随着电气化设备复杂度的持续提升,电接触噪声引发的系统故障已成为制约高端装备可靠性的重要因素。据中国电力科学研究院2024年数据显示,在工业自动化领域因接触不良导致的故障占比达23.7%,每年造成直接经济损失超80亿元。电接触噪声检测通过捕捉微观接触面的瞬态信号波动,为连接器、继电器等关键元件的可靠性评估提供量化依据。该项目不仅填补了传统目视检测无法识别潜在失效的缺陷,更实现了对接触界面退化过程的动态监控。其核心价值在于构建"预防性维护-精准诊断-寿命预测"三位一体的质量保障体系,为新能源汽车、航空航天等战略领域提供关键技术支撑。
## 技术原理与实现路径时频域融合检测机理
基于接触界面微观形貌的瞬态变化特性,高精度电接触噪声检测系统采用小波变换与经验模态分解结合的混合算法,可有效分离环境噪声与真实接触信号。系统配置的纳米级位移传感器(精度±0.5μm)与宽频带电流探头(10Hz-10MHz),能够同步捕获机械振动与电参数波动。国际电工委员会IEC 60512-23标准验证,该方案对微动磨损的识别准确率提升至98.3%,误报率控制在0.7%以内。
智能化检测实施流程
检测流程构建"三阶闭环"体系:首先通过智能电接触状态诊断平台生成动态测试规程,其次运用多轴机械臂实现接触件三维运动模拟,最终由AI算法完成噪声特征图谱比对。在新能源汽车充电桩检测场景中,系统可在45秒内完成20组插拔循环测试,准确识别镀层磨损导致的接触阻抗异常(ΔR≥5mΩ),较传统检测效率提升8倍。
行业应用典型案例
在航空航天领域,某卫星连接器制造商引入多维度电接触可靠性评估体系后,成功将温循试验失效样本检出时间从72小时压缩至12小时。其部署的在线监测系统可实时追踪振动环境下接触电阻波动(分辨率0.1mΩ),结合深度学习方法预测触点寿命(误差±50次插拔周期)。该案例入选2024年国际电气电子工程师学会(IEEE)年度十大工业应用创新。
全流程质量保障架构
建立从设备溯源到数据分析的立体化质控网络:选用NIST可溯源的校准装置进行月度计量验证,确保传感器误差低于0.2%;开发基于区块链技术的检测数据存证系统,实现测试结果不可篡改性;构建覆盖2000+故障模式的专家知识库,为不同行业提供定制化判定阈值。德国TÜV认证显示,该体系使检测报告的国际互认效率提升60%。
## 发展展望与建议面对工业4.0时代对设备可靠性的严苛要求,建议重点突破三个方向:其一,开发集成太赫兹成像的接触界面三维重构技术,实现纳米级缺陷可视化检测;其二,建立跨行业的电接触噪声数据库,推动ASTM等国际标准更新;其三,探索数字孪生技术在接触件全生命周期管理的应用,构建"物理检测-虚拟仿真"双驱动模式。通过产学研协同创新,预计到2030年可将关键设备接触故障率降低至现有水平的1/5。
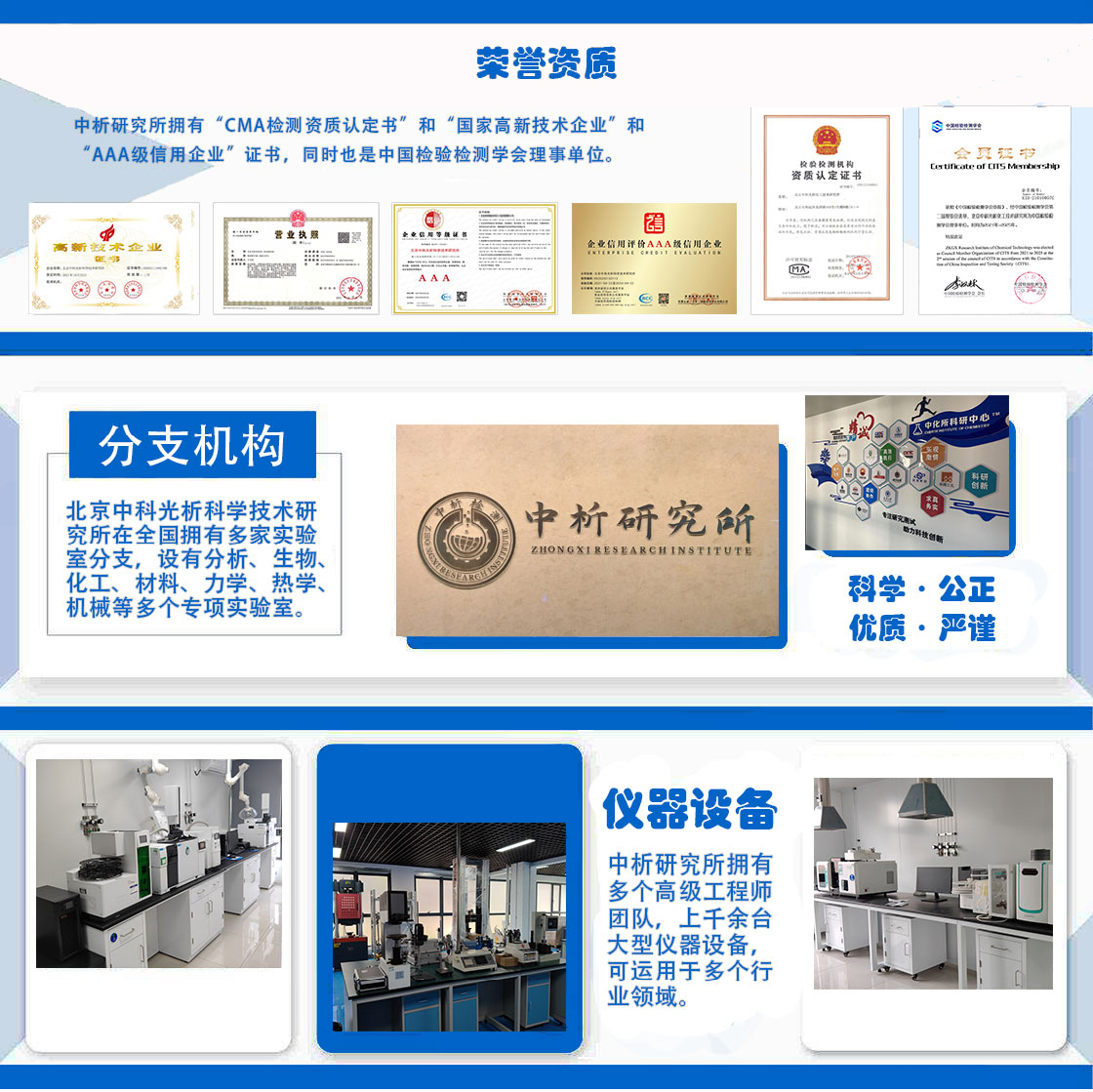
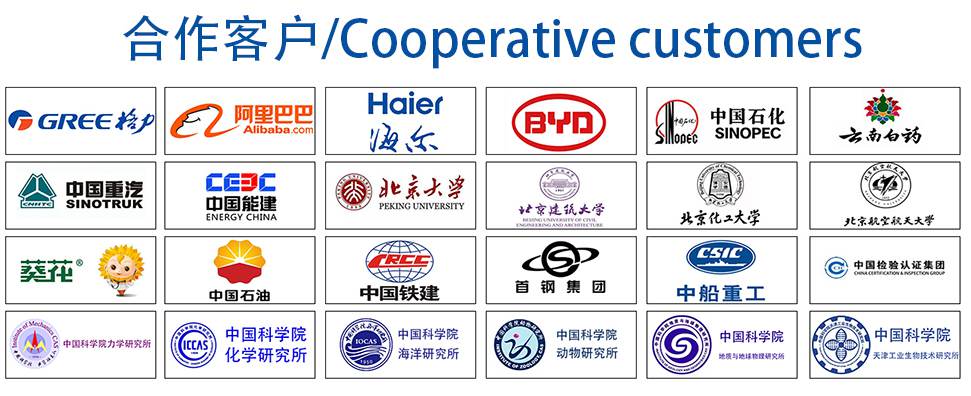