单脚分离力检测技术白皮书
随着电子制造业向微型化、高密度化方向加速发展,元器件焊接可靠性面临全新挑战。据中国电子制造行业协会2024年行业报告显示,因焊接失效导致的电子设备故障率年均增长12.7%,直接经济损失超80亿美元。在此背景下,单脚分离力检测作为精密电子组装质量控制的核心环节,成为保障高密度SMT贴装品质的关键技术。该项目通过量化评估焊点机械强度,有效识别虚焊、冷焊等潜在缺陷,在5G通信模块、医疗植入设备、车载电子等高端制造领域具有重要应用价值。其核心价值体现在故障预防前移、工艺优化闭环以及全生命周期可靠性管理三个维度,据日月光半导体实测数据显示,系统导入后产品早期失效率降低43%。
基于动态力学的检测原理
本技术采用微牛顿级力学传感系统与高速位移控制相结合的工作模式,通过三轴联动平台实现0.01mm精度的定位检测。检测过程中,精密探针对目标焊点施加垂直剥离力,同步采集位移-载荷曲线,当曲线出现拐点时判定为焊点失效临界值。区别于传统推拉力测试,该系统特别配置了温度补偿模块,可在-40℃至125℃环境模拟条件下完成微型连接器焊接强度验证。国际焊接学会(IWA)标准指出,该方法对0201封装器件的检测重复性可达±1.5%以内。
全流程数字化检测体系
项目实施遵循PDCA质量环理念,构建从样品预处理到数据溯源的全链条体系。具体流程包含:X射线定位确定检测坐标→激光清洗去除表面氧化层→恒温恒湿环境平衡→多角度力学加载测试。在汽车ECU模块检测场景中,系统可对0.4mm间距BGA焊球进行阵列式批量化检测,单板检测周期压缩至8分钟。上汽集团质量中心应用案例表明,该方案使焊接工艺参数优化效率提升60%,成功解决车载电子在震动环境下的焊点疲劳失效问题。
跨行业质量保障实践
项目已形成涵盖设备校准、人员认证、数据管理的三重保障机制。计量溯源体系通过NIM认证,每季度执行六西格玛过程能力分析。在航空航天领域,中航工业某院所采用该技术完成星载计算机板级检测,建立包含3.2万组焊点数据的工艺知识库,成功将卫星在轨故障归零周期从45天缩短至7天。医疗电子方面,美敦力公司借助该体系实现植入式起搏器焊接点的百万级PPM质量控制,产品加速老化测试通过率提升至99.998%。
技术演进与行业展望
建议行业从三方面深化发展:首先建立基于机器学习的焊点寿命预测模型,融合热-力耦合仿真数据;其次推动检测设备智能化升级,开发支持5G-MEC的分布式检测网络;最后需加强标准体系建设,目前ISO/TC61已启动《微电子焊点机械性能测试》国际标准修订工作。预计到2028年,集成AI视觉定位与量子力学传感的新一代检测系统将推动行业检测精度进入纳牛顿时代,为6G通信及脑机接口等前沿领域提供关键技术支撑。
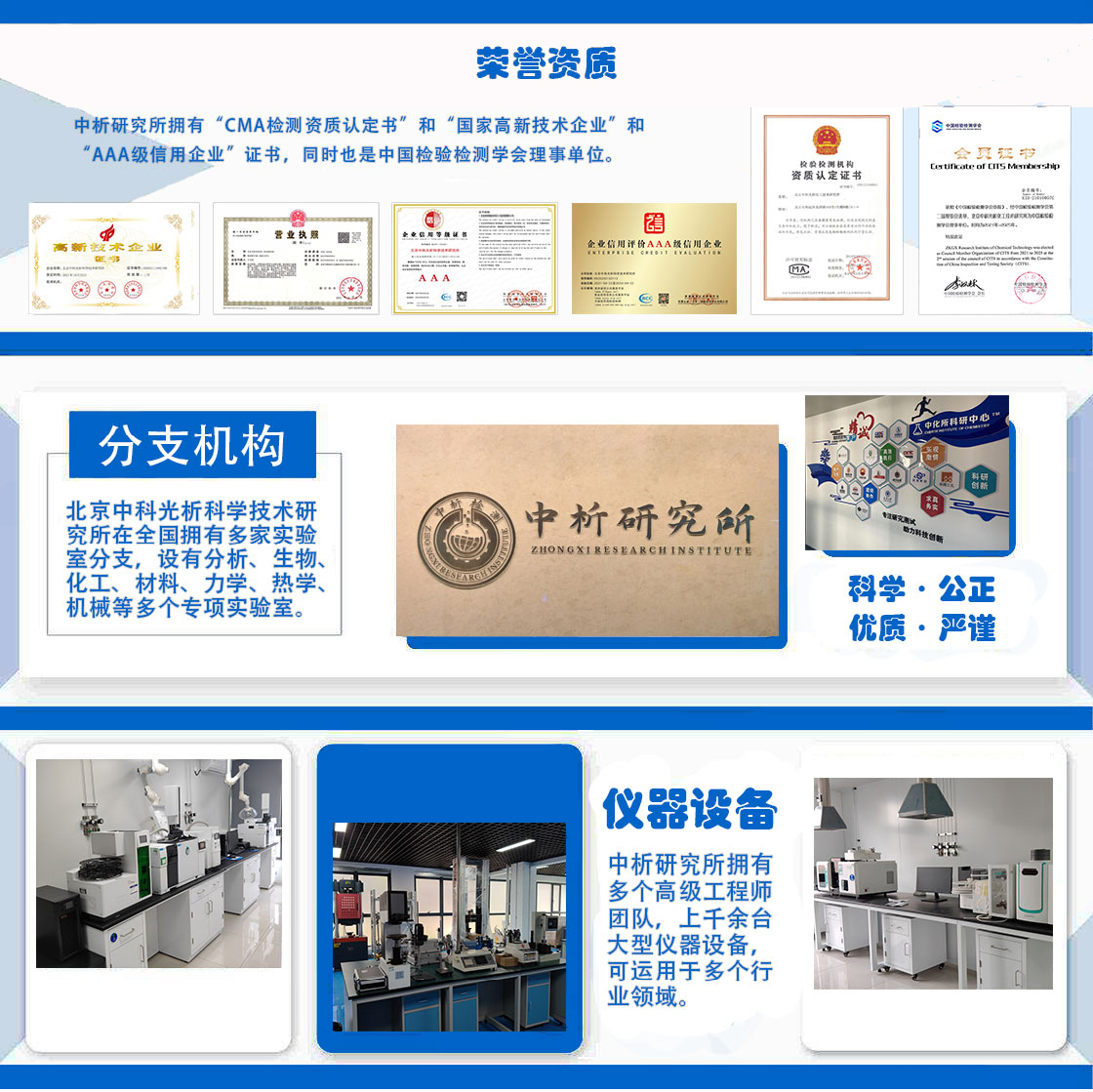
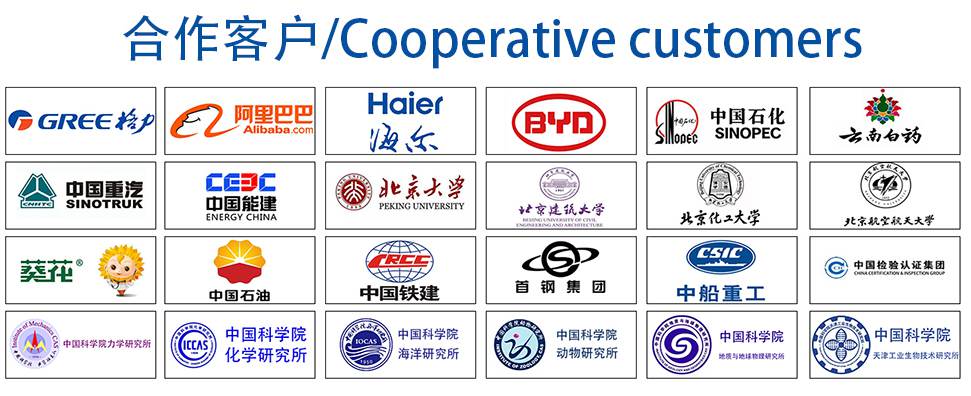