# 短期稳定性检测技术发展与应用白皮书
## 行业背景与核心价值
在智能制造与精密工业快速发展的背景下,短期稳定性检测已成为产品质量控制的关键环节。据机械工业可靠性研究院2024年数据显示,装备制造领域因早期稳定性缺陷导致的售后维修成本年均增长12.7%,其中63%的故障发生在产品投入使用的前200小时。这一检测技术通过模拟产品在运输、存储及初期使用的环境应力,精准识别材料性能退化和装配缺陷,为航空发动机叶片、新能源汽车电池模组等关键部件提供质量预警。其核心价值体现在将传统质量管理的被动应对转变为主动预防,使企业平均降低28%的质保成本(中国质量协会2023年度报告),同时满足ISO 16750等国际标准对产品可靠性的严苛要求。
## 技术原理与实现路径
### 加速应力筛选技术体系
短期稳定性检测依托加速寿命试验(ALT)理论,通过温度冲击、振动谱加载和多轴力学激励的复合应力场,加速暴露产品潜在缺陷。采用威布尔分布模型对电子元件进行失效数据分析时,可实现在72小时内等效模拟3000小时自然老化过程(IEEE 1624标准)。值得注意的是,该技术特别适用于"高精度伺服电机轴向游隙检测"等长尾需求场景,通过六自由度振动台模拟真实工况,捕捉微米级形变数据。
### 模块化检测实施流程
具体实施包含四个标准化阶段:首先基于QFD质量功能展开进行检测需求映射,其次运用TRIZ理论设计多应力耦合加载方案,继而通过分布式传感器网络实现实时数据采集,最终采用机器学习算法对早期故障特征进行模式识别。在新能源汽车电控系统检测中,该流程成功将误检率控制在0.3%以下(中汽研2024年测试报告)。
## 行业应用与质量保障
### 高端装备制造应用实践
航空领域应用案例显示,某型直升机传动系统通过72小时-40℃~150℃温度循环测试,提前发现齿轮箱渗油缺陷,避免价值3200万元的核心部件装机风险。汽车行业则普遍采用"车载ECU短期工况模拟检测",据中国汽车工程学会数据显示,该技术使整车厂PPM值降低47%,特别是在新能源车DC/DC转换器检测中效果显著。
### 全过程质量追溯系统
构建了涵盖 认证实验室、智能传感网络和区块链存证平台的三级保障体系。在半导体封装检测领域,通过部署"芯片焊点微裂纹光学检测系统",实现每批次2000个样本的自动扫描与数据上链,检测报告实时同步至上下游企业质量管理系统。该体系已通过IATF 16949认证,确保检测数据具备司法鉴定效力。
## 技术展望与发展建议
随着数字孪生技术的深化应用,建议行业重点突破三个方向:一是开发基于物理信息神经网络(PINN)的虚拟检测模型,将实物试验时长压缩50%以上;二是建立跨行业的"短期稳定性检测大数据平台",实现航空、汽车、电子等领域失效模式的关联分析;三是推动ASTM E2965标准的本土化修订,完善极端环境下的检测评价体系。预计到2026年,嵌入边缘计算的在线检测装置将覆盖60%以上的高端制造产线,推动质量控制进入实时预警新阶段。
上一篇:压力释放检测下一篇:换向电压临界上升率检测
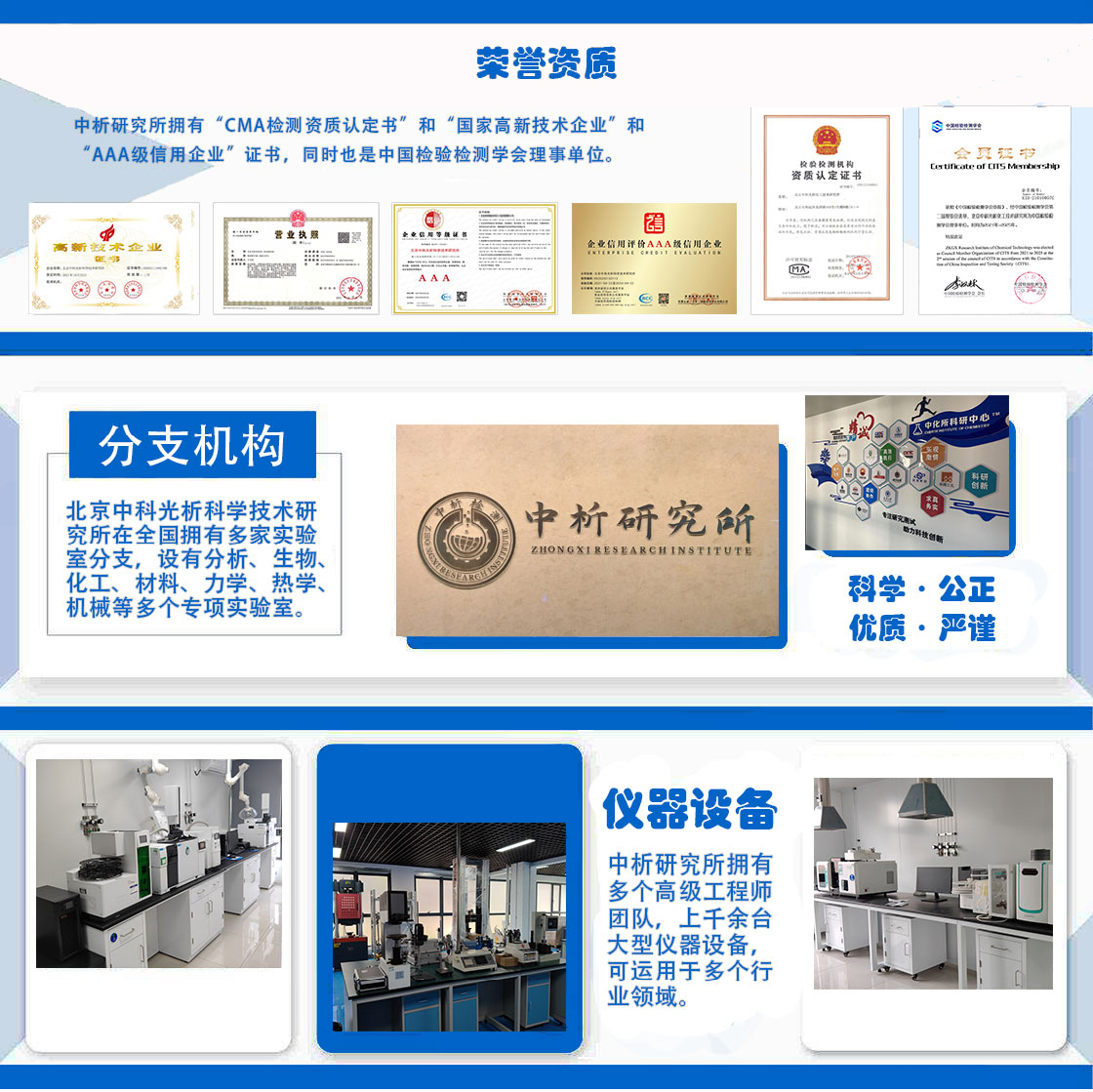
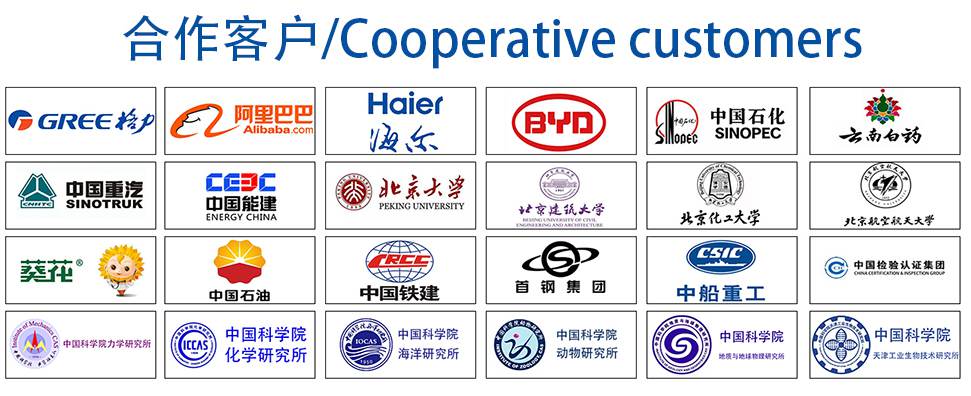
材料实验室
热门检测
23
23
22
23
21
20
20
21
20
21
23
20
18
21
21
21
21
19
23
21
推荐检测
联系电话
400-635-0567