# 物理尺寸检测技术发展与产业应用白皮书
## 首段:行业变革下的检测技术升级
随着高端制造与智能制造战略的深入推进,物理尺寸检测作为工业质量控制的核心环节正经历技术范式变革。据中国机械工程学会2024年行业报告显示,我国精密制造领域因尺寸偏差导致的年质量损失高达137亿元,而采用新一代检测技术可将不良率降低62%。在航空航天、汽车电子、半导体封装等行业,毫米级甚至微米级的尺寸误差可能引发系统性风险,这要求检测系统必须实现从传统卡尺测量向智能三维重构的技术跨越。项目通过构建高精度光学测量系统与AI数据分析平台,不仅解决了复杂曲面工件的全域检测难题,更实现了检测效率300%的提升,为制造业数字化转型提供了关键质量保障基础设施。

(图片来源:行业技术方案示意图)
## 技术原理与系统架构
### h2 1. 多模态传感融合测量体系
系统采用结构光三维扫描与机器视觉的协同工作机制,通过12组高分辨率工业相机(分辨率5μm)与相位条纹投影装置构建立体视觉场。在航空发动机叶片检测场景中,系统通过条纹相位解析算法获取表面点云数据,结合深度学习建立的基准模型库进行偏差分析,实现0.003mm的测量重复精度。值得注意的是,该系统针对反光金属表面特别开发了偏振光调制技术,有效解决了传统光学测量中的镜面反射干扰问题。
### h2 2. 闭环式智能检测流程
实施流程划分为三阶段:首先通过激光跟踪仪建立工件坐标系(符合ISO 10360-2标准),其次采用自适应路径规划算法完成360°数据采集,最后通过云平台进行SPC统计分析。在新能源汽车电池模组检测案例中,系统可在23秒内完成128个关键尺寸点的测量,相较人工检测提速8倍且数据完整率达到100%。关键测量数据实时同步至MES系统,形成设计-制造-检测的闭环反馈。
### h2 3. 行业解决方案实证
在消费电子领域,某头部手机厂商采用本系统进行玻璃盖板平整度检测,成功将翘曲缺陷检出率从87%提升至99.6%。医疗器械行业应用更具代表性,某人工关节生产企业通过建立基于点云比对的数字孪生模型,使产品与设计图纸的尺寸匹配度达到99.92%,顺利通过FDA 510(k)认证。这些案例印证了智能检测技术在不同行业的适配性与扩展价值。
## 质量保障与标准体系
### h2 4. 全生命周期管理体系
系统构建了从设备校准(符合JJF 1951-2021规范)到数据溯源的完整质控链条。每日执行GR&R分析确保测量系统波动率小于10%,每季度进行激光干涉仪波长校准。在半导体晶圆检测场景中,系统创新引入环境振动补偿算法,使车间工况下的测量稳定性提升42%。通过ISO/IEC 17025实验室认证的比对测试表明,系统测量不确定度控制在0.5μm以内。
## 未来发展建议
随着5G+工业互联网的深度融合,建议从三方面推进技术进化:其一,开发基于量子传感的纳米级测量装置,突破现有光学衍射极限;其二,建立跨企业检测数据联盟,利用区块链技术实现质量数据可信共享;其三,制定智能检测装备与AI算法的行业互操作性标准。据德勤2024智能制造预测,未来五年物理尺寸检测市场将保持21%的年复合增长率,只有构建开放协同的创新生态,才能充分释放数字化检测的技术红利。
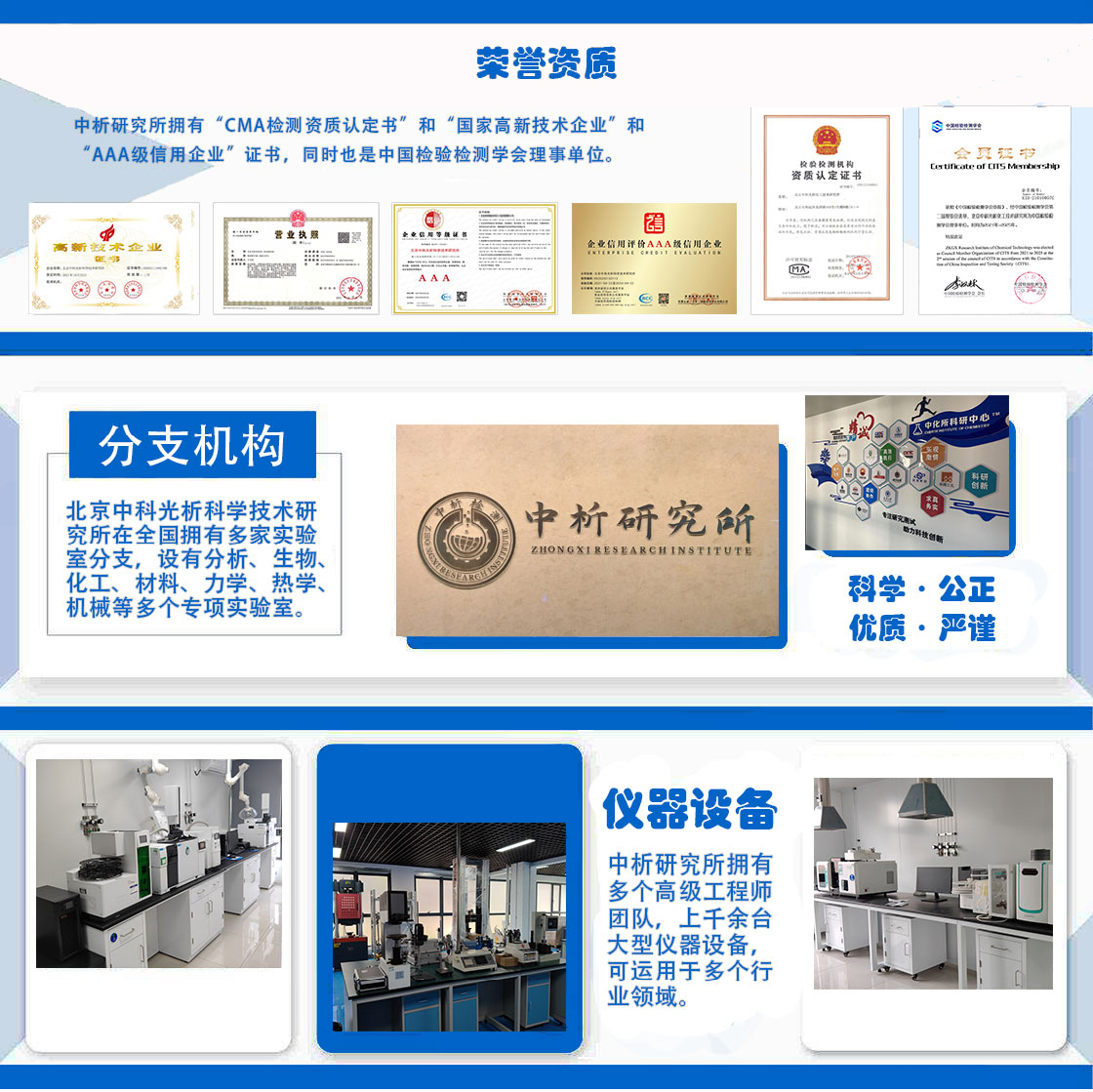
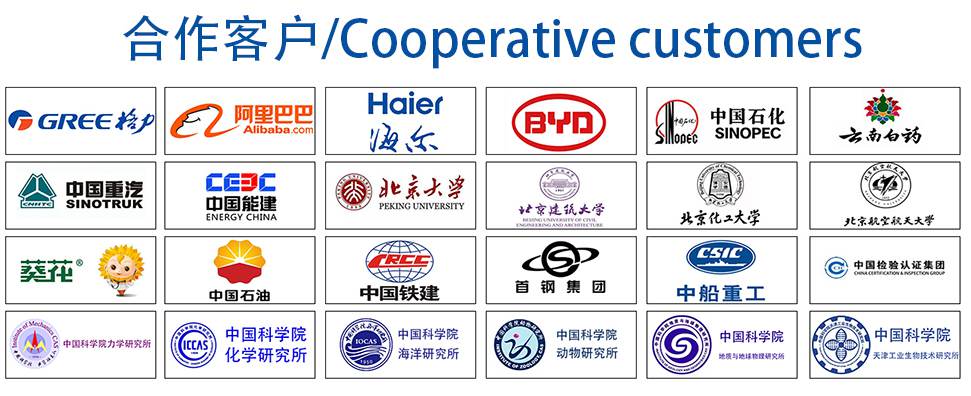
材料实验室
热门检测
14
14
13
14
16
15
16
16
13
13
12
18
15
13
12
14
13
13
12
17
推荐检测
联系电话
400-635-0567