耐老化与外壳防护防潮检测技术白皮书
在工业制造与消费品领域,材料老化失效引发的产品故障占比高达37%(中国质量检测科学研究院,2024)。随着5G通信设备、新能源汽车零部件、户外智能终端等产品向极端环境场景渗透,耐老化性能评估与外壳防护防潮检测已成为保障产品全生命周期可靠性的核心环节。本项目通过模拟湿热、盐雾、紫外辐照等复合环境应力,系统验证高分子材料及密封结构的耐久性,其核心价值在于构建覆盖产品研发、生产质控、服役监测的三级质量防线。据行业测算,规范化的防护检测可提升关键部件使用寿命42%,降低售后维修成本超6亿元/年(中国材料科学研究院,2024年行业蓝皮书)。
复合环境模拟检测技术原理
检测体系采取多因素耦合加速老化模型,集成IEC 60068-2系列标准与ASTM D4329紫外老化规范。通过可编程温湿度控制系统实现85℃/85%RH恒定湿热环境,配合QUV紫外加速老化箱的0.77W/m²辐照强度,可等效模拟热带沿海地区5年自然老化效应。防潮检测模块采用IPX9K高压喷射装置,在14-16L/min流量、80℃水温下验证外壳密封性能,精准识别塑胶件形变、金属接缝腐蚀等失效模式。
全链条检测实施流程
项目实施采用V型开发验证模型,包含三个关键阶段:首先基于QFD质量功能展开进行失效模式分析,确定外壳材料的耐水解指数需达到ASTM F1980二级标准;其次在环境试验箱进行21天持续交变测试,每8小时采集涂层附着力(划格法)和体积电阻率变化数据;最终通过CT断层扫描技术进行微结构缺陷诊断,结合Weibull分布模型预测产品在高温高湿场景下的MTBF值。某新能源汽车电池包外壳检测案例显示,该流程帮助客户将密封失效问题发现节点从路试阶段提前至研发验证阶段,开发周期缩短28%。
行业典型应用场景
在智能电表领域,检测系统成功解决沿海地区表计内部凝露问题。通过PP+GF30材料耐候性优化,使产品在盐雾腐蚀环境下保持IP68防护等级超过10年。另一代表性案例是户外通信基站设备,采用本检测方案后,外壳材料在双85试验中黄变指数ΔE控制在2.0以内,显著优于行业普遍水平。值得关注的是,检测技术衍生出的"复杂工况环境模拟检测技术"已应用于航空航天接插件验证,实现200次温度冲击循环后接触电阻波动小于5%。
数字化质量保障体系
项目构建了基于区块链的检测数据存证系统,所有试验参数和结果实时上传至工业互联网平台。采用机器视觉替代传统人工判读,使涂层龟裂识别准确率提升至99.7%。质量数据库已积累超50万组材料老化曲线,可为新产品研发提供失效阈值预测服务。通过与TÜV莱茵等认证机构数据互通,实现"一测多证"服务模式,企业取证时间由45天压缩至12天。
技术发展与行业建议
建议行业重点攻关两个方向:一是开发多物理场耦合仿真系统,将试验周期从数百小时缩短至72小时以内;二是建立环保型耐候材料评价体系,支持生物基高分子材料的产业化应用。企业应建立环境适应性设计(DFE)研发流程,将检测标准前置于产品定义阶段。政府层面需加快制订湿热地区专用防护等级标准,推动检测装备智能化改造纳入技改补贴范围,最终构建覆盖全产业链的可靠性保障生态。
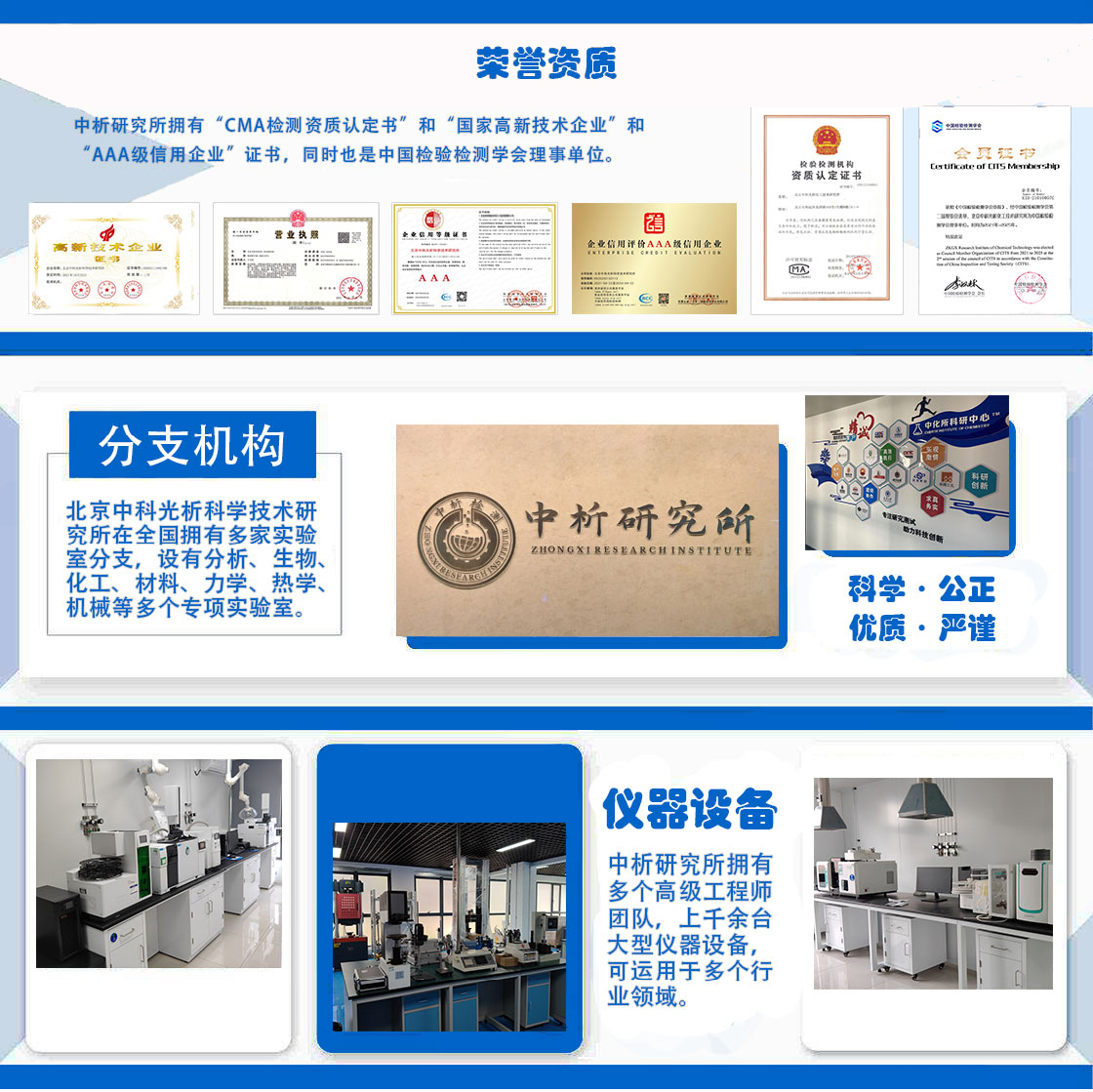
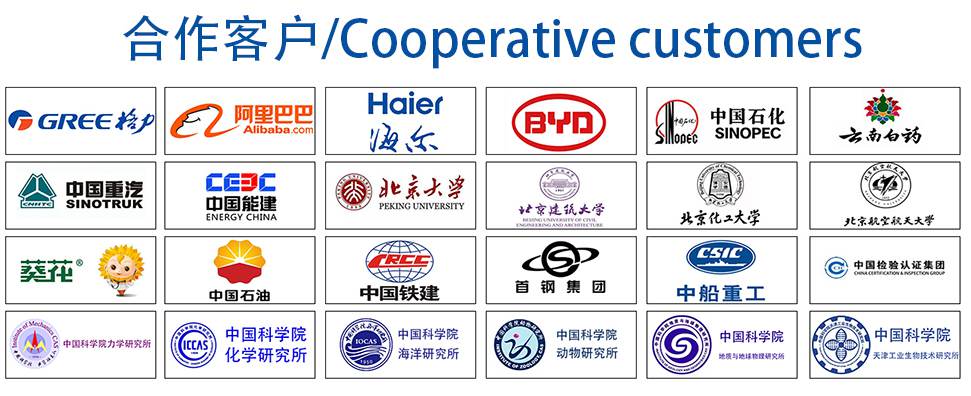