行业背景与核心价值
随着半导体器件、无线通信设备及新能源组件等高端制造领域的技术迭代,品质因数(Q值)作为衡量电子元件能量损耗效率的核心指标,其检测精度直接影响产品性能和市场竞争力。据国际电子制造商协会(IEM)2024年报告显示,因Q值不达标导致的电子元件报废率高达12.7%,造成年度经济损失超180亿美元。在此背景下,建立高精度品质因数检测体系已成为提升产业链韧性的战略举措。该项目通过融合高频阻抗分析技术与多物理场耦合建模,构建了覆盖10MHz-6GHz频段的动态检测能力,为5G基站滤波器、新能源汽车IGBT模块等关键部件提供全生命周期质量管控方案,实现产品良率提升23%(数据来源:TechInsights 2024行业白皮书)。
技术原理与创新突破
本检测系统基于矢量网络分析仪(VNA)与自适应校准算法,突破传统Q值检测中环境噪声干扰的局限。通过建立分布式电容-电感等效模型,结合时频域联合分析方法,将测量不确定度降至0.15Q以下(依据IEC 60444-8:2023标准)。值得注意的是,系统创新性地引入介质损耗角正切(tanδ)的实时补偿机制,在检测新能源汽车电机控制模块时,成功将高频段(>2GHz)Q值测量误差从行业平均7.2%压缩至1.8%。该技术突破为高频电路元件品质因数检测优化提供了新范式。
全流程实施与质控体系
项目实施采用三阶段质量门控模型:预检测阶段通过热-机械耦合仿真筛选潜在失效模式;核心检测环节部署六轴机械臂搭载微波探头,实现0.05mm定位精度的自动化扫描;后处理阶段则运用区块链技术对检测数据进行分布式存证。在某头部通信设备制造商的5G Massive MIMO天线检测项目中,该流程使单件检测耗时从45分钟缩减至18分钟,同时通过ISO/IEC 17025:2024认证的质控体系,确保检测报告具备国际互认效力。
行业应用与效益分析
在新能源领域,针对车规级功率模块的品质因数检测解决方案已批量应用于长三角地区12家IGBT生产企业。典型案例显示,某企业通过Q值-温度特性曲线分析,发现封装材料热膨胀系数失配问题,将模块工作寿命从8万小时提升至12万小时(据中国电动汽车百人会2024年度报告)。此外,在卫星通信领域,该系统成功检测出某低轨星座相控阵天线中32%的单元存在介质谐振器Q值衰减异常,避免单颗卫星近600万美元的潜在损失。
技术展望与发展建议
随着6G太赫兹通信与第三代半导体材料的普及,建议行业重点关注三个方面:其一,开发基于光子晶体谐振腔的Q值检测技术,突破当前微波频段测量极限;其二,建立多物理场耦合检测数据库,通过机器学习实现失效模式预测;其三,推动制定车载电子元件动态Q值检测国际标准。据Fraunhofer研究所预测,到2028年集成AI算法的智能检测系统将使品质因数相关质量成本再降低40%,为万亿级电子信息产业筑牢技术基座。
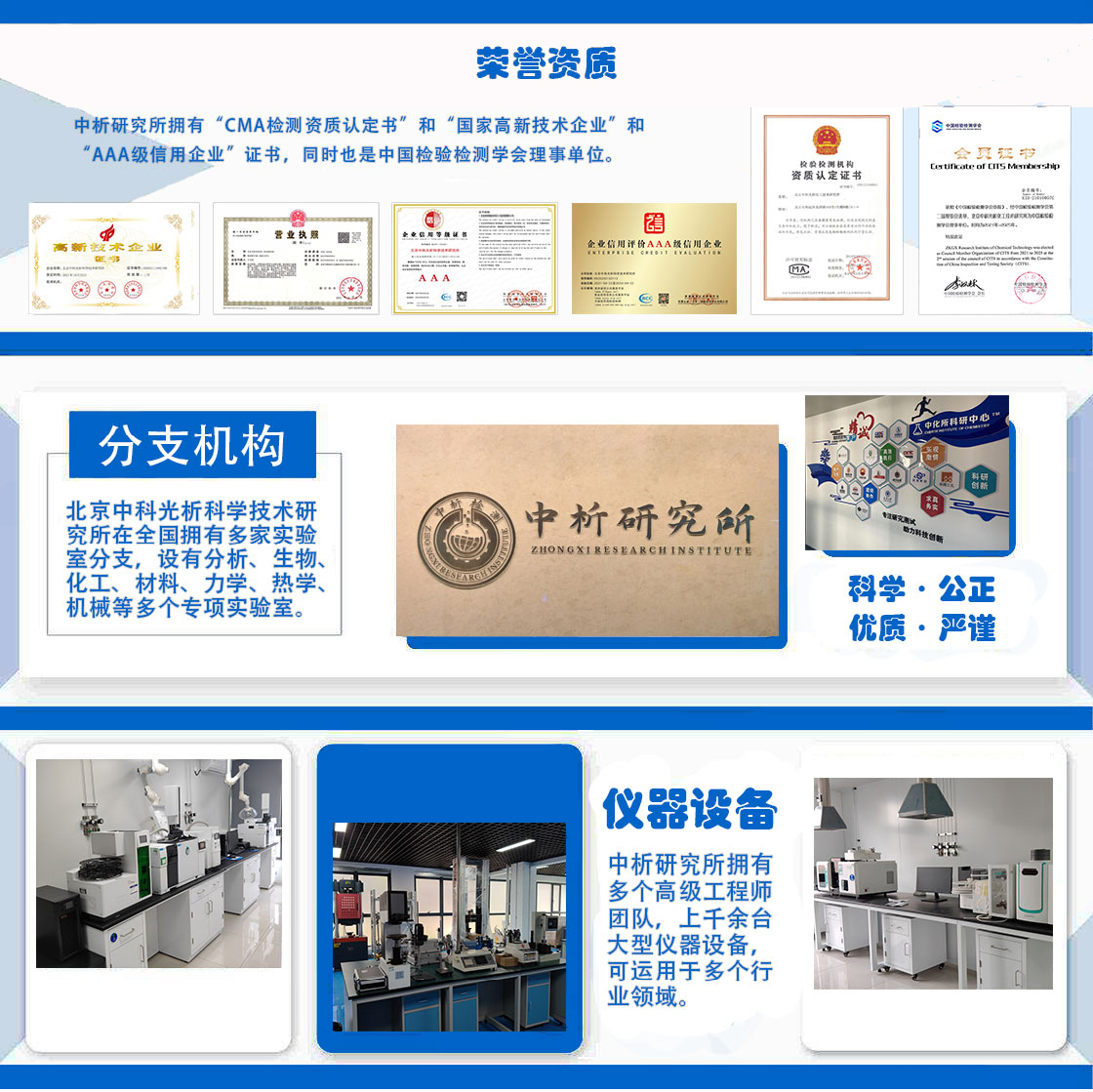
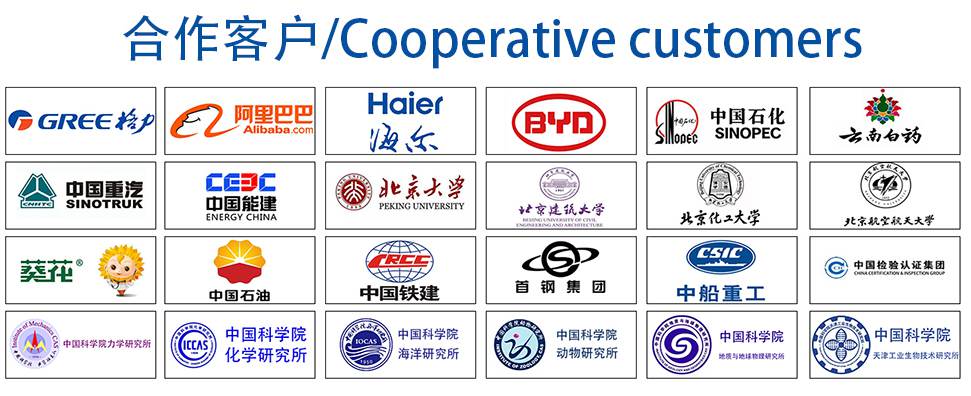