管材爆破试验检测:核心检测项目与流程解析
一、试验目的
二、检测核心项目
-
- 定义:管材在持续增压下发生破裂时的临界压力值。
- 检测方法:
- 逐步加压至管材破裂,记录峰值压力(MPa)。
- 根据公式计算理论爆破压力,与实际值对比验证材料性能。
- 公式示例(薄壁管): ��=2��⋅��Pb=D2σb⋅t 其中,��σb为材料抗拉强度,�t为壁厚,�D为外径。
-
- 膨胀率:破裂前管径的局部或整体膨胀程度,反映材料塑性变形能力。
- 塑性变形量:通过激光测距仪或应变片监测加压过程中的管壁形变,绘制压力-变形曲线。
-
- 裂纹形态:纵向裂纹(韧性断裂)或横向断裂(脆性断裂)。
- 破裂位置:焊缝、管壁薄弱点或随机分布,判断材料均匀性及工艺缺陷。
-
- 在初始压力下检测管材是否泄漏,排除因密封不良导致的试验误差。
-
- 记录压力-时间曲线、破裂瞬间压力波动及环境温度。
- 对比不同批次管材的数据一致性,评估生产工艺稳定性。
三、试验标准与设备
-
- 国际标准:ISO 1167、ASTM D1599
- 国内标准:GB/T 15560、GB/T 6111(塑料管材)
-
- 液压系统:可编程增压泵(精度±1%FS)。
- 夹具:定制化密封夹具,适配不同管径(如DN20~DN500)。
- 数据采集仪:同步记录压力、变形、温度等参数。
- 高速摄像机(选配):捕捉破裂瞬间动态过程。
四、试验步骤示例
-
- 截取3~5倍管径长度的管段,端口打磨平整。
- 标记测量点,安装应变传感器。
-
- 施加10%预期爆破压力,保压5分钟,检查泄漏。
-
- 按标准速率(如1 MPa/s)均匀增压,实时监测数据。
- 持续至管材破裂,记录爆破压力及失效形态。
五、结果应用与判据
-
- 实测爆破压力 ≥ 设计压力 × 安全系数(通常3~4倍)。
- 破裂模式符合预期(如塑性变形充分,无明显工艺缺陷)。
-
- 案例1:爆破压力低于理论值 → 材料杂质或壁厚不均。
- 案例2:脆性断裂 → 热处理不当或低温环境下韧性不足。
六、应用领域
- 金属管材:石油管道、高压锅炉管。
- 塑料管材:PE给水管、PPR热水管。
- 复合材料管:航空航天液压管路。
七、注意事项
- 试验环境需符合标准温湿度要求(如23±2℃)。
- 操作人员需穿戴防护装备,防止高压液体飞溅。
- 设备定期校准,确保数据准确性。
八、总结
上一篇:重油中总氮分析检测下一篇:电气照明设备和类似设备检测
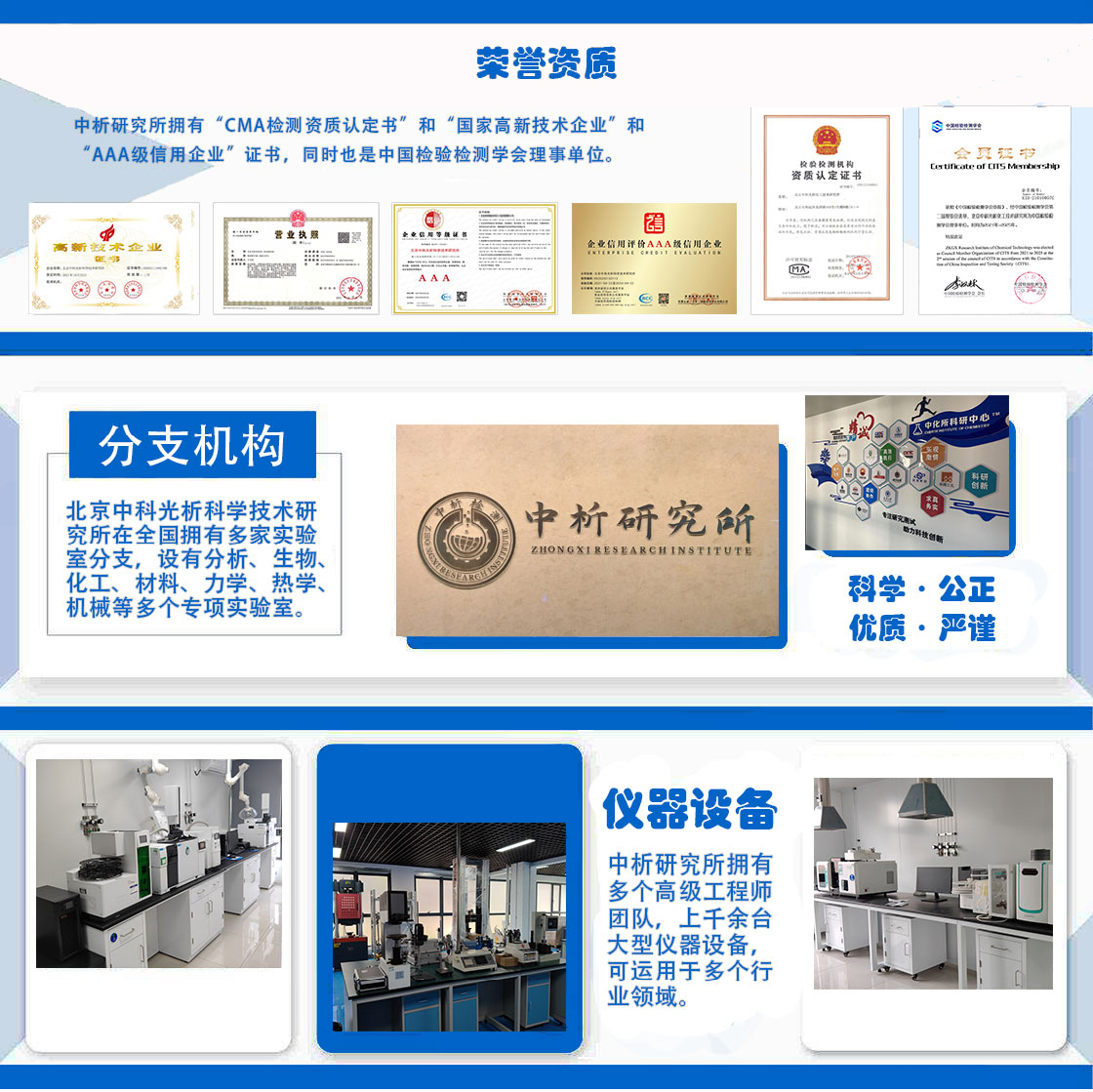
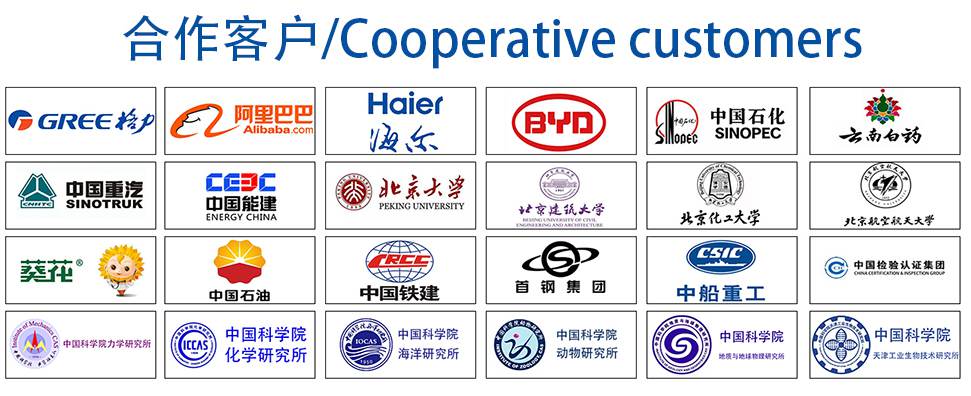
材料实验室
热门检测
19
20
18
19
23
21
19
26
33
23
25
28
21
18
23
19
21
19
22
15
推荐检测
联系电话
400-635-0567