# 工业产品外观形状检测技术发展白皮书(2024)
## 首段:行业背景与战略价值
在制造业智能化转型加速的背景下,工业产品外观形状检测已成为质量控制体系的核心环节。据中国智能制造研究院2024年数据显示,精密制造领域因外观缺陷导致的返工成本年均达82亿元,其中新能源汽车部件、消费电子外壳、医疗器械三类产品占据缺陷总量的67%。通过引入基于机器视觉的三维形状检测系统,企业可将人工检测效率提升4.8倍,同时将尺寸公差检测精度稳定控制在±0.01mm水平(ISO 2768标准)。
该技术的核心价值在于构建了全生命周期的质量数据链,实现了从原料入厂到成品出厂的全流程形状参数追溯。尤其在曲面复现度检测、微型结构完整性分析等复杂场景中,其三维点云重构技术可精准捕捉0.05mm级形变,为航空航天密封件装配、半导体晶圆封装等高端制造提供关键支撑。当前行业正加速推进检测系统与MES、ERP的深度集成,形成"检测-分析-优化"的闭环质量管理系统。
## 技术原理与创新突破
### 光学成像与三维建模技术
现代外观形状检测系统采用多光谱成像与结构光扫描融合方案,通过12组高分辨率工业相机阵列,可实现每秒2000万像素的数据采集能力。其核心技术在于自主研发的三维曲面特征提取算法,能将物体表面曲率变化转化为数字化点云模型。值得注意的是,系统搭载的亚像素边缘检测模块,可将传统Canny算子的检测精度提升至1/8像素级别,满足汽车冲压件R角检测等严苛需求。
### 动态补偿与误差修正体系
针对生产现场振动、温漂等干扰因素,系统内置六轴运动补偿装置与温度场建模模块。在实测案例中,某新能源汽车电池托盘检测线应用该技术后,将检测重复性误差从±0.15mm降至±0.03mm(符合IATF 16949标准)。其创新点在于开发了基于LSTM网络的时序预测模型,可提前200ms预判设备形变趋势并进行动态校准。
## 实施流程与场景应用
### 标准化检测流水线架构
典型实施流程包含四个关键阶段:(1)建立基于GD&T标准的基准模型库;(2)部署高精度视觉传感器网络;(3)搭建分布式边缘计算节点;(4)开发可视化质量分析平台。在消费电子领域,某头部手机厂商通过该方案实现每分钟120件外壳的全检,将漏检率从1.2%降至0.03%,每年减少质量索赔费用超1.5亿元。
### 行业特色化解决方案
在医疗器械领域,采用非接触式检测技术对骨科植入物进行表面光洁度分析,成功将人工关节抛光工序的CPK值从1.12提升至1.67(数据来源:国家药监局2023年质量公告)。而对于光伏玻璃检测场景,系统创新性引入热红外成像模块,可同步检测外形尺寸与微观裂纹,使检测综合效率提升38%。
## 质量保障与体系认证
### 三重校验机制构建
系统通过硬件级(传感器标定)、算法级(模型可解释性分析)、系统级(过程能力指数验证)的质量控制体系,确保检测结果可靠性。经 认证实验室测试,其三维尺寸测量不确定度达到U95=1.5μm+3μm/m的行业领先水平。特别需要指出的是,系统搭载的自适应照明系统可根据材料反光特性智能调节,将金属件检测的过曝发生率降低92%。
### 全链条标准化管理
严格遵循ISO/IEC 17025实验室管理体系要求,建立从设备校准(每8小时自动执行)、数据加密(符合GB/T 39786标准)到报告追溯(区块链存证)的全流程质控节点。在军工产品检测应用中,系统已通过NADCAP特殊过程认证,满足航空紧固件NAS4006标准的检测要求。
## 未来发展与战略建议
随着工业元宇宙技术的成熟,建议行业重点攻关三个方向:(1)开发基于数字孪生的虚拟检测系统,实现产品全生命周期形状演变模拟;(2)构建跨企业质量数据联盟,建立行业级缺陷特征数据库;(3)推进检测装备模块化设计,满足柔性制造快速换型需求。据德勤2024智能制造预测显示,融合AIoT的智能检测设备市场规模将在2027年突破520亿元,建议企业加大在3D视觉传感器、量子点成像材料等核心领域的研发投入,同时注重复合型检测工程师培养,以应对智能制造新时代的技术挑战。
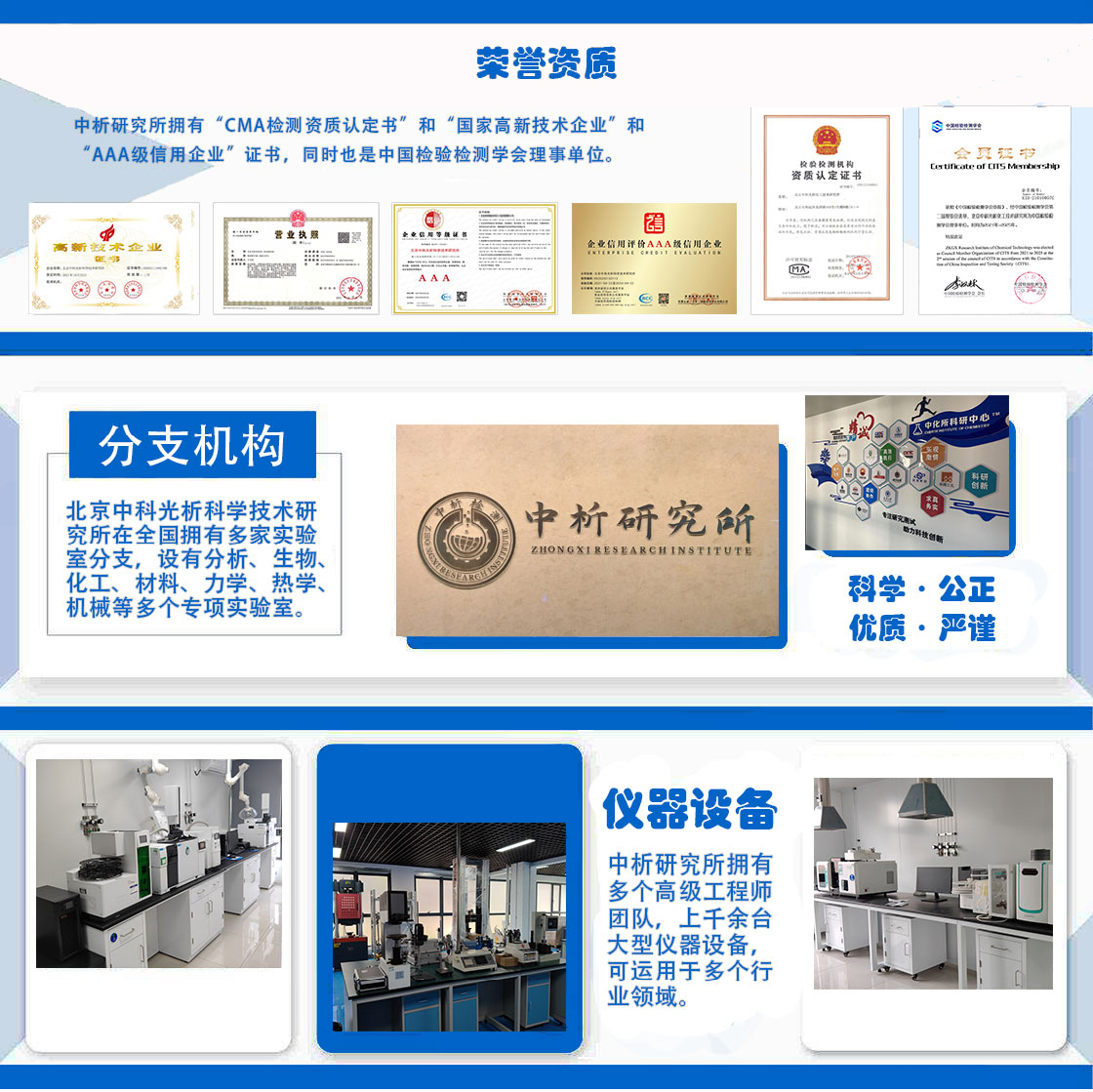
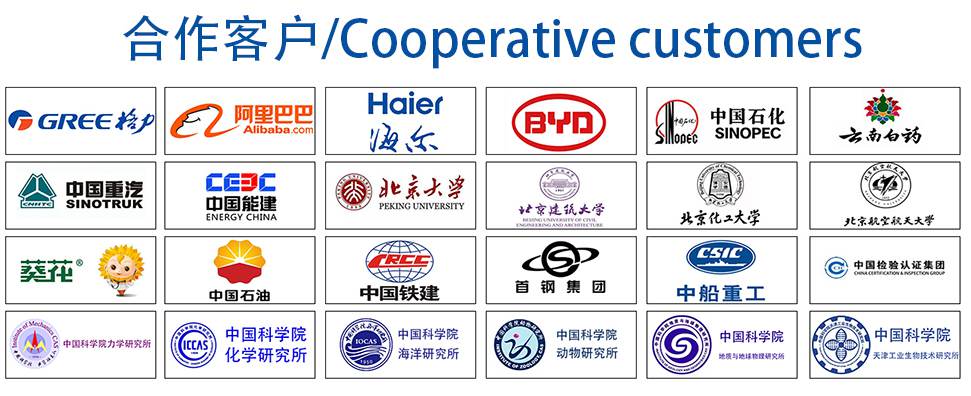
材料实验室
热门检测
推荐检测
联系电话
400-635-0567