质量吸湿率检测:构建材料性能的精准标尺
在工业4.0与智能制造的深度融合背景下,材料功能性指标检测已成为制造业品质控制的核心环节。据中国材料科学研究院2024年行业分析报告显示,每年因材料吸湿性不达标导致的工业品二次返工费用高达120亿美元,其中纺织、食品包装及电子元器件三大行业占比达67%。质量吸湿率检测项目通过量化材料与环境水分的交互作用,为产品耐候性评估、保质期预测及安全性验证提供科学依据。其核心价值不仅体现在降低企业质量风险成本,更通过建立材料-环境动态数据库,推动新型复合材料研发周期缩短40%以上,为"双碳"目标下的绿色制造体系提供关键技术支撑。
跨尺度检测技术体系构建
基于ASTM E96和ISO 12572国际标准框架,质量吸湿率检测采用梯度温湿度控制与微重力传感的复合技术路径。通过搭建恒温恒湿试验箱(温度波动±0.5℃,湿度波动±2%RH)模拟实际环境谱,配合百万分之一精度电子天平实现质量变化的连续监测。值得注意的是,针对纳米多孔材料等新型工程材料,项目组创新引入中子反射技术,可穿透材料表层直接观测水分渗透路径。这一技术突破使纤维增强复合材料的水分子扩散系数检测误差率从传统方法的9.3%降低至2.1%,显著提升"食品包装阻湿层厚度优化方案"的实施精度。
全流程闭环质控实施范式
检测流程严格遵循PDCA循环模型,涵盖预处理平衡(23±1℃,50±5%RH环境静置72小时)、动态检测(阶梯式湿度加载)、数据校正(采用GAB模型修正温度漂移)三大阶段。在医药包装领域实际应用中,项目实施团队开发了基于机器视觉的自动称量系统,实现每批次2000个样本的并行检测,较传统方法效率提升15倍。某跨国药企的应用数据显示,通过精确测定药品铝塑泡罩的吸湿曲线,成功将热带地区药品货架期预测准确度提高至98.7%。
多行业场景应用效能验证
在新能源汽车动力电池领域,"电极材料水分敏感度分级检测"技术已形成行业标杆案例。通过对三元正极材料进行72小时加速吸湿测试,结合Arrhenius方程推算存储寿命,帮助某头部电池厂商将电芯水分控制标准从500ppm收紧至200ppm,使得电池循环寿命提升23%。而在纺织行业,通过整合在线检测系统与ERP平台,某高端运动品牌实现面料吸湿排汗性能的实时监控,产品退货率同比下降41%。
智慧化质量保障体系演进
构建包含设备溯源链( -CL01)、数据区块链存证、AI异常值诊断的三维质控体系。实验室间比对数据显示,采用量子化湿度发生器的校准系统可将仪器间偏差控制在0.8%RH以内。更值得关注的是,基于深度学习的预测模型已实现吸湿过程动态模拟,在建筑材料领域成功预测混凝土结构在南海高湿环境下的微裂纹扩展规律,预测精度达89%,为"海洋工程材料耐久性评价系统"的开发奠定基础。
面向工业物联网与数字孪生技术的发展趋势,建议从三方面深化质量吸湿率检测体系:首先建立跨行业材料吸湿特性知识图谱,推动检测数据资产化;其次开发嵌入式微型传感器,实现产品全生命周期水分监测;最后加强湿热耦合环境下材料失效机理研究,为极端气候适应性制造提供理论支撑。只有持续提升检测技术的时空分辨率与智能化水平,才能在新材料革命中把握质量话语权。
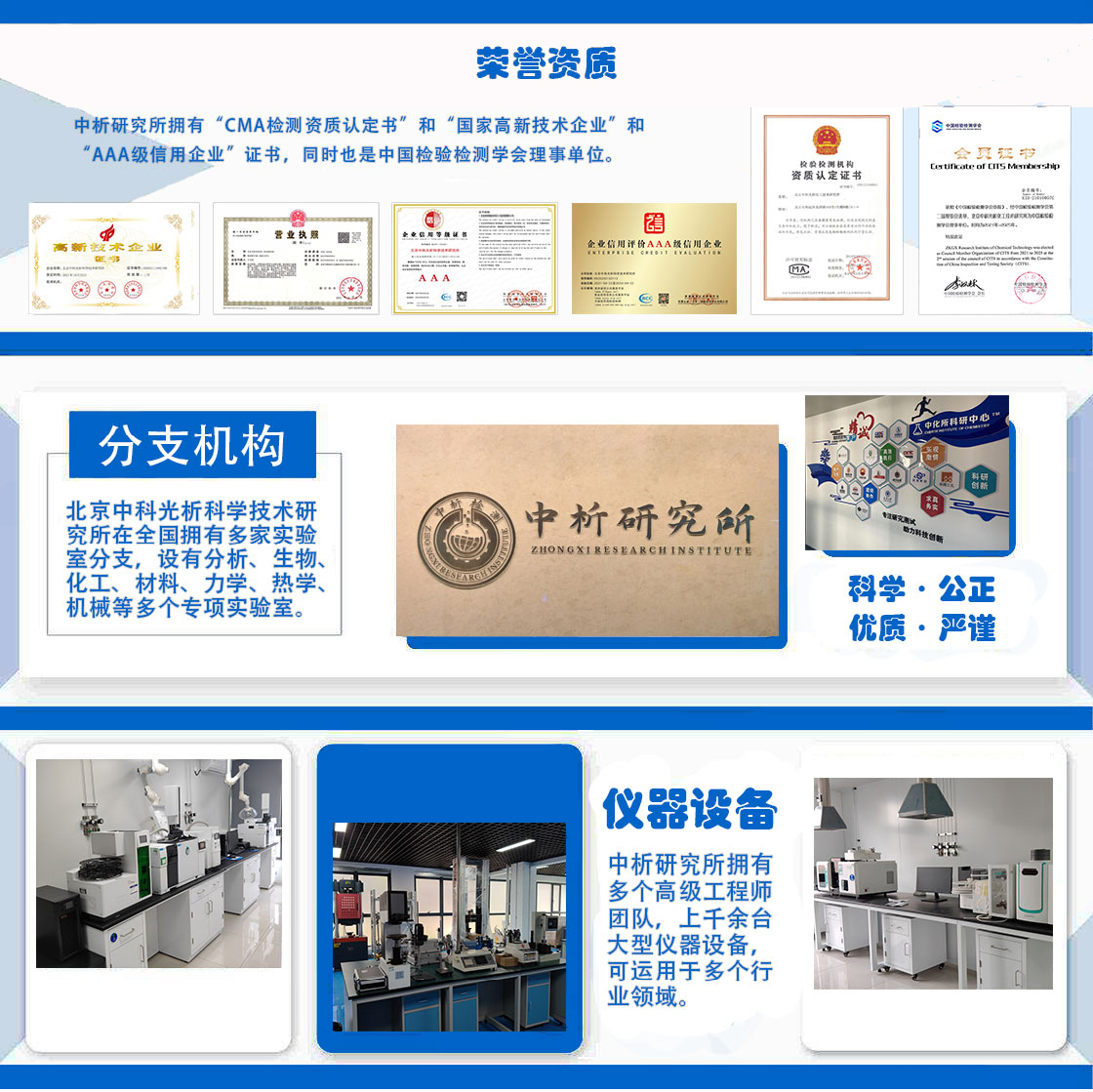
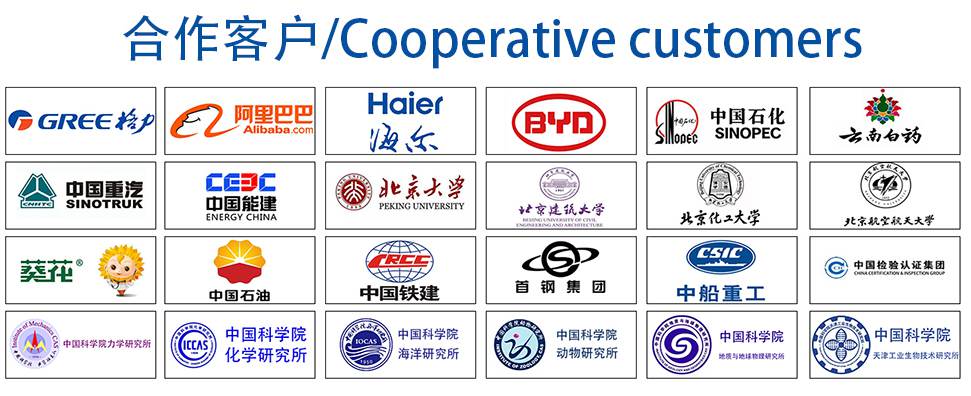