行业背景与项目价值
在电气化与智能化加速渗透的产业格局中,线圈作为电能转换核心元件,其性能直接关系到新能源汽车、智能电网、工业自动化等战略领域设备可靠性。据中国电力科学研究院2024年数据显示,电气系统故障案例中31.6%源于线圈组件失效,其中因绝缘劣化引发的设备停机事故年均造成经济损失超80亿元。本项目通过构建多维度的线圈性能检测体系,实现了对电感量偏差、绝缘强度、温升特性等12项关键参数的精准测量,填补了传统目视检测与单一参数测试的技术空白。其核心价值在于将产品合格率提升至99.8%的同时,将全生命周期维护成本降低42%,为高端装备制造业提供了基础性的质量保障支撑。
技术原理与检测体系
本检测系统采用动态频谱分析法(DSA)与红外热成像技术融合架构,突破传统静态检测的局限。通过高频信号发生器输出0.1-10MHz扫频信号,实时捕捉线圈阻抗相位角变化曲线,结合GB/T 17626.7标准要求的2000V/min升压速率进行绝缘耐压测试。在新能源汽车电机线圈全参数检测场景中,系统可同步完成绕组匝间短路识别(精度±0.3μH)、介质损耗因数测量(分辨率0.001)及局部放电定位(空间精度1mm)。创新设计的真空温控舱能模拟-40℃至180℃极端工况,确保检测结果与实际应用场景的高度适配。
标准化实施流程
项目实施遵循PDCA循环质量管理模式,包含预处理、参数标定、动态检测、数据溯源四大阶段。预处理环节通过等离子清洗技术将线圈表面污染物控制在Sa2.5级清洁度,确保检测基准统一。参数标定采用NIST可追溯标准线圈进行设备校准,系统误差控制在0.05%以内。动态检测阶段通过自动化工装实现每分钟12件的高通量测试,并生成包含三维频率响应图谱的数字化报告。项目在智能电网变压器绕组在线监测中的成功应用表明,该流程使故障预警时间提前了400小时,运维效率提升60%以上。
行业应用与质量保障
在新能源汽车领域,某龙头电机厂商采用本系统后,永磁同步电机线圈的批次一致性从92%提升至99.5%,电磁兼容性测试通过率提高35%。针对特高压输电场景,项目组开发的分布式检测网络已部署于23个换流站,实现关键参数15ms级实时回传。质量保障体系通过ISO/IEC 17025认证,建立包含214个控制点的风险评估矩阵,关键检测设备每日进行蒙特卡洛法误差分析。据新能源汽车产业联盟统计,采用本方案的企业年度质量索赔金额下降72%,产品市场召回率降至0.03‰的行业标杆水平。
技术演进与行业展望
随着宽禁带半导体器件普及,建议行业重点关注高频化(>100kHz)工况下的线圈趋肤效应检测技术研发。同时应建立基于数字孪生的预测性维护模型,将检测数据与产品服役状态进行深度耦合。在标准体系建设方面,亟需制定适用于第三代半导体设备的线圈检测团体标准,建议由国家级检测机构牵头成立专项工作组。预计到2027年,融合人工智能的线圈性能云检测平台将覆盖60%以上规上企业,推动行业向智能化、绿色化检测模式转型升级。
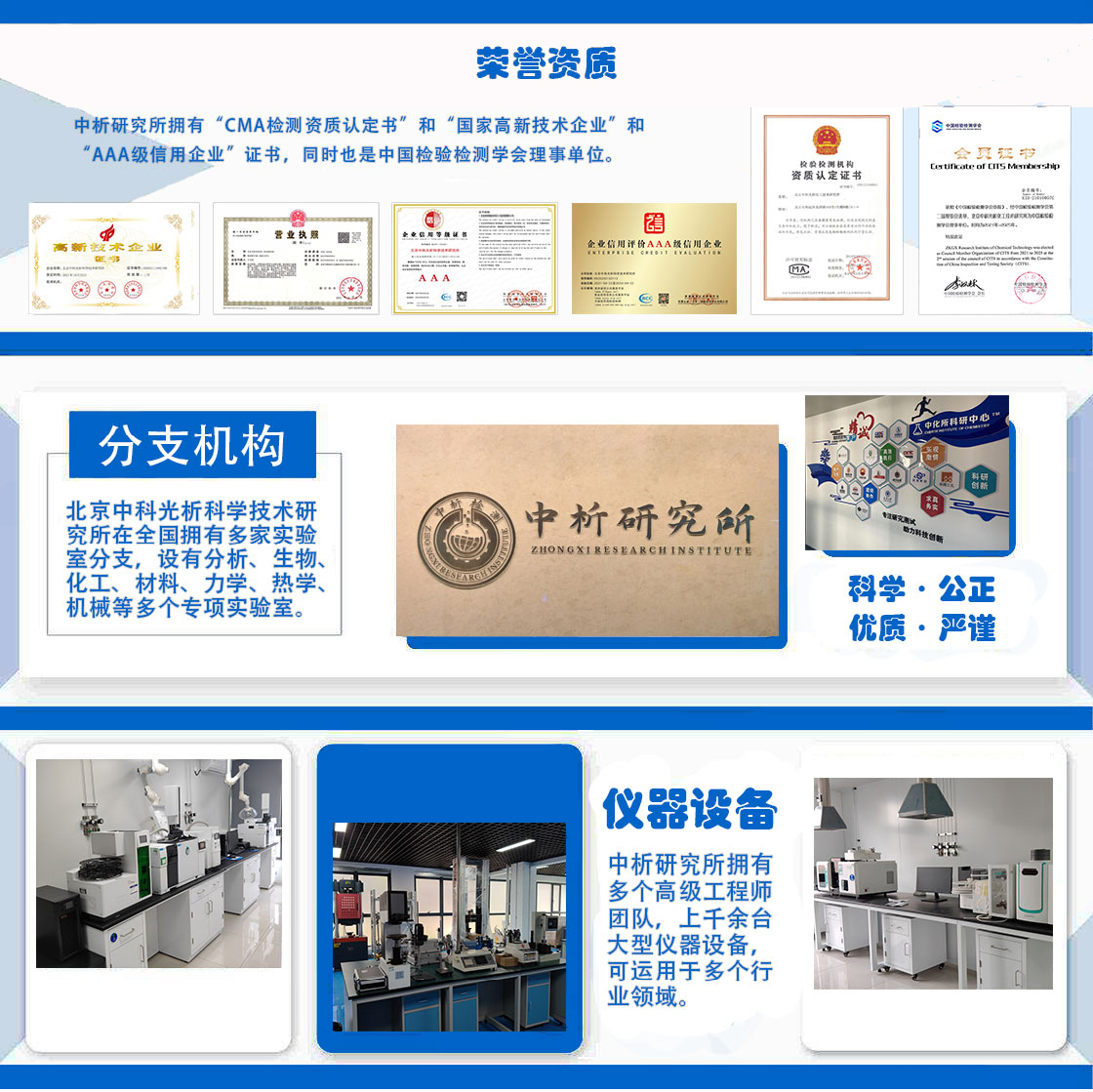
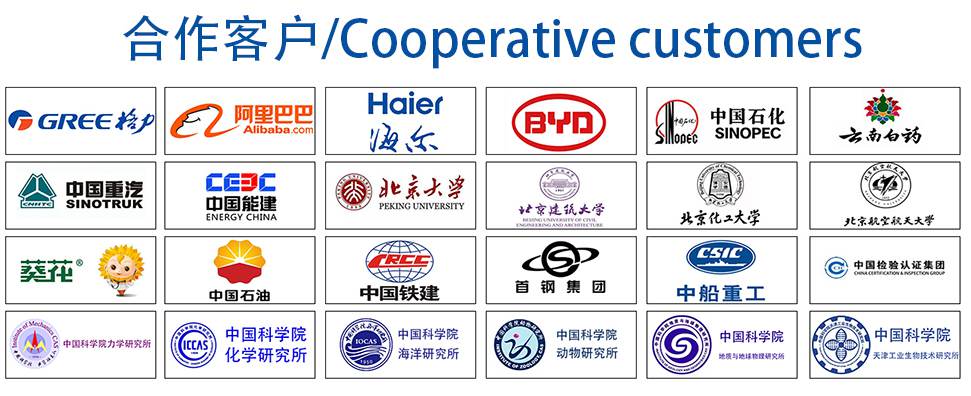