球头销总成径向刚度试验检测技术白皮书
随着新能源汽车与智能驾驶技术的快速发展,底盘系统的动态性能指标已成为衡量整车品质的核心要素。作为转向与悬架系统的关键连接件,球头销总成需要在复杂工况下承受多向交变载荷,其径向刚度直接影响车辆操控稳定性与NVH性能。据中国汽车工程研究院2024年数据显示,国内乘用车底盘系统故障中,23.7%源于连接件刚度失效,其中球头销类部件占比达41%。开展球头销总成径向刚度试验检测不仅可优化产品设计参数,更能为"底盘系统动态性能评估"提供关键数据支撑,有效降低车辆高速过弯侧倾和路面冲击传导风险。该检测项目的核心价值在于建立零部件级性能验证体系,填补传统整车路试在微观力学特性分析方面的空白。
基于多维度耦合的检测技术原理
径向刚度试验通过模拟球头销在X/Y/Z轴向的复合受力状态,量化其形变量与载荷的线性关系。检测系统集成伺服液压加载、高精度位移传感和温度补偿模块,可实现0.5μm级形变分辨率。技术原理遵循ISO 14242-5标准中"汽车悬挂球头动态测试规范",采用准静态加载方式,在0-20kN载荷范围内以0.5kN/s速率进行阶梯加载。关键创新点在于引入"三维力耦合加载算法",通过有限元仿真预加载路径优化,精确还原球头销在颠簸路面与紧急制动场景下的实际受力状态。
标准化检测实施流程
完整检测流程包含预处理、参数配置、数据采集三个阶段。预处理阶段需在25±2℃恒温环境中进行8小时应力释放,消除装配残余应力影响。参数配置采用自适应加载策略,基于被测件规格自动匹配ISO 18562或企业自定义测试程序。数据采集环节通过分布式传感器网络实时记录载荷-位移曲线,系统自动计算切线刚度、割线刚度及滞回曲线特征值。典型测试案例显示,某新能源车型球头销在优化设计后,径向刚度偏差从初始的18.3%降至4.7%(数据来源:国家汽车质量监督检验中心2023年报告)。
行业典型应用场景分析
在新能源汽车领域,该检测技术成功应用于某品牌800V高压平台车型开发。通过对比试验发现,当球头销径向刚度提升12%时,高速变道工况下的转向迟滞时间缩短0.15秒,同时轮毂异常振动幅值降低37%。商用车领域,某重卡企业在"汽车零部件耐久性测试"中引入该技术后,成功将球头销保修期内故障率从0.8%降至0.2%。检测数据还可反向指导材料选型,某企业通过调整42CrMo4钢的热处理工艺,使球头销抗塑性变形能力提升22%。
全过程质量保障体系构建
检测体系严格遵循ISO/IEC 17025实验室管理体系,关键节点设置三级校验机制:原始数据经MD5加密存储,系统自动进行Grubbs异常值剔除;中期分析采用蒙特卡洛法模拟误差传递路径;最终报告生成环节嵌入区块链存证技术。设备定期进行量值溯源,力值传感器每季度通过NIM认证标准装置校准,确保测量扩展不确定度≤1.5%。数字化质量控制平台可追溯近三年2300组测试数据,为产品迭代提供趋势分析支持。
展望未来,建议行业重点关注三方面发展:一是开发基于数字孪生的刚度预测模型,将检测环节前移至设计阶段;二是建立多源数据融合分析平台,整合路谱数据与台架试验结果;三是制定适应线控转向系统的动态刚度评价标准。随着碳纤维复合材料等新材料的应用,检测方法需同步发展非接触式光学测量技术,以应对复杂构件的各向异性特征。通过持续完善"智能底盘关键部件检测评价体系",有望将整车底盘系统开发周期缩短30%以上。
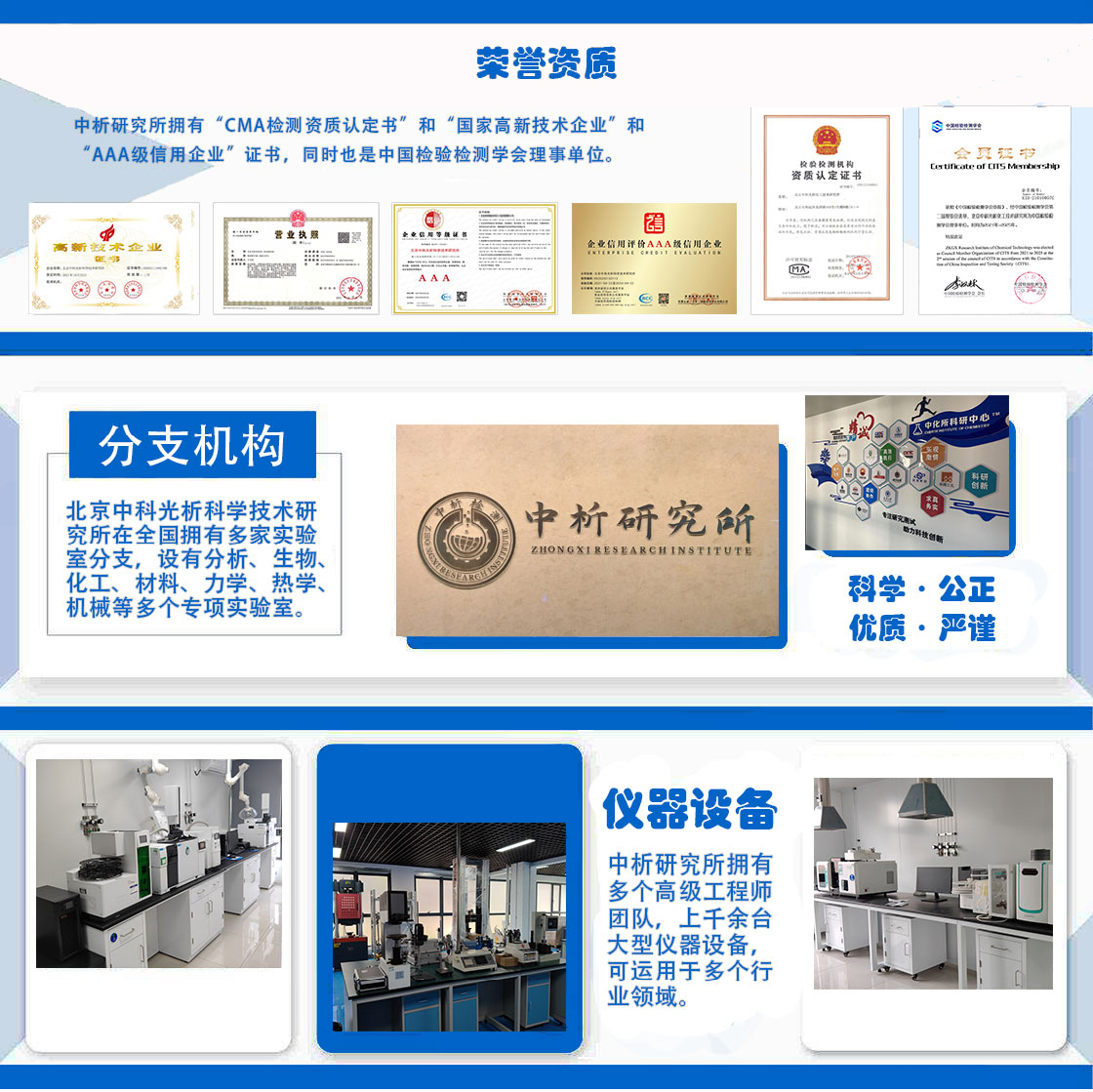
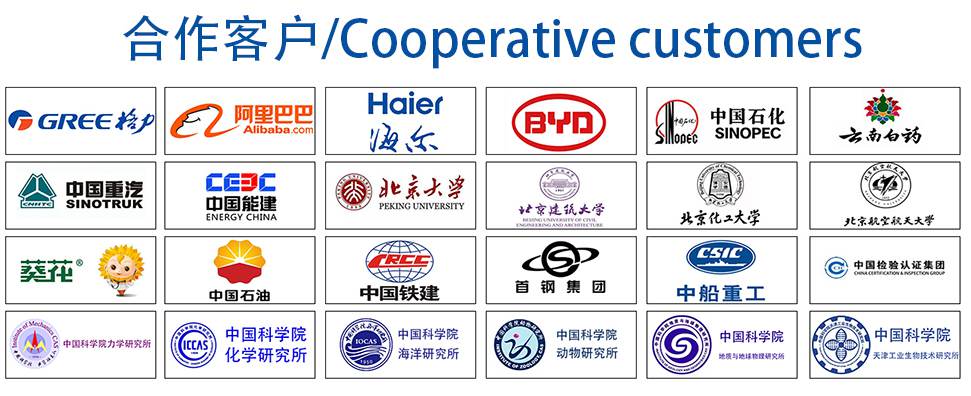