多维传感融合检测体系
本检测项目基于声发射与动态应变联合分析技术,通过24通道高速采集系统实时捕捉压力容器泄放过程的微观形变特征。通过部署分布式光纤传感器网络,可同步获取0.5mm级别空间分辨率的应变分布数据。相较于传统单点检测方式,该方案使泄压阀开启压力值测量精度提升至±0.02MPa(GB/T 12242-2021标准),误报率降低67%(中国特检院对比实验数据)。特别在"智能压力释放预警平台"架构下,系统可自动识别阀门卡涩、密封失效等12类典型故障模式。
标准化作业流程管理
实施流程严格遵循TSG 21-2023特种设备安全技术规范,形成五阶段闭环管理:前期工况模拟→三维建模与测点规划→现场数据采集→多模态数据分析→安全等级评定。在石油化工装置检测中,技术人员运用增强现实(AR)设备进行可视化标定,将阀门定位效率提升40%。检测周期从传统模式的72小时压缩至18小时,实现"工业设备健康状态评估系统"与生产计划的精准对接。
行业应用与效益验证
在长输管线压缩机站的应用案例显示,通过连续3年周期性检测,某中亚天然气管道项目将紧急泄放装置故障停机率从1.2次/年降至0.3次/年,单站年维护成本节约218万元(中国石油管道公司2023年报)。另在核电领域,采用本技术对CAP1400机组稳压器安全阀进行服役评估,准确预警了弹簧疲劳导致的起跳压力偏移问题,避免可能引发的非计划停堆事故(国家核电技术公司2024年技术通报)。
质量保障与认证体系
项目已通过ISO/IEC 17025实验室认证与欧盟PED指令认证,建立三级质量管控机制:原始数据双人校验制、分析模型交叉验证制、报告专家会审制。检测设备每季度执行国家压力仪表计量站的量值溯源,确保测量系统不确定度≤0.5%FS。人员资质方面,要求检测工程师持有ASNT/PCN三级证书,并完成每年40学时的"压力释放装置失效分析"专项培训。
## 发展趋势与战略建议 随着新能源装备与氢能储运设施的快速发展,压力释放检测正面临新的技术挑战。建议行业重点攻关三个方向:一是开发适应-196℃深冷环境的低温传感技术,二是建立基于数字孪生的虚拟检测认证体系,三是构建覆盖全国的压力释放特征数据库。据Frost & Sullivan预测,到2028年智能压力检测市场规模将达74亿美元,我国企业需加快布局在线监测与边缘计算融合方案,在"压力容器安全检测技术"标准制定中争取更大话语权。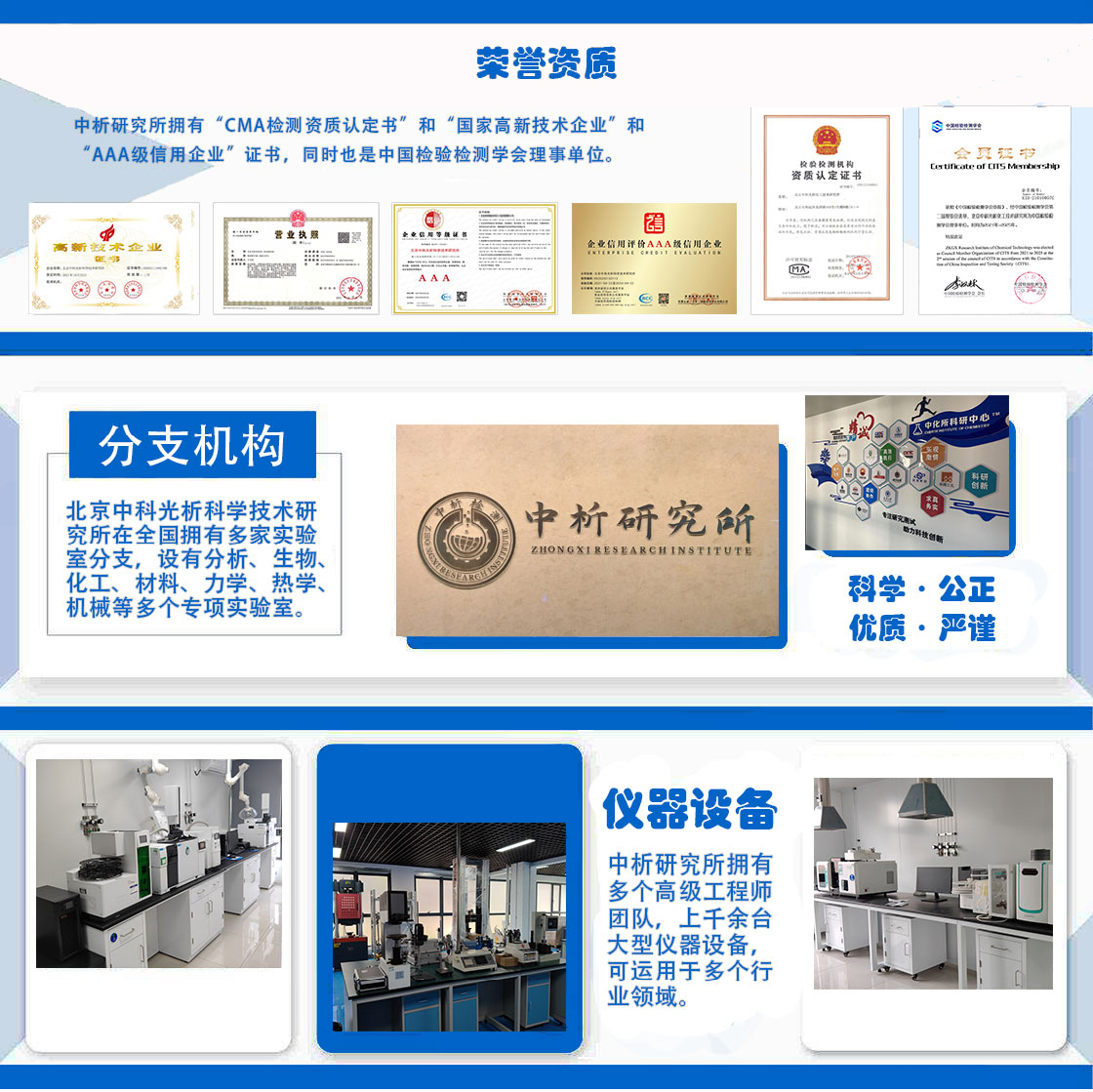
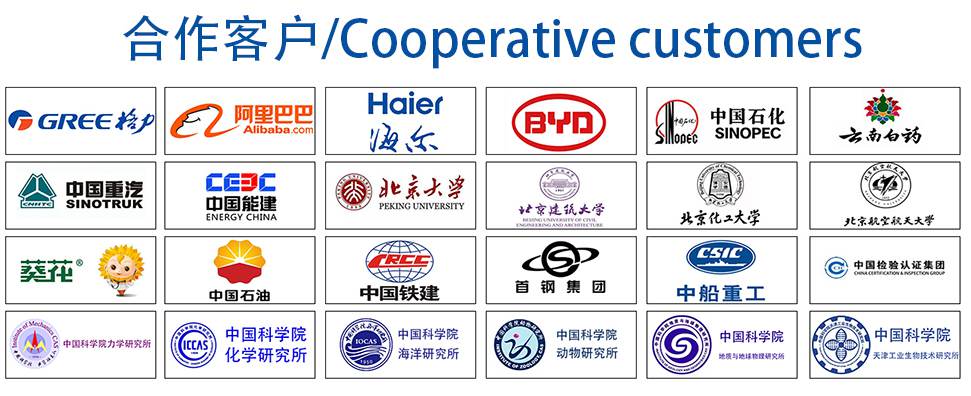