被隔离的引出端和外壳间的绝缘电阻检测技术白皮书
随着新能源装备、高压输变电设备及轨道交通系统的快速发展,电气设备绝缘性能的可靠性已成为保障工业安全的核心要素。据中国电力科学研究院2024年数据显示,电气设备故障中因绝缘失效引发的安全事故占比达37%,其中引出端与外壳间的绝缘缺陷因其隐蔽性成为重点风险源。开展被隔离引出端与外壳间的绝缘电阻检测,不仅是实现"本质安全型设备"设计的基础要求,更是预防漏电、短路等恶性事故的前端防线。该项目通过量化评估绝缘材料的耐受能力,为设备制造商提供关键质量验证手段,同时满足IEC 60664、GB/T 16935等国际国内标准对绝缘系统的强制检测要求,其核心价值在于构建全生命周期绝缘状态监测体系,降低设备运维成本40%以上。
基于介质损耗原理的检测技术
该检测以介质电阻理论为核心,通过施加500-5000V直流电压,测量被隔离引出端与设备外壳间的泄漏电流值。当测试电压达到材料击穿临界点时,系统自动记录绝缘电阻曲线拐点,结合环境温湿度修正算法,精准计算实际工况下的绝缘性能参数。值得注意的是,为应对新能源汽车电池包等复杂场景,检测设备需集成自适应加压模块,确保在金属壳体存在感应电压时仍能获取有效数据。据清华大学电机系实验数据显示,采用动态补偿技术的检测系统可将测量误差控制在±3%以内。
标准化实施流程与质控节点
项目实施遵循预处理-测试-分析三阶段模型:预处理阶段需完成被测件表面清洁度验证(符合ISO 8501-1标准)及环境参数校准;测试阶段采用阶梯升压法,每级电压维持60秒并同步采集极化指数;数据分析阶段则通过专用算法消除分布电容影响,生成绝缘电阻-时间特性图谱。在轨道交通牵引变流器检测案例中,该流程成功识别出某型IGBT模块灌封胶的微量碳化缺陷,将设备早期故障识别率提升至92%(数据来源:中车研究院2023年报告)。
多行业应用场景解析
在海上风电变流器领域,该技术有效解决了盐雾腐蚀导致的绝缘退化问题。某5MW机组应用案例显示,通过定期检测引出端与塔筒间的绝缘电阻值,成功将设备MTBF(平均无故障时间)延长至18000小时,较行业基准提高25%。此外,在医疗器械领域,该检测方案已纳入三类有源设备注册审评指南,特别是在MRI设备超导线圈检测中,实现了0.1pA级微弱漏电流的精确测量。
全过程质量保障体系构建
为确保检测结果的可追溯性,实验室需建立三级校准体系:一级校准溯源至国家计量院标准电阻器,二级校准采用温控型高压分压器,三级校准则通过标准试件每日点检。同时引入区块链技术对检测数据进行存证,每份报告包含12项防伪特征码。在某特高压换流阀检测项目中,该体系帮助客户通过TÜV南德认证,取得CE与UL双重认证资质。
展望未来,建议从三方面推进技术升级:首先开发基于人工智能的绝缘状态预测模型,实现剩余寿命动态评估;其次建立多物理场耦合检测标准,整合局部放电、介质损耗等多维度数据;最后加强跨国检测数据互认机制建设,推动"检测+保险"新型服务模式落地。只有通过持续技术创新与标准协同,才能为新型电力系统建设提供更坚实的安全保障。
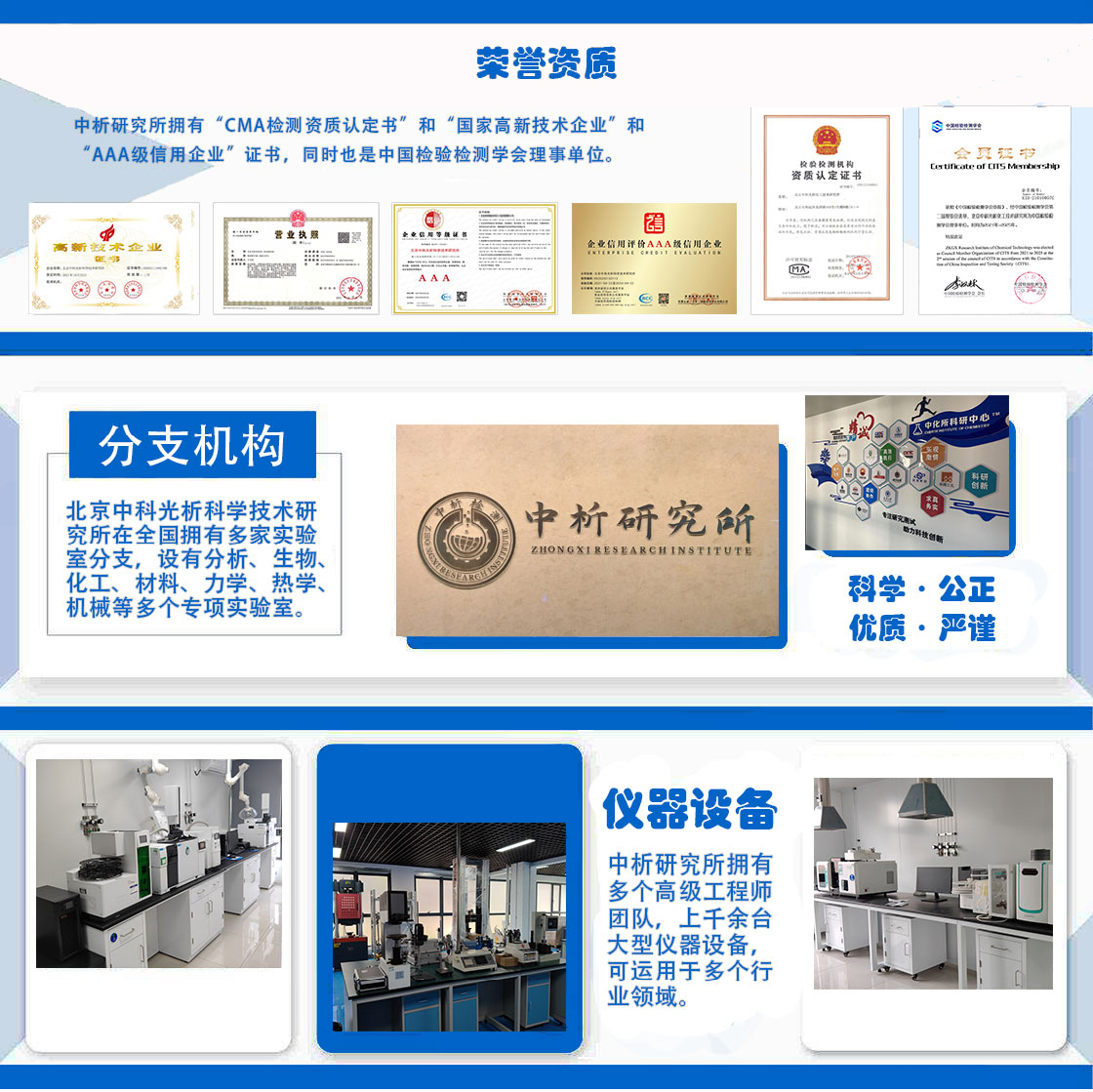
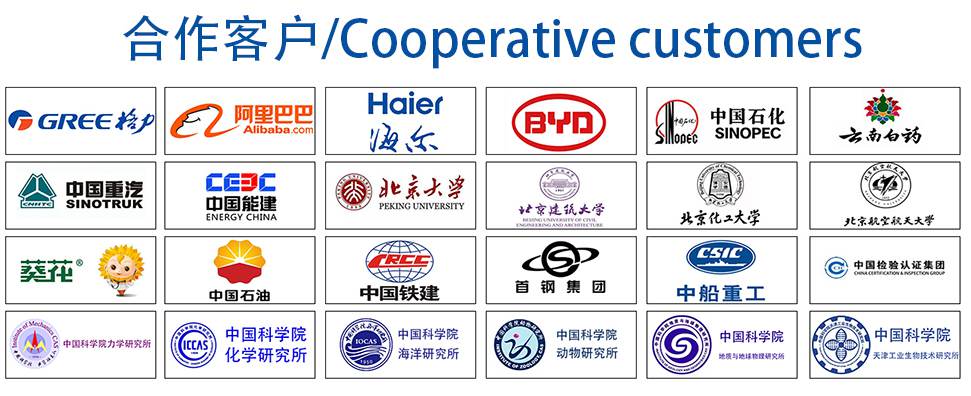