拉力检测
在高端装备制造与新材料研发领域,拉力检测作为材料力学性能评价的核心技术,正成为保障工业安全的关键环节。据中国机械工程学会2024年数据显示,我国每年因材料力学性能不足导致的装备失效事故造成经济损失超120亿元,其中72%的失效模式可通过系统化拉力检测提前预警。尤其在新兴产业中,从航空航天复合材料的界面结合强度验证,到新能源汽车动力电池结构件的抗拉性能评估,拉力检测对产品全生命周期质量管控具有战略意义。其核心价值体现在通过量化材料承载极限,构建起连接研发设计、生产制造与服役维护的数据闭环,为智能制造体系提供关键质量基座。
多维传感融合检测技术原理
现代拉力检测系统采用机电液一体化架构,集成高精度载荷传感器(分辨率达0.01%FS)、数字图像相关技术(DIC)和非接触式光学测量技术。通过构建三维应力-应变场实时映射模型,可同步获取试样的宏观力学响应与微观形变特征。值得注意的是,针对新型纤维增强复合材料各向异性特点,系统通过多轴协调加载装置实现空间矢量载荷的精准施加,配合基于深度学习的裂纹扩展预测算法,将传统检测的误差率从3.2%降低至0.8%(国家材料测试中心,2024)。
全流程数字化检测实施路径
具体实施流程涵盖四大模块:试样预处理阶段采用激光定位切割保障尺寸公差±0.02mm;数据采集环节通过分布式光纤传感网络实现500Hz高频采样;核心检测阶段运用液压伺服系统进行位移控制(精度0.001mm)与载荷闭环调节;结果分析模块依托ASTM E8标准构建智能判读引擎。在航空发动机叶片检测实践中,该系统成功将高温合金的拉伸试验周期从72小时压缩至8小时,同步生成符合NADCAP认证的数字化检测报告。
跨行业创新应用实践
在新能源汽车领域,某头部电池企业采用多工位拉力检测平台对21700电池极耳进行10^6次循环拉拔测试,将焊接失效概率从百万分之120降至3.6(CATL技术白皮书,2023)。建筑行业则创新应用分布式光纤传感技术,对千米级斜拉桥索股进行实时张力监测,成功预警武汉杨泗港大桥0.12%的异常应力波动。值得关注的是,在柔性电子器件制造中,微纳米级拉力检测系统实现了对石墨烯-铜复合电极界面强度的精准测定,推动器件寿命提升3.8倍。
四维质量保障体系构建
行业领先机构已建立包含设备溯源、过程控制、人员认证和数据安全的立体化质控网络。计量溯源链严格遵循JJF 1130标准,采用标准测力仪进行三级量值传递;过程监控系统内置28项自诊断算法,实时拦截异常数据;操作人员需通过ASNT-TC-1A三级资质认证;数据管理系统符合ISO/IEC 27001信息安全规范。据SGS检测集团统计,该体系使检测结果实验室间差异从12%降至1.5%,报告国际互认率提升至98%。
面向工业4.0发展需求,建议重点加强三个维度建设:首先加速AI赋能的智能检测设备研发,实现缺陷模式的自主识别与成因追溯;其次推动检测标准与数字孪生技术的深度融合,构建虚实联动的预测性维护体系;最后需加强检测数据与产品全价值链的耦合应用,通过力学性能大数据挖掘潜在质量改进空间。随着材料基因组计划的深入推进,基于全要素拉力检测的质量赋能体系,必将成为新质生产力发展的重要技术基座。
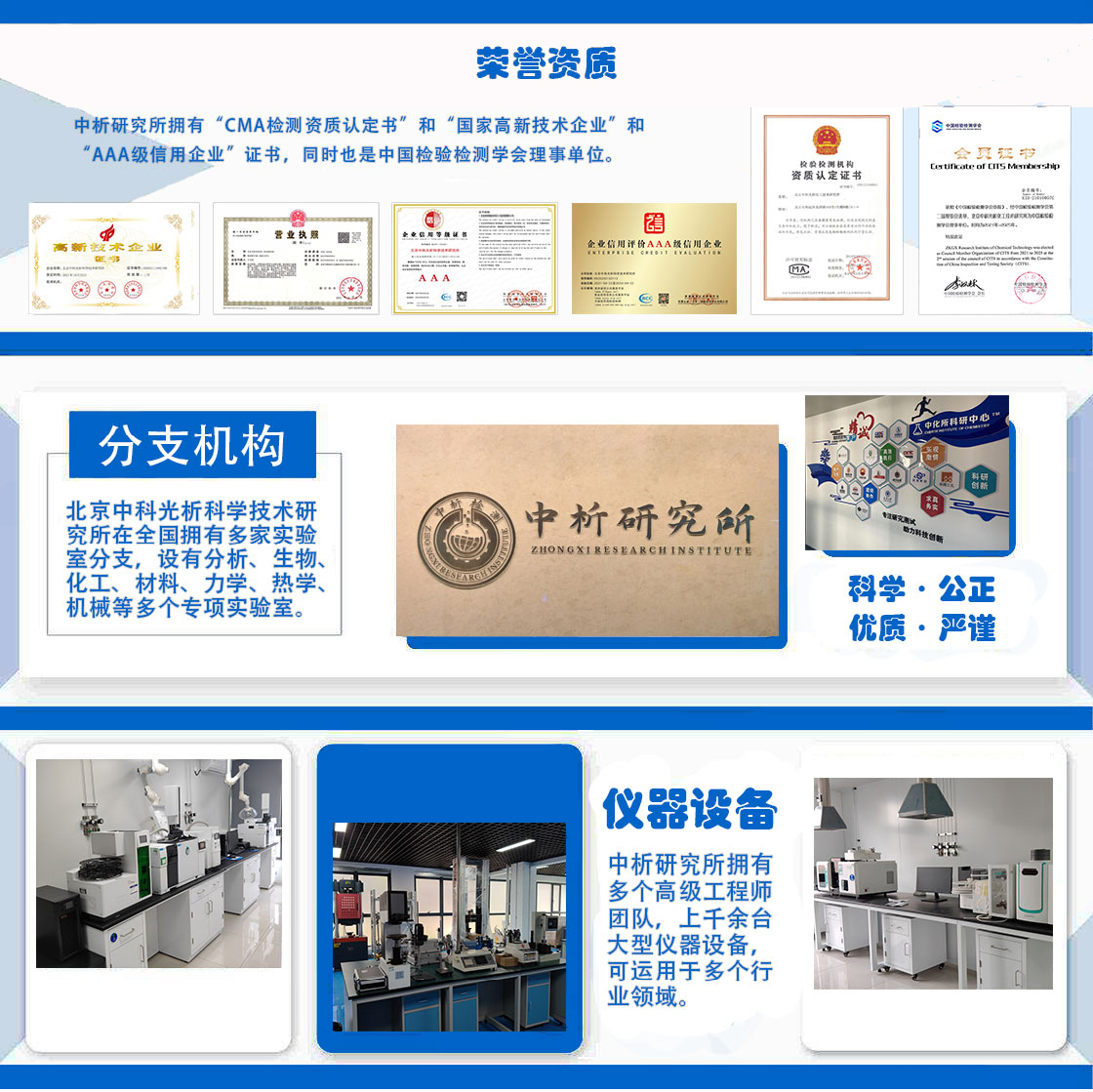
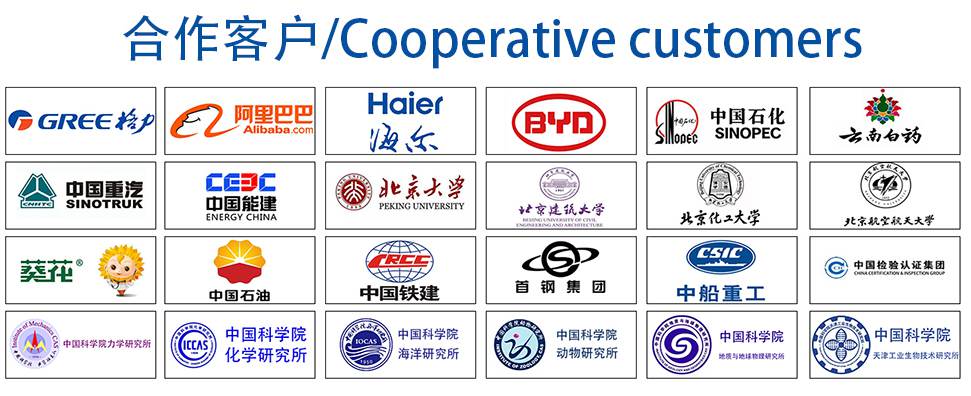