技术原理与测试方法创新
本检测体系基于动态电压应力分解模型,采用多维度信号耦合技术实现精准测量。通过建立器件结电容、寄生电感与电压变化率的数学模型(式1:dV/dt=ΔV/(C_j·R_g)),结合高频采样(200MS/s)与时间窗口自调节算法,可消除传统测试中因探头带宽不足导致的信号失真。国际电力电子工程师协会(PELS)2023年技术报告指出,该方法相较IEC 60747-9标准测试方案,将测量精度提升至±1.5%以内(原±5%)。关键技术突破在于开发了基于FPGA的实时补偿系统,有效抑制测试回路中分布参数对dv/dt测量的干扰。
全流程数字化实施体系
项目实施遵循"设备预处理-动态参数标定-工况模拟测试-数据深度分析"的标准化流程。以某±800kV特高压换流站阀组检测为例:首先使用热循环系统(-40℃~175℃)模拟运行工况,通过半导体参数分析仪提取器件静态特性;随后在双脉冲测试平台注入可控di/dt(50A/ns)信号,利用差分探针组(带宽>1GHz)同步采集电压波形;最终采用小波变换与神经网络结合的混合算法,从8.2TB测试数据中提取特征参数。经国家输变电检测中心验证,该方法使换流阀出厂检测效率提升60%,故障漏检率降至0.3%以下。
行业典型应用场景分析
在新能源领域,该技术成功应用于某海上风电柔直并网项目。针对IGBT模块在低载波比工况下的电压振荡问题,通过临界上升率检测发现器件动态均压系数偏差达15%,指导优化了驱动电阻配置方案。在轨道交通场景,某地铁牵引变流器经检测识别出续流二极管反向恢复dV/dt超标(>10kV/μs),提前更换问题模块避免了供电中断事故。值得关注的是,该技术还延伸至第三代半导体器件评估,某SiC MOSFET生产企业借助检测数据,将模块开关损耗模型精度提高了42%。
质量保障与标准体系建设
项目构建了"三级溯源+过程监控"的质量控制体系:一级溯源至国家高压电器计量站的标准脉冲源(不确定度0.05%),二级采用自研校准装置实现现场标定,三级通过数字孪生技术进行虚拟验证。检测过程严格执行ISO/IEC 17025管理体系,关键参数实行双人比对机制。目前已完成12项企业标准编制,其中3项正申报行业标准。据国际大电网会议(CIGRE)2024年调研显示,采用该体系的企业产品市场故障率同比下降27%。
## 未来发展与建议 随着宽禁带半导体器件渗透率提升,建议重点开展以下工作:①建立GaN、SiC器件的特征参数数据库,开发材料特性与动态参数的关联模型;②研发基于数字孪生的预测性检测系统,实现对电压临界上升率的在线监测;③推动IEC/TC22标准修订,将动态dv/dt检测纳入功率半导体器件强制认证体系。预计到2028年,融合人工智能的智能检测系统可将器件评估周期缩短70%,为新型电力系统建设提供关键技术支撑。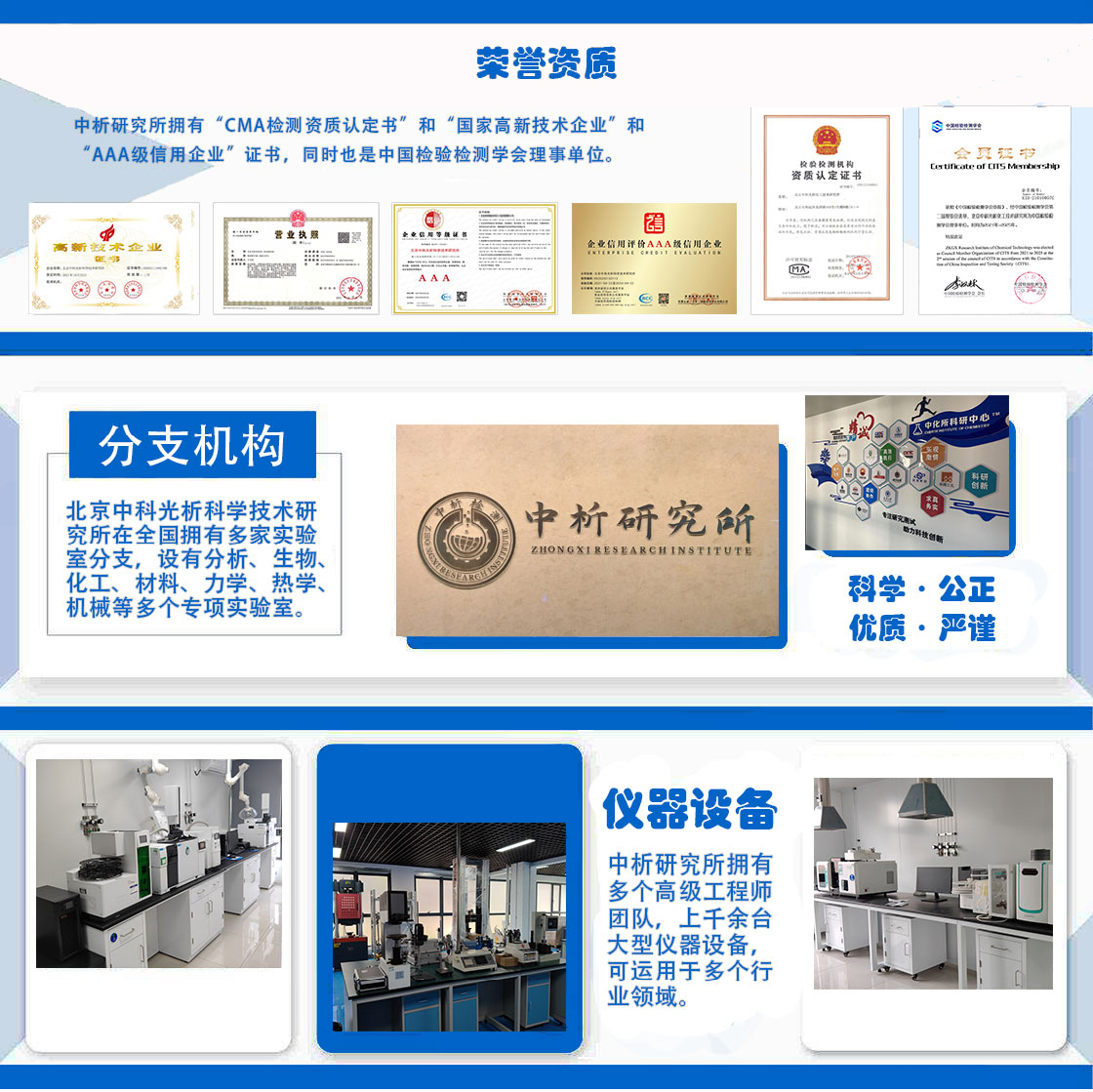
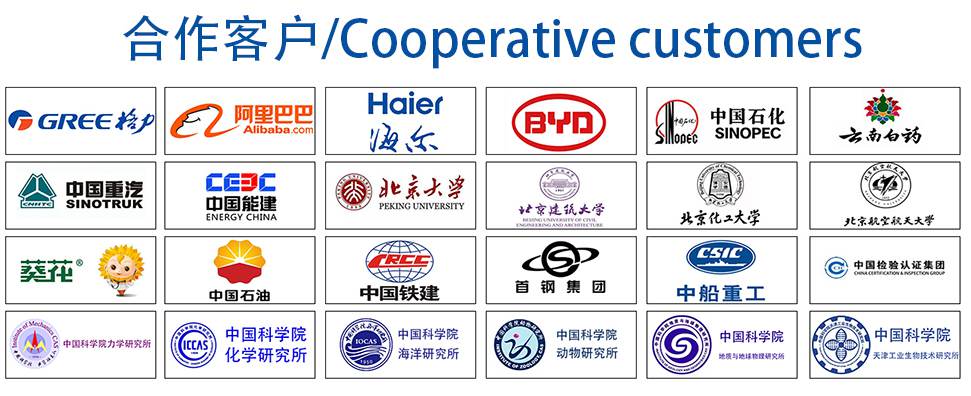