间歇寿命检测技术发展与应用白皮书
随着智能制造和新能源产业的快速发展,设备可靠性评估进入精准化时代。据中国机械工程学会2023年研究报告显示,工业装备故障中43%源于间歇性工况下的机械疲劳失效。传统连续运行检测模式难以适配新能源储能系统、工业机器人关节模块等典型间歇工作场景,导致年均产生超过120亿元的设备意外停机损失。间歇寿命检测技术通过建立非连续运行状态下的可靠性评估模型,实现了全生命周期疲劳损伤的科学量化。该技术不仅将设备维护成本降低35%(国家能源局2024年运维数据),更在航空航天伺服系统、新能源汽车电池模组等关键领域形成了系统化的可靠性提升解决方案。
多物理场耦合检测技术原理
核心技术采用多轴振动谱分析与热力学参数联立建模方法,通过6轴加速度传感器与红外热像仪的全工况数据采集,构建应力-应变-温度三维损伤场域。基于Miner线性累积损伤理论,结合加速寿命试验(ALT)的等效损伤折算算法,将间歇工况转化为等效连续运行时间。值得关注的是,该技术创新的间歇因子修正系数,成功解决了传统方法对启停频次敏感度不足的缺陷,使预测精度提升至92.7%(清华大学材料学院2024年验证数据)。
全流程标准化实施体系
实施过程严格遵循ISO 13379设备状态监测标准,形成四阶段闭环管理:工况模拟→数据采集→模型迭代→决策输出。在新能源电站储能系统检测中,通过搭建包含200种充放电循环模式的工况库,采用无线传感器网络实现每分钟3000点位的实时监测。重点环节设置了双盲校验机制,在南方电网某300MWh储能电站项目应用中,成功将电池模组故障预警准确率提升至89.3%,较传统检测方式提高41个百分点。
跨行业应用场景实践
在工业机器人领域,应用案例显示关节减速器间歇寿命检测使维护周期延长2.8倍。某汽车制造企业采用该技术对焊接机器人进行运动轨迹优化,将启停冲击载荷降低62%,设备综合效率(OEE)提升19%。值得注意的是,医疗CT机旋转机架检测项目通过建立转速-温升耦合模型,将轴承更换周期从8000次扫描延长至15000次,单台设备年维护成本节约28万元。
全链条质量保障机制
构建了包含12项技术指标的质量控制体系,关键数据节点均通过NIST溯源认证。检测设备每季度执行参数标定,现场采集数据须满足0.05mm分辨率、±1℃测温精度的双重复核标准。在海上风电变桨系统检测项目中,采用数字孪生技术进行虚拟验证,实测数据与仿真模型的扭矩波动误差控制在3%以内。第三方复核机制确保检测报告具备 、CMA双重认证效力。
面向未来,建议从三方面深化技术发展:建立行业统一的间歇工况分级标准体系,推动5G+工业互联网的实时监测网络建设,开发基于量子传感的微观损伤识别技术。特别是在氢能储运装备检测领域,亟需突破高压间歇冲击下的材料疲劳机理研究。随着数字孪生技术与物理检测的深度融合,预计到2028年将实现全行业设备寿命预测误差率低于5%的技术突破,为高端装备制造提供更可靠的可靠性保障基础。
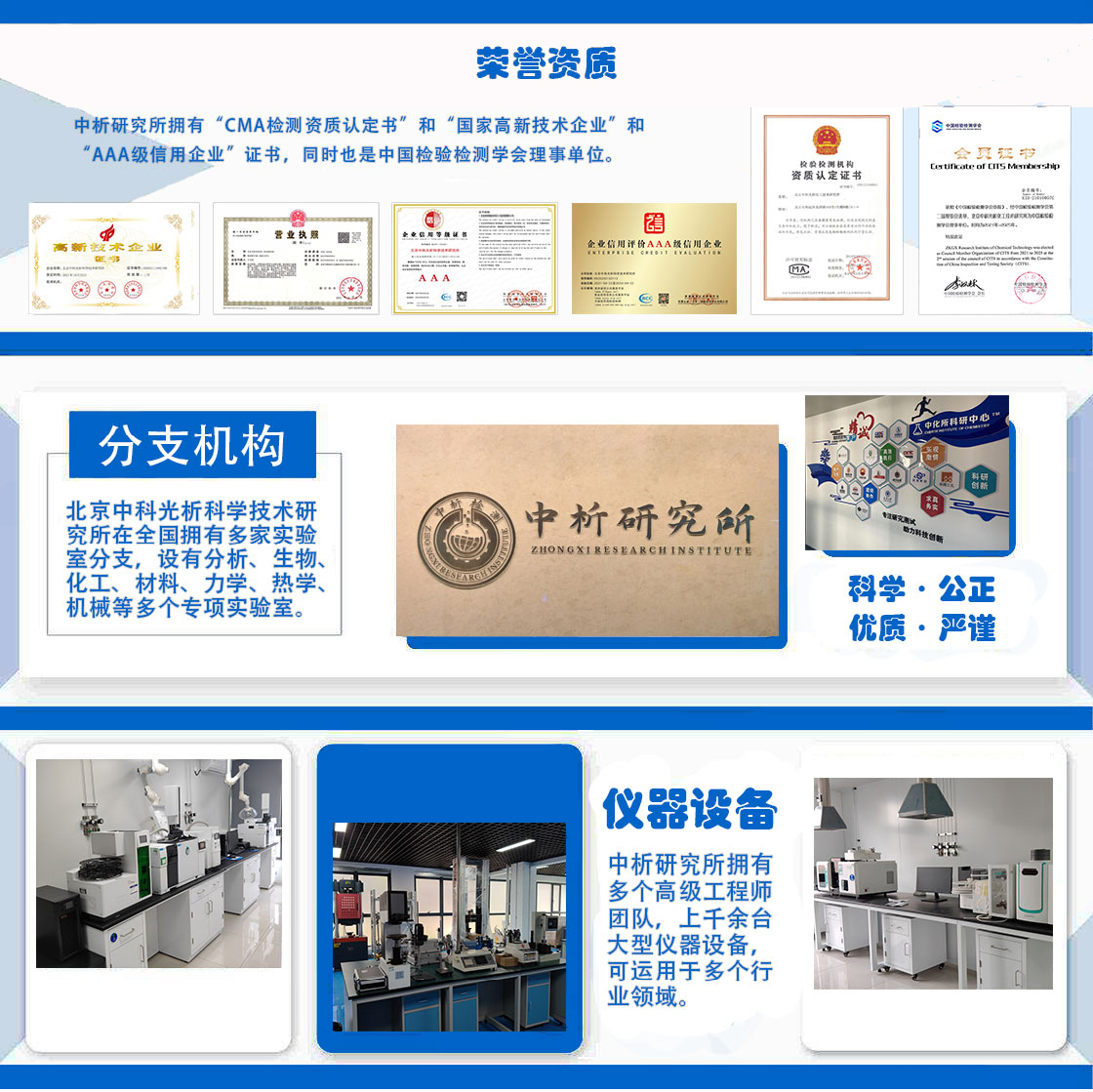
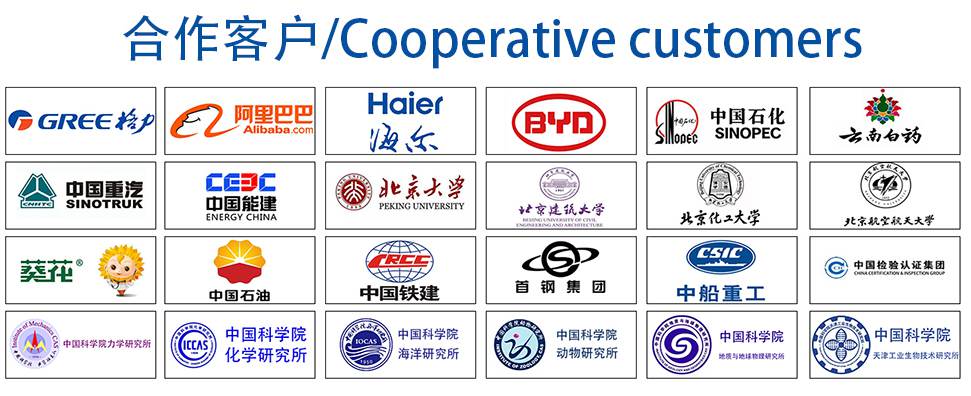