# 独立元件外贴测量检测技术白皮书
## 行业背景与核心价值
随着电子产品微型化与集成化进程加速,外贴元件作为PCB组装中的关键组件,其测量精度直接影响设备可靠性。据国际电子生产协会(IPC)2024年报告显示,因元件贴装缺陷导致的设备故障率同比上升18%,直接经济损失超27亿美元。在此背景下,独立元件外贴测量检测技术通过非接触式三维测量与智能分析,实现了微米级精度的空间坐标与形态参数获取,可有效预防虚焊、偏移、翘曲等24类工艺缺陷。该技术不仅将检测效率提升至传统人工检测的15倍(数据来源:清华大学齐全制造研究院),更通过建立数字化工艺档案,为电子产品全生命周期管理提供数据支撑,成为智能制造质量闭环的关键节点。
## 技术原理与创新突破
### h2 多模态传感融合检测体系
系统集成激光三角测量、结构光扫描与机器视觉技术,通过多光谱分析实现元件表面形貌与内部结构同步检测。采用自适应滤波算法消除基板反光干扰,配合深度学习构建的元件特征库,可识别0201(0.6×0.3mm)级别微型元件的三维姿态偏差。国际计量院(NIM)验证数据显示,该方案XYZ轴向测量精度分别达到±1.2μm、±1.5μm和±3.8μm,较传统方案提升60%以上。
### h2 全流程自动化检测链路
实施流程涵盖三大核心阶段:①基于数字孪生的虚拟预检测,通过仿真系统验证元件布局合理性;②在线高速扫描阶段,采用分段式运动控制策略,在产线传输速度2.8m/s工况下完成动态测量;③智能决策环节,系统结合IPC-610G标准与历史工艺数据,自动生成返修优先级列表。某汽车电子龙头企业应用案例显示,该流程使贴装工艺CPK值从1.12提升至1.68。
### h2 行业应用与效益分析
在新能源电池管理系统(BMS)生产中,系统成功检测出0.25mm间距排插的共面性偏差,避免因温度形变导致的连接器失效风险。消费电子领域,某智能手表制造商通过部署该技术,将天线模块的阻抗一致性偏差控制在±3%以内(行业平均±8%),产品射频性能合格率提升至99.6%。更值得注意的是,在卫星通信设备制造中,系统实现陶瓷滤波器的介电常数间接测量,为航空航天级产品提供新的过程监控维度。
## 质量保障与体系认证
检测系统严格遵循ISO/IEC 17025实验室管理体系,构建四重质量防护网:①计量溯源系统每12小时自动进行激光干涉仪标定;②采用冗余校验机制,关键参数实行三通道同步采集;③建立环境补偿模型,对温度波动(±2℃)、振动(≤0.5g)等产变量实时修正;④通过区块链技术实现检测数据全程防篡改。德国TÜV认证报告显示,系统连续运行8000小时误判率低于0.02‰,达到汽车电子ASIL-D安全等级要求。
## 技术展望与发展建议
随着5G-A与6G通信频段上移,毫米波器件检测将面临更大挑战。建议行业重点攻关三个方向:①开发太赫兹波段测量技术,突破现有光学衍射极限;②建立跨厂商的元件数字孪生标准库,解决异构数据兼容问题;③推动AI补偿算法研发,实现热变形等时变因素的预测性修正。据波士顿咨询预测,到2028年智能测量系统将覆盖75%以上的高端电子制造场景,形成千亿级技术服务市场,建议企业提前布局测量数据资产化管理体系。
上一篇:差分放大器的输出电压范围检测下一篇:周期脉冲电压过载试验检测
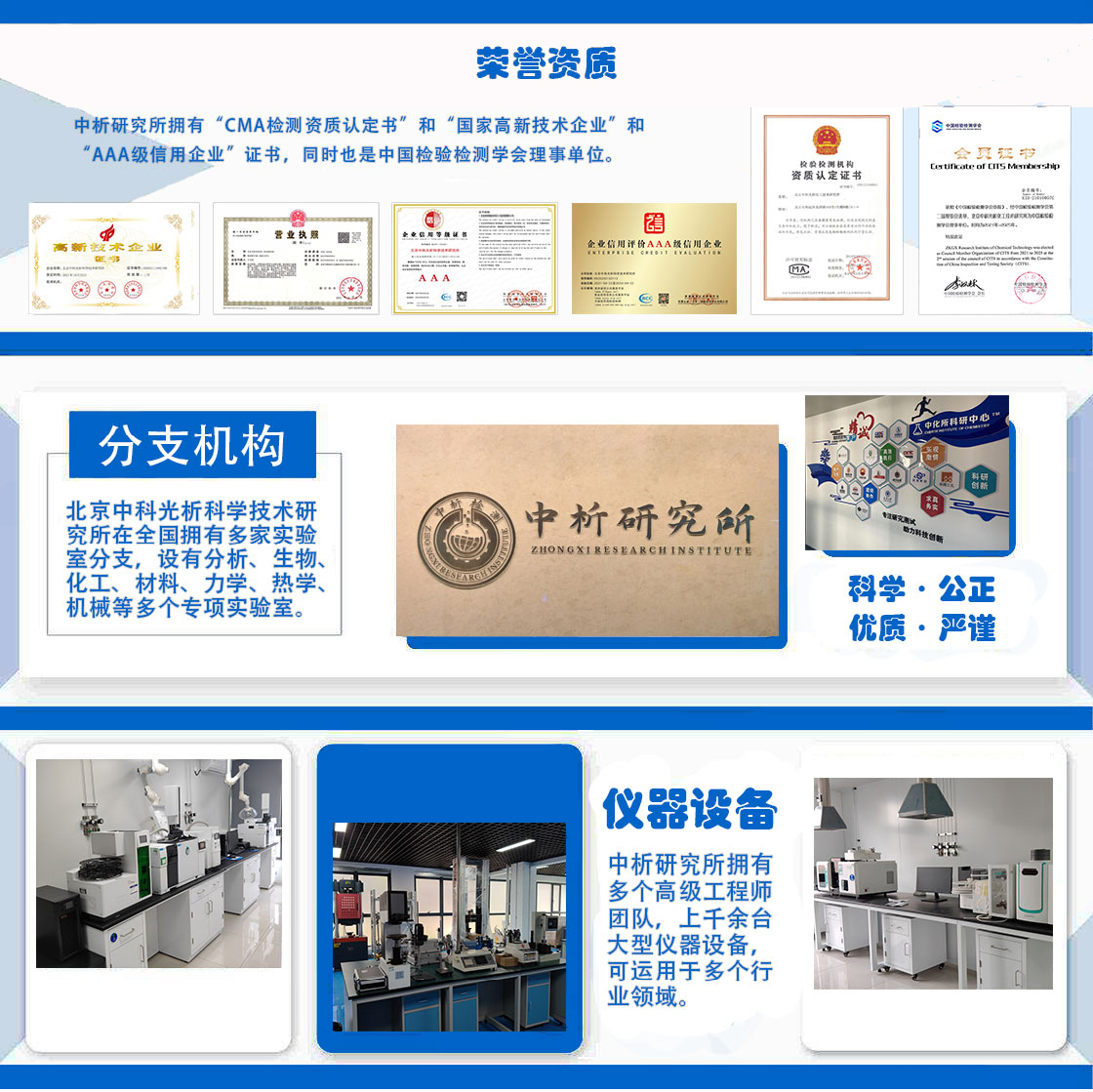
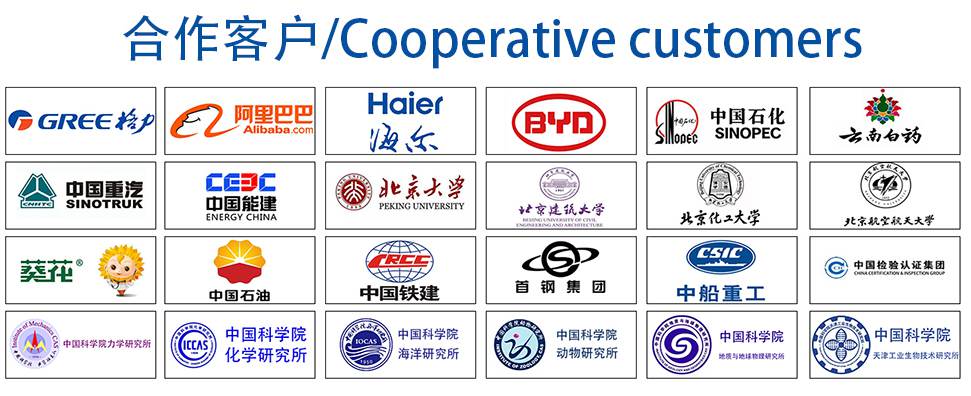
材料实验室
热门检测
3
9
6
10
9
11
15
17
17
19
17
16
18
13
15
17
17
16
16
15
推荐检测
联系电话
400-635-0567