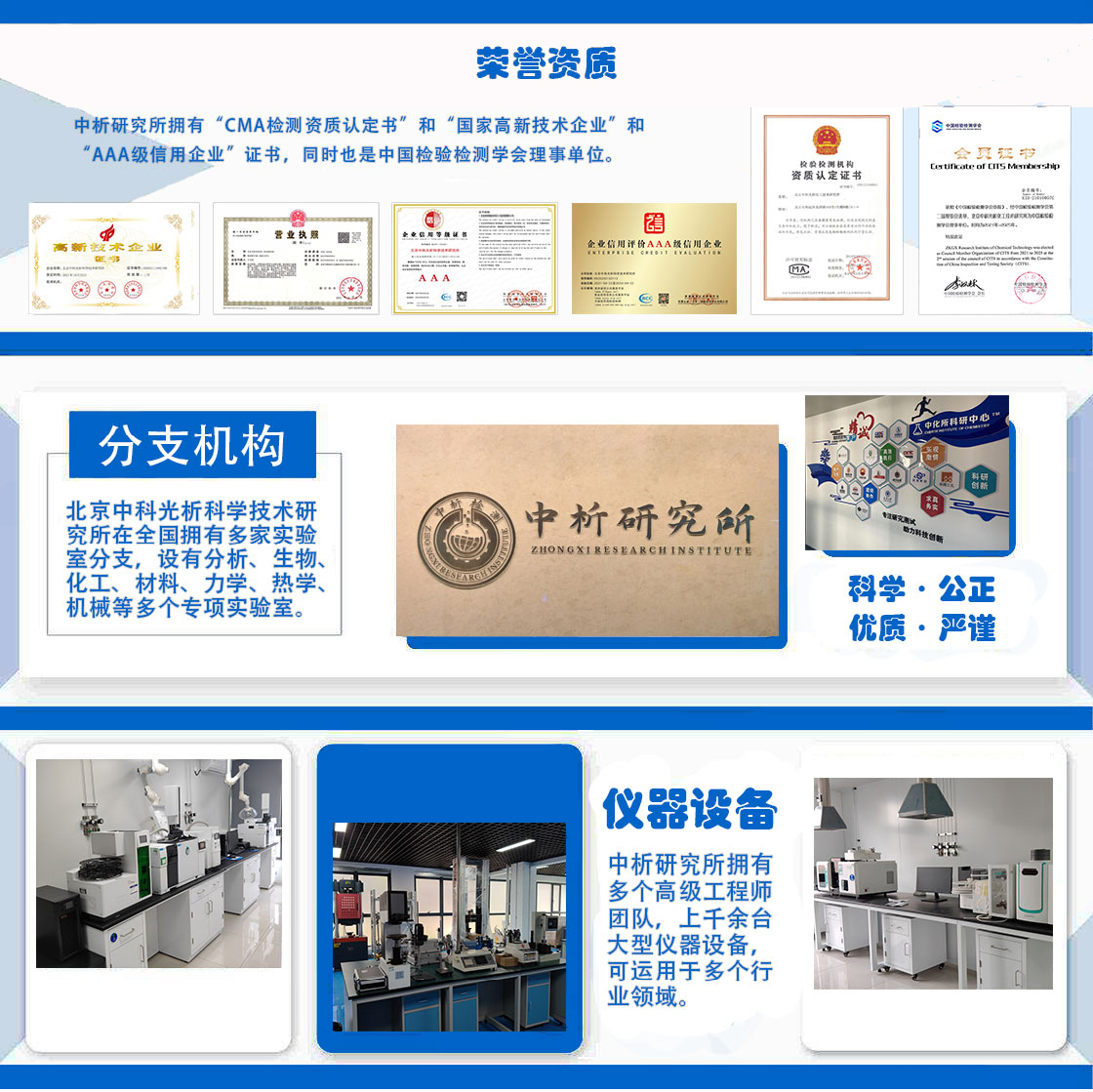
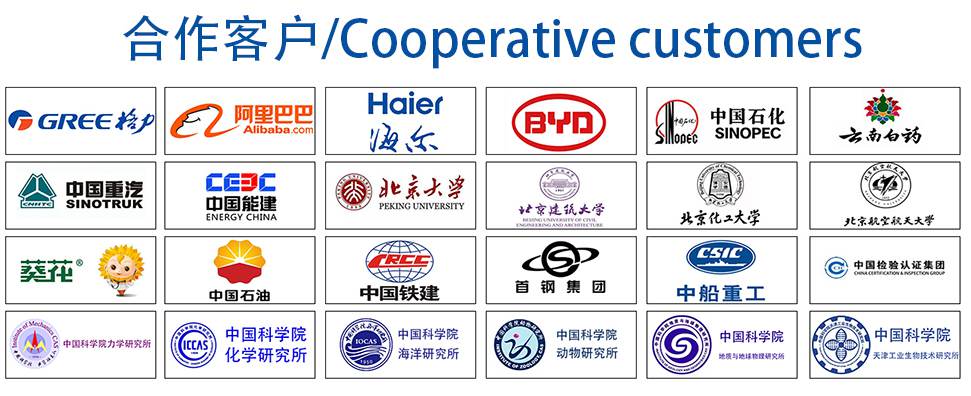
材料实验室
热门检测
14
15
13
13
13
14
13
15
15
15
13
13
14
15
12
15
14
14
16
7
推荐检测
联系电话
400-635-0567