星点检测:核心技术与检测项目详解
一、星点检测的核心检测项目
-
- 检测内容:确定星点的精确坐标(二维或三维空间位置)。
- 技术方法:
- 质心法:通过计算光斑的灰度加权中心确定位置,适用于高信噪比场景。
- 高斯拟合法:利用二维高斯函数拟合光斑分布,提升亚像素级定位精度。
- 应用场景:天文望远镜的恒星定位、工业视觉的元件对位。
-
- 检测内容:量化星点的亮度或能量强度,为后续分类或校准提供依据。
- 挑战:背景噪声干扰、相邻星点重叠(例如星团区域)。
- 解决方案:
- 背景扣除算法:动态估计局部背景并扣除。
- PSF(点扩散函数)反卷积:分离重叠星点的能量分布。
-
- 检测内容:测量星点的半高全宽(FWHM)、椭圆度、对称性等参数。
- 意义:
- 光学系统质量评估(如镜头像差检测)。
- 区分真实星点与噪声(例如:宇宙射线噪点通常呈尖锐非对称形态)。
-
- 检测内容:计算目标信号强度与局部背景噪声的比值。
- 关键公式: SNR=�peak−�mean��SNR=σBSpeak−Bmean 其中,�peakSpeak为星点峰值强度,�meanBmean和��σB分别为背景均值和标准差。
- 应用:天文观测中筛选有效星点,排除低信噪比干扰。
-
- 检测内容:验证检测系统在不同亮度星点下的响应线性度。
- 方法:
- 输入已知强度的模拟星点,检测输出值与理论值的偏差。
- 绘制响应曲线,计算非线性误差(如积分非线性度,INL)。
二、检测流程与关键技术
-
- 去噪滤波:使用小波变换或非局部均值滤波减少随机噪声。
- 平场校正:消除光学系统的不均匀响应(如暗电流、像素灵敏度差异)。
-
- 自适应阈值法:根据局部背景动态调整分割阈值(例如:�=��+���T=μB+kσB,k通常取3-5)。
- 形态学处理:通过开运算去除小面积噪点,填充空洞。
-
- 挑战:密集星场中相邻星点的重叠问题。
- 算法:
- 迭代分解法:交替优化多个高斯模型的参数。
- 深度学习:U-Net等分割网络实现像素级目标分离。
-
- 误检剔除:根据形状、亮度一致性约束过滤异常点。
- 交叉验证:与参考星表(如Gaia DR3)匹配,验证定位精度。
三、行业应用案例
-
- 项目:巡天望远镜(如LSST)的实时星点处理系统。
- 检测指标:单帧处理速度>1000星点/秒,定位误差<0.1像素。
-
- 案例:手机镜头模组的散斑检测。
- 参数要求:检测直径>2μm的缺陷点,漏检率<0.01%。
-
- 应用:X光片中的钙化点检测,需区分血管壁钙化与肿瘤病灶。
- 技术难点:低对比度目标的分割与分类(常用多尺度Retinex增强)。
四、挑战与前沿技术
-
- 解决方案:单光子雪崩二极管(SPAD)传感器结合时间相关计数。
-
- 嵌入式方案:FPGA硬加速质心算法,延迟<1ms。
-
- 趋势:基于Transformer的端到端检测模型(如StarDist),减少人工特征依赖。
五、总结
- Berry, R., & Burnell, J. (2005). The Handbook of Astronomical Image Processing.
- Zhang, K., et al. (2020). Deep Learning for Star Detection in Wide-Field Images. IEEE TIP.
- ISO 9039:2021 Optical systems—Quality evaluation—Star test method.
上一篇:波长准确度及重复性检测下一篇:湿循环试验检测
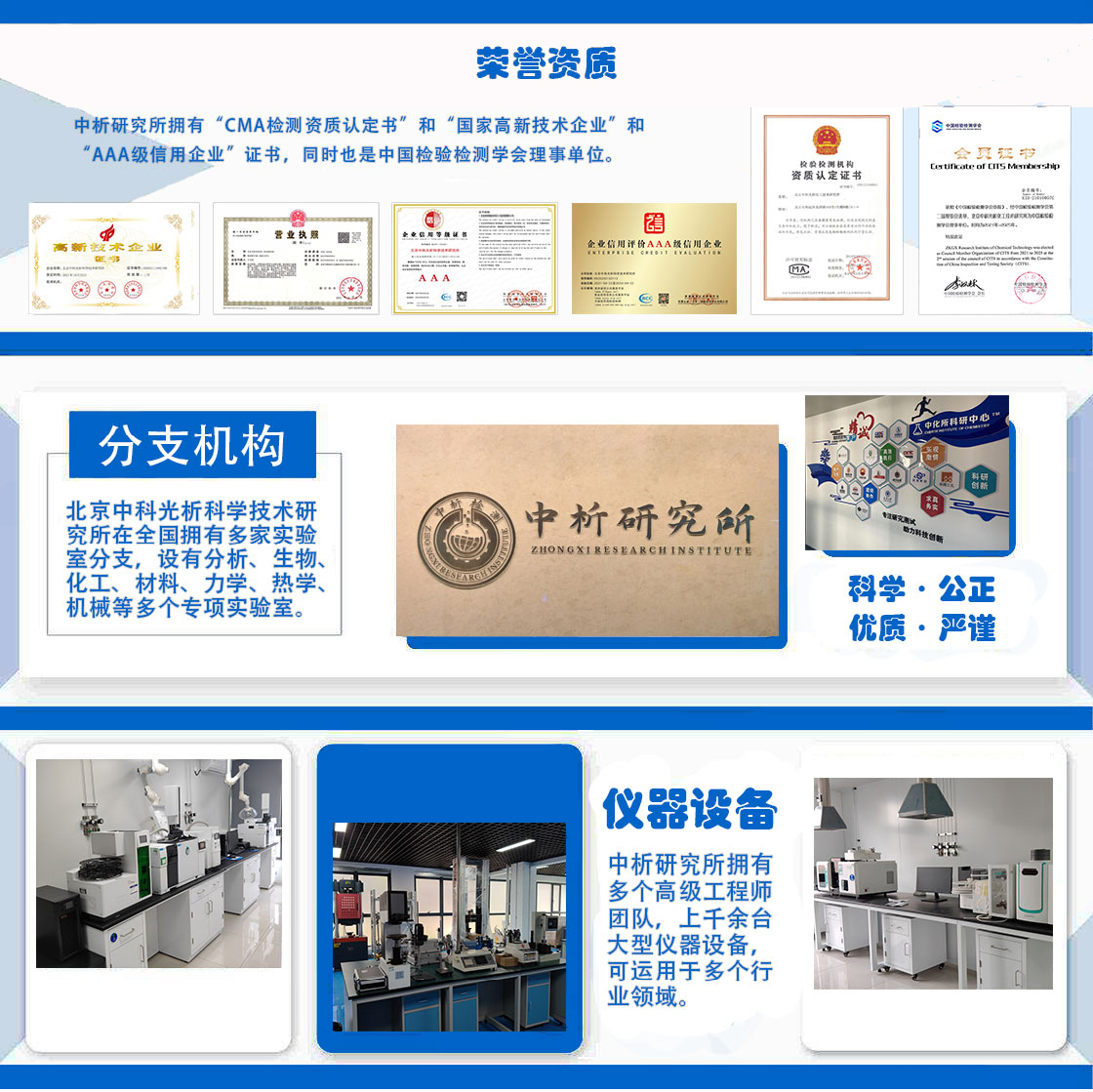
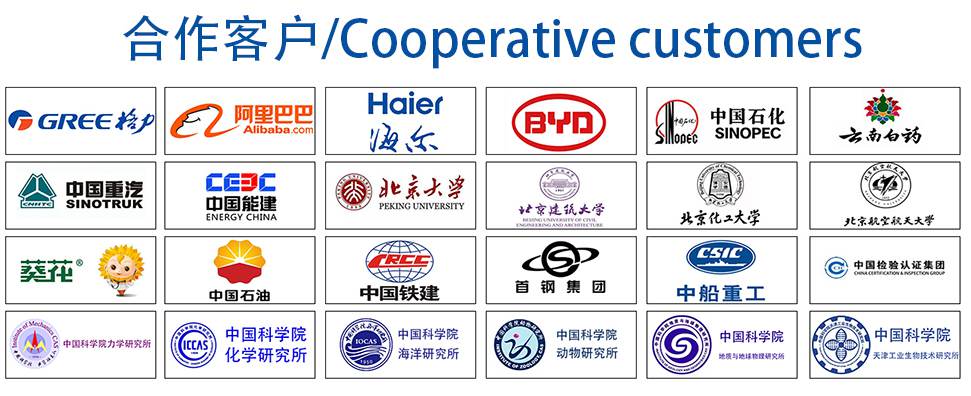
材料实验室
热门检测
14
19
21
17
39
38
44
36
42
42
36
43
36
36
37
42
36
43
37
35
推荐检测
联系电话
400-635-0567