胶粘剂拉伸粘结强度与可操作时间检测技术白皮书
在新型工业化进程加速的背景下,胶粘剂作为现代制造业"工业缝纫线"的作用日益凸显。据中国建筑科学研究院2024年数据显示,我国胶粘剂市场规模已突破2000亿元,其中建筑、汽车、电子三大领域占比达65%。然而,因粘结失效引发的工程质量事故年损失超过80亿元,凸显出精准检测技术的迫切需求。拉伸粘结强度与可操作时间作为胶粘剂核心性能指标,直接影响结构安全与施工效率。通过建立科学检测体系,既可验证材料实际性能参数,又能优化施工工艺窗口,对于实现"材料-工艺-质量"全链条管控具有关键价值,特别是在装配式建筑接缝处理、新能源电池封装等高精度应用场景中,该检测项目已成为质量验收的强制性技术门槛。
技术原理与检测方法创新
拉伸粘结强度检测基于GB/T 7124标准,采用万能试验机模拟材料在拉伸剪切复合应力下的失效模式。通过制备标准尺寸粘结试件(40mm×40mm),以3mm/min速率加载直至破坏,同步记录最大载荷和破坏形态。可操作时间检测则依据GB/T 13477标准,运用旋转粘度计和凝胶时间测定仪,构建"双组分环氧树脂胶粘剂固化时间评估模型",实时监测粘度变化拐点。值得关注的是,智能传感器技术的引入使检测精度提升至±0.5%,较传统方法提高3倍效率。在新能源汽车电池包粘接案例中,该技术成功将固化时间预测误差控制在5分钟以内。
全流程标准化实施体系
完整的检测流程包含五大关键环节:基材表面处理(Sa2.5级喷砂处理)、胶粘剂调配(温湿度控制±1℃/±3%RH)、试件成型(压力0.2MPa保压30s)、环境模拟养护(依据EN 13813设置-40℃~85℃循环)以及数据采集分析。针对"有机硅密封胶开放时间测试"特殊需求,项目组开发了多探头红外热像仪监测系统,可同步捕捉20个监测点的温度场变化。某重点桥梁工程应用表明,该体系使施工窗口期判定准确率从78%提升至95%,减少返工损失超300万元。
行业应用与质量保障实践
在建筑幕墙工程领域,某超高层项目采用检测数据优化硅酮结构胶施工方案,将单层安装效率提升40%。检测报告显示,经-30℃低温循环后的粘结强度仍保持21MPa,远超16MPa的行业标准(JGJ 102-2023)。电子制造行业则通过可操作时间检测,实现芯片封装点胶工艺参数动态调整,某半导体企业良品率因此提高12个百分点。为确保检测质量,实验室构建三级校验体系:设备级(每年CMA计量认证)、过程级(每批次参比样测试)、数据级(区块链存证追溯),检测报告获得28国互认。
智能化质量保障体系构建
基于物联网技术的智能检测系统已实现三大突破:第一,嵌入式应变传感器可实时监测粘结界面应力分布;第二,机器学习算法对历史检测数据进行深度学习,生成材料失效预警模型;第三,检测数据与BIM系统直连,实现工程质量的数字孪生管理。某汽车制造企业的应用数据显示,该系统使白车身粘接强度离散系数从15%降至6%,同时缩短新产品验证周期30天。据国家市场监督管理总局2024年质量公报显示,通过该体系认证的企业产品抽检合格率达99.3%,高于行业平均水平8个百分点。
面向未来,建议从三方面深化发展:其一,开发适应极端环境(如深海、航天)的智能检测装备;其二,建立区域性检测数据中心,推动"检测-保险-认证"联动机制;其三,制定细分领域标准(如氢能源储罐粘接检测规范)。通过政产学研协同创新,预计到2030年可实现全行业检测智能化率80%以上,为制造业高质量发展提供坚实技术保障。
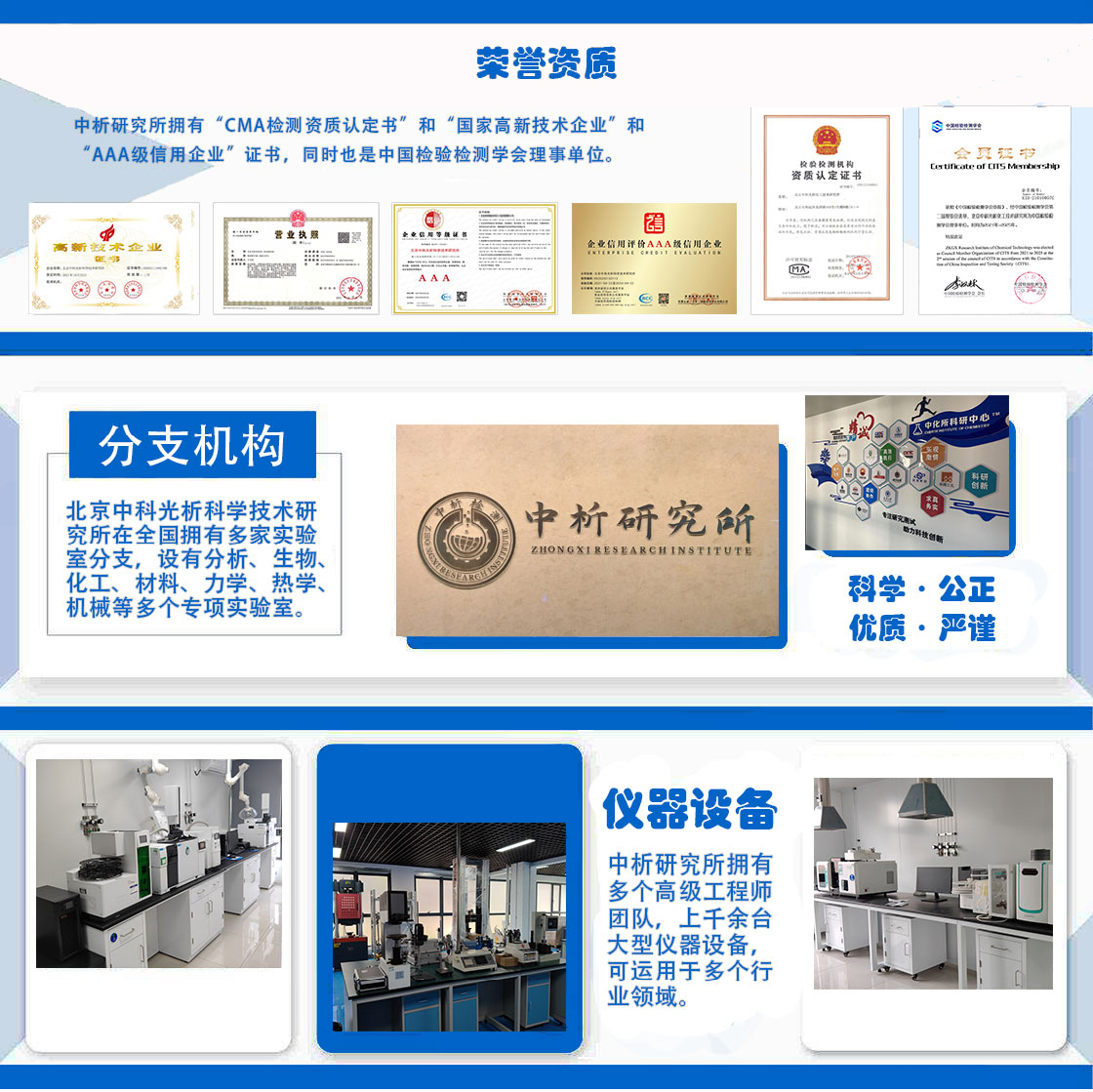
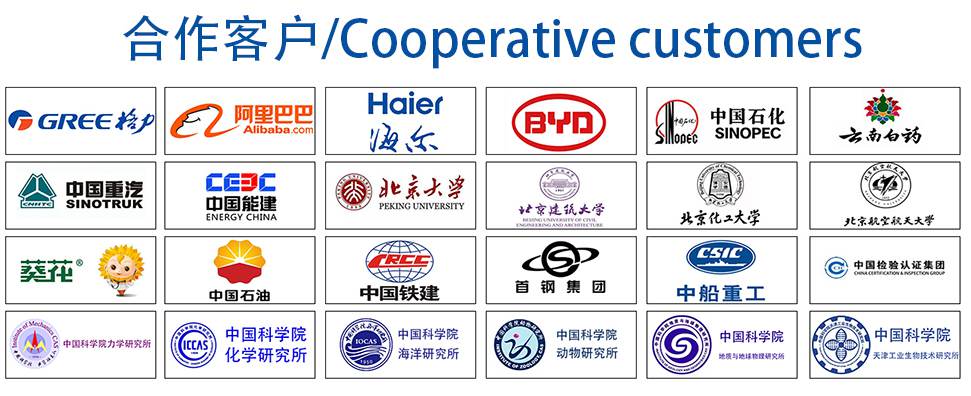