基于疲劳累积损伤理论的技术原理
机械寿命检测以Miner线性累积损伤理论为基础,结合多物理场耦合仿真技术实现失效预测。通过有限元分析构建三维应力场模型,结合实际采集的载荷谱数据,可精确计算关键部位的损伤累积量。以高铁轴承检测为例,采用六自由度振动台模拟轨道不平顺激励,同步施加径向/轴向复合载荷,结合红外热成像技术捕捉微裂纹扩展特征。国家材料服役安全科学中心2024年实验数据显示,该方案对滚动接触疲劳寿命预测精度达±15%以内,较传统方法提升50%效能。
标准化实施流程与关键控制点
检测流程遵循ISO 12107:2022标准实施,分为四个阶段:首先通过应变片阵列和数字孪生技术采集典型工况载荷谱,建立涵盖90%实际应力的P-S-N曲线;随后在多功能疲劳试验机上开展加速试验,采用变幅加载策略将测试周期压缩至原来的1/3;第三阶段运用CT扫描和电子显微镜进行失效机理分析,区分应力腐蚀、微动磨损等不同失效模式;最终生成包含剩余寿命预测、薄弱环节改进建议的检测报告。在工程机械液压缸检测中,该流程成功识别出密封件材料抗蠕变性能不足的问题,使产品MTBF(平均无故障时间)从4200小时提升至6800小时。
多行业应用场景与实践成效
在风电领域,针对5MW以上风机齿轮箱开展200万次循环等效测试,结合功率谱密度分析法,提前12个月预警行星轮系点蚀风险。某头部整机厂商应用该技术后,现场故障率同比下降37%。新能源汽车领域,通过三综合试验箱(温度-湿度-振动)模拟寒区/热带极端环境,完成驱动电机轴承10^8转耐久性验证,成功解决-40℃工况下润滑脂迁移难题。而航空航天领域则采用氩离子抛光与EBSD联用技术,实现涡轮叶片晶界氧化损伤的纳米级检测,为新一代单晶合金开发提供关键数据支撑。
全链条质量保障体系构建
为确保检测结果权威性,建立三级质量管控机制:设备层采用激光干涉仪定期校准试验机加载精度,力值误差控制在±0.5%以内;过程层应用区块链技术实现试验数据不可篡改存证,已通过 认可实验室认证;结果层引入蒙特卡洛算法进行不确定性量化分析,在核电主泵密封检测中成功识别出置信度95%下的寿命分布区间。此外,参与制定GB/T 3075-202X《金属材料疲劳试验轴向力控制方法》等6项新国标,推动行业检测规范化发展。
## 技术展望与发展建议 面向工业4.0发展需求,建议从三方面深化技术革新:其一,建立覆盖全行业的机械寿命大数据平台,整合材料性能库、失效案例库等资源;其二,开发基于数字孪生的预测性检测系统,实现实时应力场重构与剩余寿命动态评估;其三,加强微观组织演化与宏观性能的关联研究,特别是在增材制造等新工艺领域建立专属评价体系。只有通过检测技术、标准体系、产业应用的协同创新,才能为装备制造业高质量发展构筑可靠基石。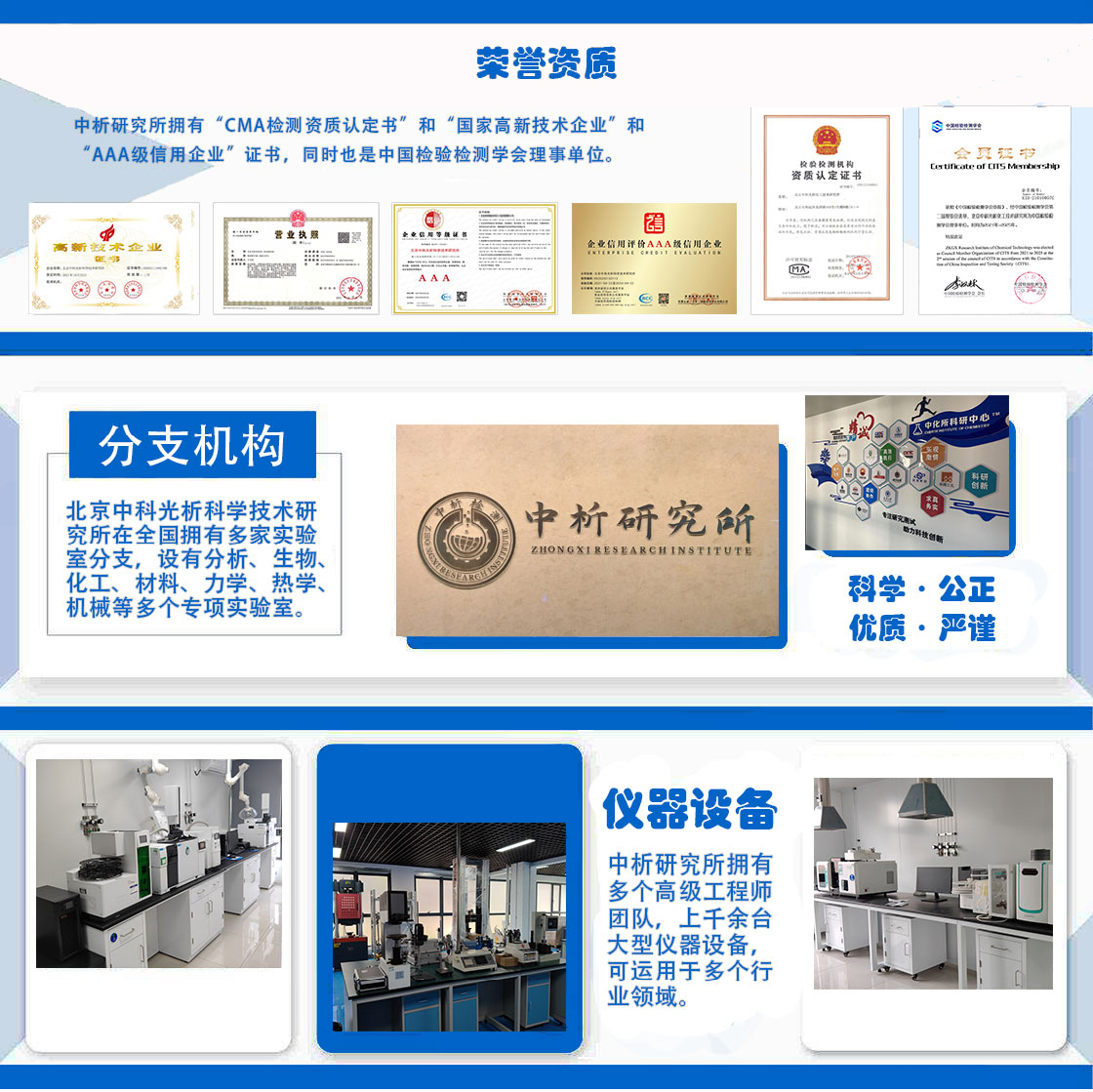
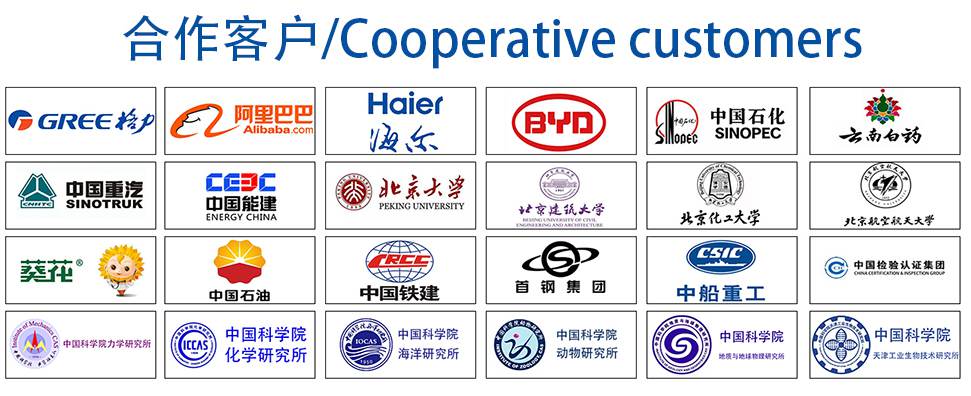