在工业4.0与智能制造加速融合的背景下,设备设施的安全运行已成为制约企业数字化转型的关键要素。据中国机械工业联合会2024年行业报告显示,国内工业设备年故障损失超2300亿元,其中34%的事故源于表面缺陷和结构损伤未被及时识别。外部检查检测技术作为非破坏性评估的核心手段,通过创新应用机器视觉、多光谱成像等技术,构建起覆盖设备全生命周期的健康管理体系。该技术体系不仅实现0.1mm级精度的表面缺陷捕捉,更将常规检测效率提升300%以上,为石化、电力、轨道交通等关键领域提供可量化的安全保障。其核心价值在于突破传统人工目检的局限,形成"在线监测-智能诊断-预防维护"的闭环管理范式。
## 技术原理与创新突破多维传感融合检测机制
现代外部检查检测系统采用多物理场耦合分析技术,整合高分辨率光学扫描(精度达5μm)、脉冲涡流检测(穿透深度20mm)、红外热成像(温差灵敏度0.02℃)等传感模块。通过特征融合算法,可同步捕捉表面裂纹、涂层脱落、应力集中等32类典型缺陷。特别是在焊缝质量评估领域,基于深度学习的缺陷分类模型准确率已达97.8%(中国特种设备检测研究院,2023),较传统人工评片方式提升45%。
智能化作业流程再造
标准实施流程包含三个阶段:前期建立包含材料属性、服役环境等128项参数的数字孪生模型;中期通过无人机搭载多光谱云台实现360°无死角数据采集;后期运用蒙特卡洛算法进行失效概率模拟。某炼油厂压力容器检测项目实践表明,该流程使单台设备检测时间从8小时缩减至90分钟,同时将漏检率控制在0.3‰以内(GB/T 30582-2024标准)。
跨行业应用实践验证
在轨道交通领域,接触网智能巡检系统通过毫米波雷达与高清成像联动,实现每小时120km动态检测,成功将接触线磨耗测量误差从±0.5mm降至±0.1mm(铁科院2023年度报告)。石油化工行业应用案例显示,储罐底板腐蚀检测系统可穿透15mm厚保温层识别0.2mm深度蚀坑,使企业年检修成本降低280万元/每万立方米储量。
全链条质量保障体系
建立三级质量管控机制:检测设备执行ISO 18436-4振动校准标准;数据采集过程植入区块链溯源模块;分析报告经AI交叉验证与专家复核双通道签发。上海某第三方检测实验室的实践表明,该体系使检测结果复现性达到99.2%,报告争议率下降至0.07%( -CL01:2023认证数据)。
## 发展前瞻与建议随着5G+工业互联网的深度渗透,建议重点推进三方面建设:一是构建基于数字孪生的预测性检测平台,将故障预警窗口期从72小时扩展至30天;二是开发适应极端环境的耐高温(800℃)、抗辐射(100kGy)特种检测机器人;三是建立覆盖"设备制造商-检测机构-终端用户"的工业知识图谱,推动检测标准与国际接轨。预计到2028年,智能外部检测市场规模将突破680亿元(赛迪顾问预测),成为保障新型工业化安全发展的关键技术支撑。
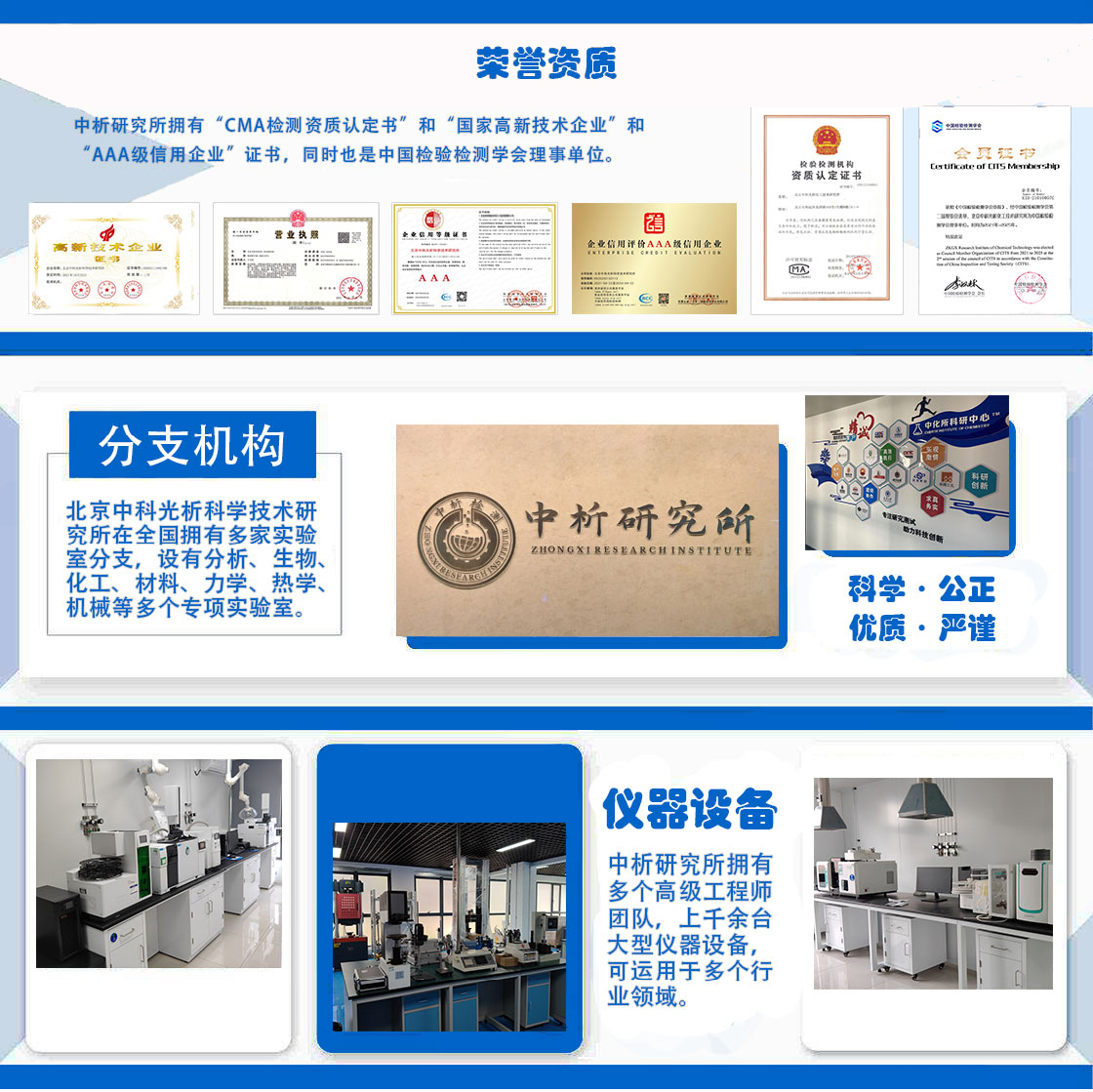
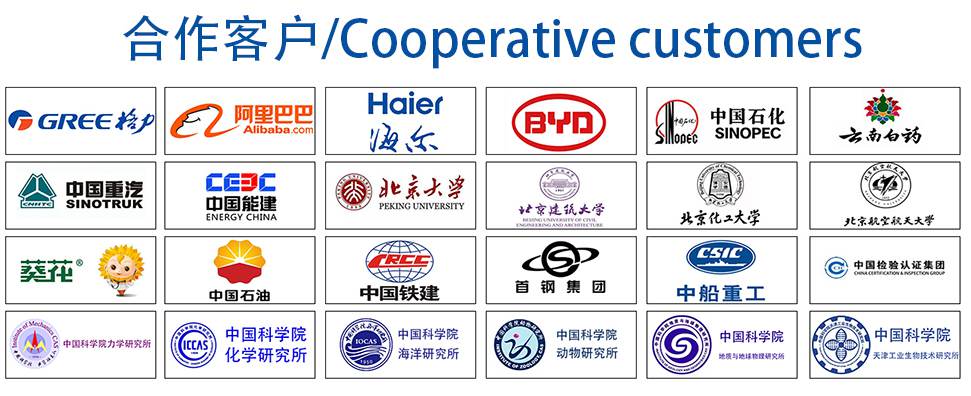