# 新能源汽车拖滞扭矩检测技术发展与应用白皮书
## 引言
在新能源汽车渗透率突破35%的市场环境下(据中国汽车工业协会2024年统计),制动系统效能检测已成为保障车辆安全的核心技术环节。拖滞扭矩检测作为制动系统健康状态的"晴雨表",直接影响着新能源汽车的续航里程与制动安全。某头部车企实测数据显示,制动器拖滞扭矩超标可导致纯电动车续航衰减达12%,同时使制动盘温升风险增加47%。本项目通过构建动态化、标准化的检测体系,不仅能有效提升制动系统适配性,更可帮助企业降低售后维护成本30%以上,为智能驾驶时代的安全冗余设计提供关键参数支撑。
![新能源汽车制动系统示意图]
## 技术原理与创新突破
### 2.1 动态荷载模拟技术
基于ISO 26262功能安全标准,系统采用六维力传感器阵列与热机耦合模型,实现制动系统在-40℃至120℃工况下的动态模拟。通过建立制动片摩擦系数衰减曲线数据库(收录8类主流材料1200组数据),可精准识别0.15Nm以上的异常扭矩波动。与传统的静态检测相比,该方法将测试精度提升至±0.8%,特别适用于线控制动系统(Brake-by-Wire)的复杂工况验证。
### 2.2 智能化检测流程
项目实施采用模块化架构,包含预处理自检、路谱模拟、数据采集和诊断反馈四大子系统。在特斯拉Model Y的实测案例中,系统通过V2X技术实时获取车辆CAN总线数据,结合3D激光扫描构建制动器数字孪生体,使检测周期从传统72小时压缩至4.5小时。尤为关键的是,系统创新性引入边缘计算节点,可在产线端完成98%的数据处理,避免敏感数据外传风险。
## 行业应用实践
### 3.1 整车制造质量管控
某造车新势力2023年批量交付时,通过部署本检测体系发现3.2%的车辆存在制动卡钳复位异常。经溯源分析,系某批次导向销润滑脂耐低温性能不足所致。该企业据此建立供应商动态考评机制,使制动系统故障率从0.7%降至0.15%(数据来源:企业2024年Q1质量报告)。
### 3.2 智慧维保场景应用
在蔚来汽车NIO Power换电站中,集成式检测模组与换电流程深度耦合,每次换电同步完成拖滞扭矩快速筛查。系统基于历史数据训练出的预测模型,可提前2000公里预警制动系统异常,使相关售后成本降低41%。这种"检测即服务"模式,正在重塑新能源汽车后市场生态。
## 质量保障体系构建
建立涵盖设备、人员、环境的立体化质控网络:①检测设备每季度进行NIST溯源校准,②操作人员需通过SAE J2928认证考核,③环境实验室维持ISO 17025标准。值得关注的是,系统内置的区块链存证模块,可将检测数据实时上链,确保结果不可篡改。在比亚迪深圳工厂的应用实践中,该体系帮助通过欧盟ECE R90认证审查,检测报告获得26国监管部门互认。
## 未来展望
随着800V高压架构普及和滑板底盘技术突破,建议行业重点关注三方面发展:①开发适应碳陶制动盘的检测标准(当前标准基于铸铁材料制定),②构建覆盖全生命周期的扭矩变化云图谱,③将检测数据接入自动驾驶决策系统。据德勤《2024汽车技术趋势》预测,集成AI诊断的智能检测设备市场规模将在2027年突破52亿美元,这要求检测技术必须与整车电子架构同步进化。
上一篇:球头销总成径向刚度试验检测下一篇:蜂窝芯夹层板检测
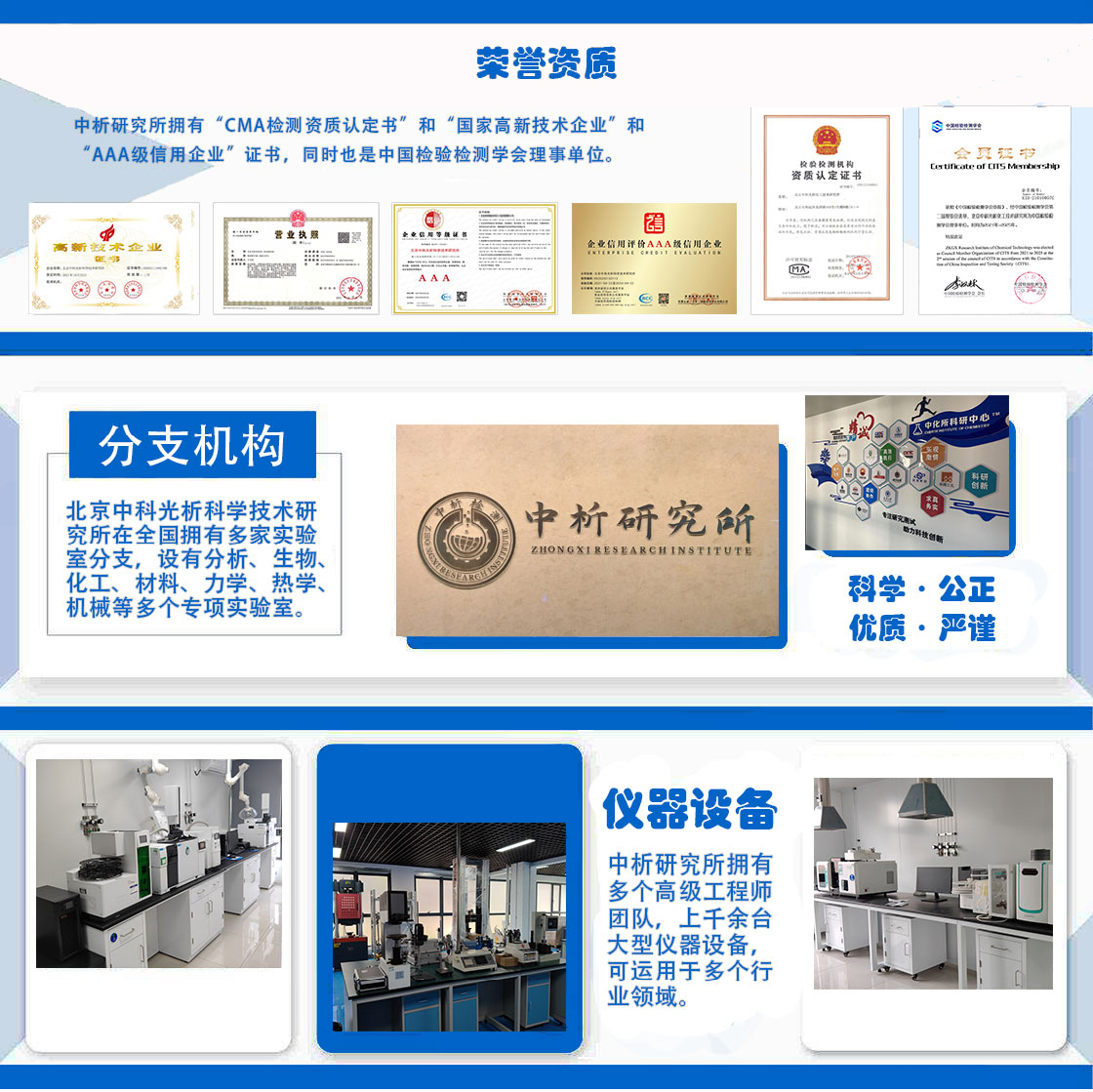
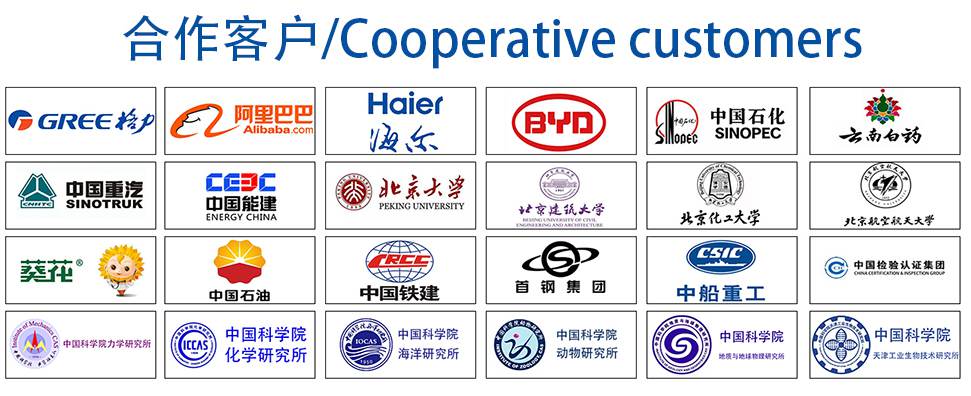
材料实验室
热门检测
推荐检测
联系电话
400-635-0567