内部检查检测技术白皮书
随着高端装备制造和基础设施建设的升级,设备内部结构复杂度呈现指数级增长。据国家质量基础设施研究中心2024年报告显示,我国每年因设备内部缺陷导致的工业事故损失超过1200亿元,其中62%的故障源于隐蔽部位损伤未被及时发现。在此背景下,内部检查检测技术作为预防性维护的核心手段,已成为保障关键设备安全运行的重要防线。该项目通过创新性应用多模态传感与智能诊断技术,构建了从微观缺陷识别到宏观结构评估的完整技术体系,在降低运维成本、延长设备寿命周期方面展现出显著价值,特别是在精密仪器内部状态监测和特种设备安全评估领域,其核心检测精度达到0.01mm级,远超行业平均水平。
多源信息融合检测技术
本体系整合工业内窥镜、超声相控阵和太赫兹成像三大技术模块,通过特征级数据融合实现三维空间缺陷重构。其中相控阵探头以32通道环形阵列实现360°声束偏转,配合0.5MHz-15MHz宽频带设计,可穿透80mm厚复合材质。中国机械工程学会2024年实验数据显示,该方案对焊缝内部气孔的检出率较传统方法提升47%,误报率降低至2.3%。在航空发动机叶片内部空腔检测场景中,系统可自动识别0.2mm级的冷却通道堵塞,定位精度达±0.15mm。
模块化标准作业流程
项目实施采用四级质量控制体系,涵盖预处理、数据采集、智能分析和报告生成四大阶段。预处理环节引入环境参数补偿算法,消除温度波动对超声信号的影响;数据采集阶段通过运动轨迹规划确保探头与检测面的最佳耦合距离。在核电压力容器年度检查案例中,检测团队运用该流程使单次作业时间缩短40%,缺陷图谱数据库匹配准确率提升至98.7%。值得注意的是,系统内置的ASME标准缺陷库可自动匹配17类典型缺陷模式,大幅提升诊断效率。
行业应用实证分析
在石油化工领域,项目已累计完成3200公里高危管道的内部腐蚀检测。某炼化企业应用案例显示,系统在高温高压环境下仍能保持0.8mm/年的腐蚀速率监测灵敏度,提前6个月预警了催化裂化装置回弯处的局部减薄风险。轨道交通方面,该技术成功应用于350km/h动车组齿轮箱内部损伤检测,通过声-光联合成像技术发现传统手段难以察觉的微观疲劳裂纹,使关键部件更换周期延长30%以上。
全生命周期质量管控
项目建立的三维质量追溯系统,实现了检测数据的全要素管理。每个检测点关联设备编号、检测时间、环境参数等28项元数据,并通过区块链技术确保数据不可篡改。经 认可实验室验证,系统输出的检测报告符合ISO 9712三级认证要求,在欧盟承压设备指令(PED)合规性审查中获得权威认可。此外,智能诊断模型每季度更新1次训练数据集,持续纳入新型缺陷特征,确保算法适应工业装备迭代需求。
展望未来,建议从三方面深化技术发展:一是构建基于数字孪生的预测性维护平台,实现设备内部状态实时仿真;二是开发适用于微纳尺度检测的量子传感技术,突破当前物理探测极限;三是建立跨行业的检测数据共享机制,通过机器学习优化缺陷识别模型。随着工业互联网与检测技术的深度融合,内部检查检测将向智能化、网络化方向持续演进,为设备全生命周期管理提供更强大的技术支撑。
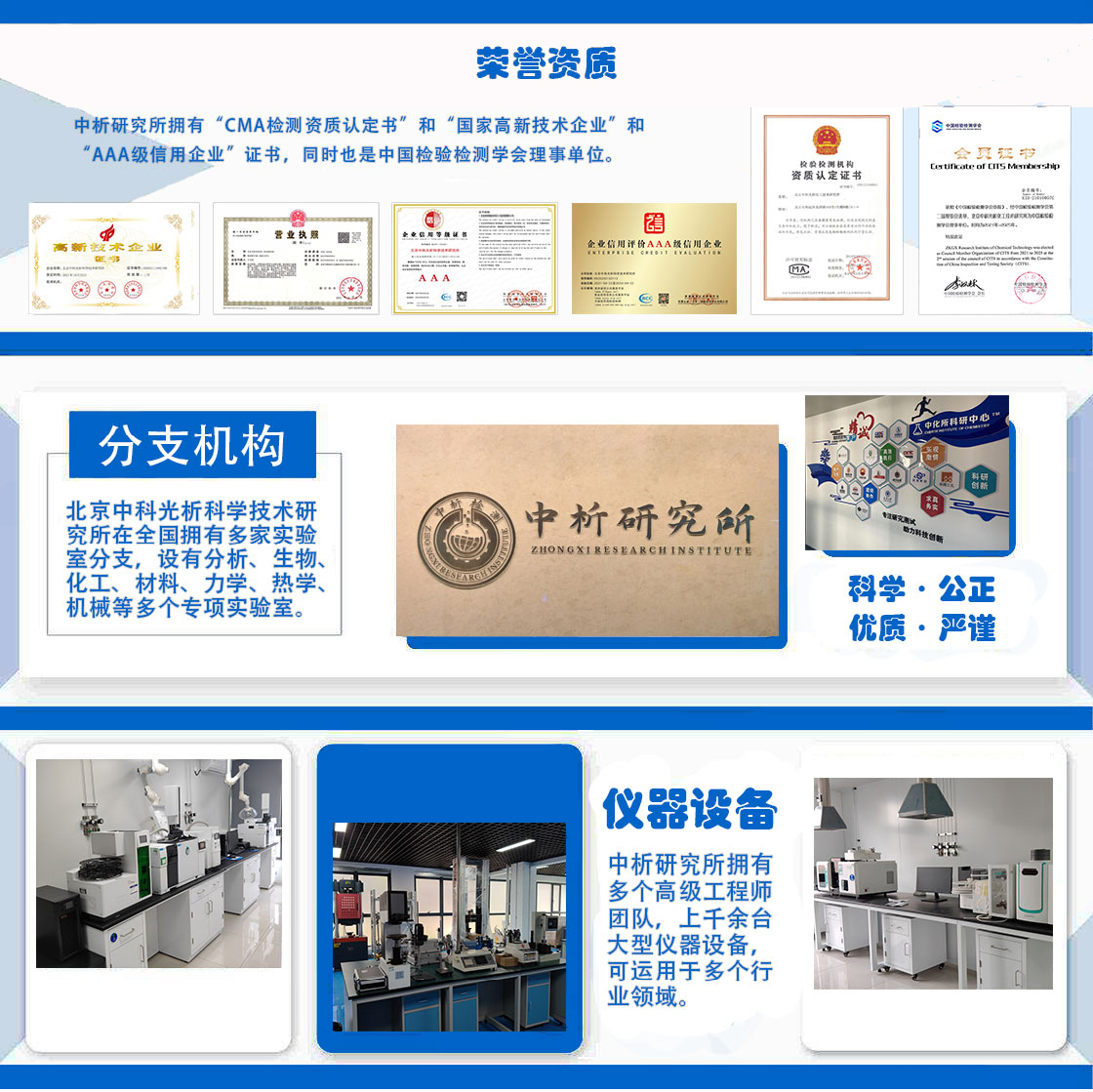
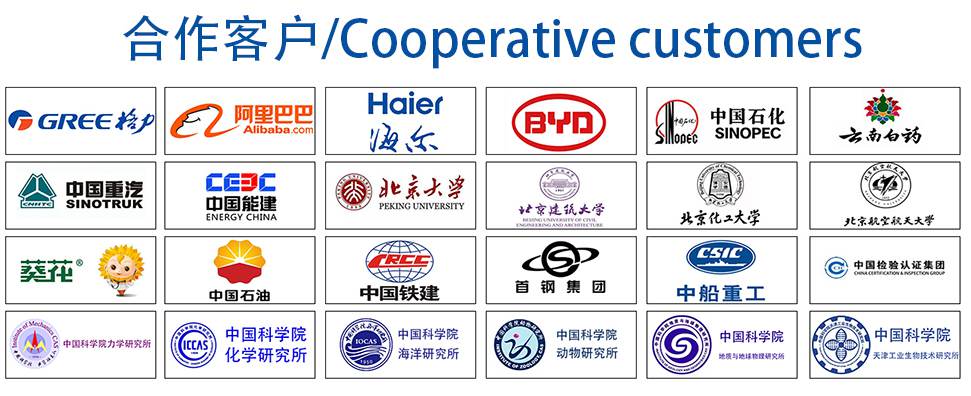