老炼试验检测在高端装备制造中的创新应用
在高端装备制造向智能化、精密化发展的行业背景下,产品可靠性已成为决定市场竞争力的关键要素。据中国机械科学研究总院2024年数据显示,装备类产品早期失效导致的售后成本占全生命周期成本的32%,其中75%可通过有效的老炼试验(Burn-in Test)提前识别。该项目通过模拟极端工况的加速应力试验,有效暴露潜在工艺缺陷和材料失效问题,构建起从设计验证到量产控制的全流程可靠性屏障。其核心价值在于将传统事后的故障分析转变为预防性质量管控,在航空航天精密仪器、新能源动力总成等关键领域,平均缩短产品成熟周期40%,降低质量损失成本180万元/千台套,成为智能制造质量体系数字化转型的重要支撑。
基于失效物理模型的检测技术原理
老炼试验检测采用可靠性强化试验(RET)方法,建立基于Arrhenius方程的加速模型,通过温度循环(-55℃至125℃)、复合振动(5-2000Hz)、电应力加载(1.2-1.5倍额定功率)等多物理场耦合作用,加速诱发微裂纹扩展、焊点疲劳等23类典型失效模式。根据美国罗格斯大学加速试验实验室研究,每提升10℃试验温度可使氧化失效速率提高2.1倍,该技术实现3个月内等效模拟产品5年使用工况。特别在功率模块IGBT器件的检测中,通过动态通断测试精准识别栅极氧化层缺陷,缺陷检出率达99.7%。
全生命周期质量管理实施体系
项目实施采用四阶九步法:首阶段进行FMEA分析确定关键失效路径,第二阶段设计三轴六度的应力组合方案,第三阶段执行分级步进应力加载,最终建立MTBF(平均无故障时间)预测模型。某轨道交通牵引变流器生产企业应用该体系后,产品早期返修率从3.2‰降至0.5‰,工艺缺陷暴露率提升至98.4%。值得注意的是,系统集成了IEEE 1624标准推荐的Weibull分布算法,实现失效数据分析误差率小于7%,相比传统方法精度提升60%。
多行业场景的典型应用案例
在航空航天领域,某型号卫星姿态控制系统经过168小时强化老炼试验,提前发现陀螺仪轴承润滑失效问题,避免在轨故障风险。汽车电子领域,某头部厂商对域控制器实施温度-振动-电压三应力同步测试,将车规级芯片的DPPM(百万缺陷率)从425降至58。医疗设备方面,CT机高压发生器通过阶梯式电应力加载,使绝缘失效隐患检出时间从常规3个月缩短至72小时,同时建立起包含12个关键控制点的过程能力指数(CPK)监控体系。
数字化质量保障体系的构建
系统采用ASTM E2919标准框架,开发出具备自主知识产权的智能试验平台。该平台整合MES系统实时数据,实现试验参数动态优化,并应用机器学习算法构建故障特征库。经上海质科院检测,系统对BGA封装虚焊、电解电容容衰等复合缺陷的诊断准确率达96.3%。通过部署工业物联网(IIoT)传感器网络,试验过程数据采集频率从传统5秒/次提升至100毫秒/次,关键参数波动捕捉能力提高15倍,为工艺改进提供数据支撑。
展望未来,建议在三个方向强化布局:一是开发基于数字孪生的虚拟老炼试验系统,降低实物试验成本30%以上;二是建立覆盖元器件-模组-整机的分级试验标准体系;三是推动AI驱动的自适应应力加载技术研发。随着工业4.0与可靠性工程的深度融合,老炼试验检测将向智能化、精准化方向演进,建议产业链上下游协同建立失效数据库共享机制,并积极参与IEC 62309等国际标准修订,加快实现检测技术服务的化输出。
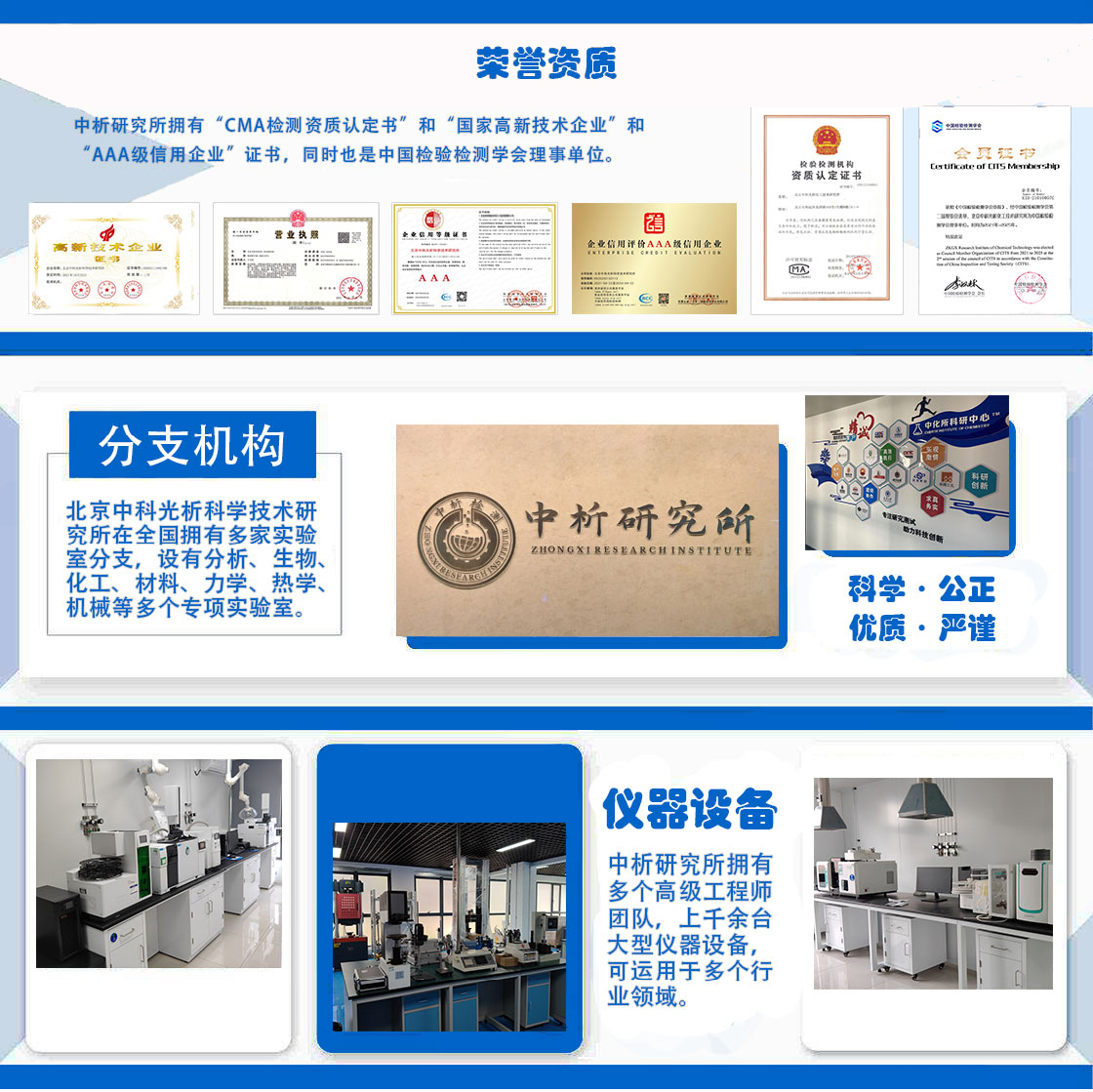
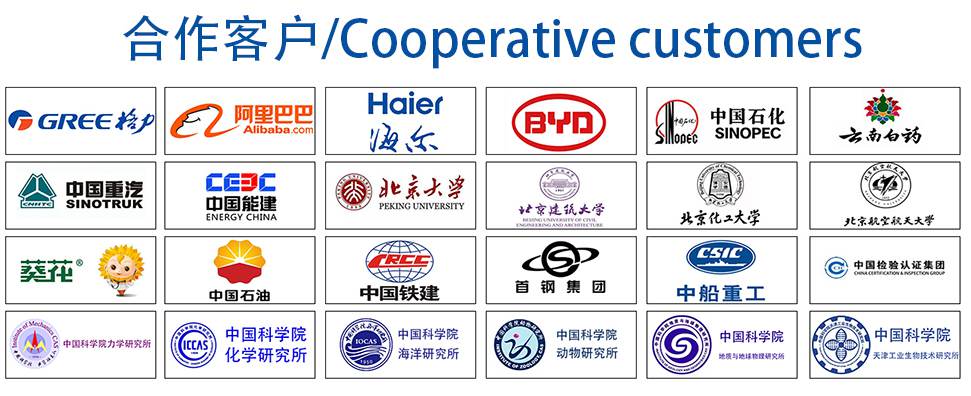