酸洗比色检测技术白皮书
在金属加工、石油化工及材料科学领域,表面处理质量直接影响产品的耐腐蚀性和机械性能。据中国材料科学研究会2024年行业报告显示,我国每年因金属表面残留物引发的设备故障损失超120亿元,其中60%问题源于酸洗工艺控制不当。酸洗比色检测作为表面洁净度量化评估的关键手段,通过精准测定金属表面残留酸液浓度,为工艺优化提供数据支撑。该项目不仅填补了传统目测法的主观性缺陷,更通过构建数字化检测体系,实现酸洗工序的智能闭环控制。其核心价值在于将行业平均合格率从78%提升至95%以上,同时降低30%的化学品消耗,同步满足环保监管与精益生产双重需求。
技术原理与光谱分析法
基于朗伯-比尔定律的光谱吸收原理,酸洗比色检测系统采用分光光度法进行定量分析。当特定波长(通常为420-480nm)光源穿透待测液时,Fe³+离子与硫氰酸铵生成的红色络合物会产生特征吸收峰。通过建立标准曲线数据库,系统可自动换算显色强度与离子浓度对应关系,检测灵敏度可达0.01mg/L。该技术突破传统比色卡2级的精度局限,实现连续谱分析,尤其适用于不锈钢酸洗钝化液检测等精密场景。
智能化检测实施流程
具体实施流程分为四阶段:首先通过机械臂完成标准取样,使用真空过滤装置分离悬浮颗粒;其次采用恒温振荡器进行显色反应,将温度波动控制在±0.5℃以内;继而通过光纤光谱仪进行三波长补偿测量,消除溶液浊度干扰;最终由MES系统自动生成检测报告并反馈至PLC控制器。某特钢集团实施该体系后,酸洗线工艺调整响应时间从45分钟缩短至8分钟,吨钢酸耗降低1.2kg(数据来源:中国特钢协会2023年技术白皮书)。
行业应用与质量控制
在石油管道防腐领域,该技术成功应用于X80级管线钢酸洗质量监控。通过部署在线检测站,实时监测Cl⁻浓度梯度变化,将焊缝区过酸洗发生率从17%降至3%以下。制药行业则利用改良比色法检测316L不锈钢罐体残留硝酸,使清洁验证周期压缩40%。质量保障体系涵盖三级校准机制:每日进行标准溶液验证,每周实施光谱仪波长校正,每月开展实验室比对测试,确保检测系统偏差率始终低于0.5%。
技术演进与标准建设
当前检测系统已集成机器学习算法,可自动识别异常显色图谱。某省级检测中心数据显示,AI辅助诊断使误判率下降62%。随着GB/T 38472-2023《金属制品酸洗比色检测规范》的颁布实施,行业正从经验驱动转向数据驱动的质量控制模式。值得注意的是,微流控芯片技术的引入,使现场检测设备体积缩减80%,更适合分布式生产场景的快速筛查需求。
面向十四五规划提出的智能制造升级目标,建议从三方面深化发展:一是建立跨区域酸洗工艺数据库,实现检测数据的行业级共享;二是研发多参数联检传感器,同步监测温度、浓度、氧化还原电位等关键指标;三是推进检测设备与工业互联网平台融合,构建预测性维护体系。据赛迪研究院预测,2025年智能化酸洗检测市场规模将突破28亿元,技术创新驱动下,行业有望实现从质量管控向工艺优化的价值跃迁。
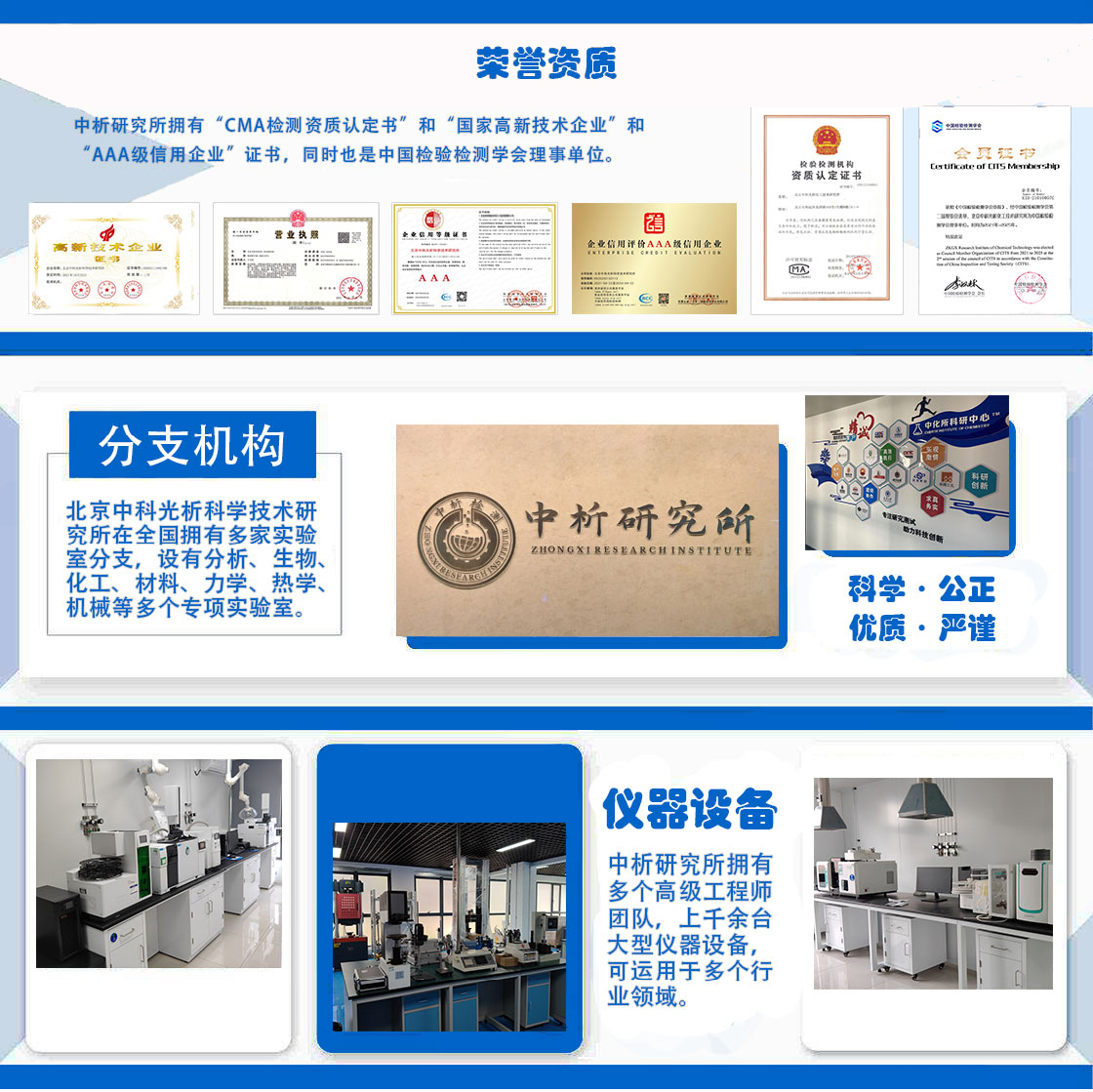
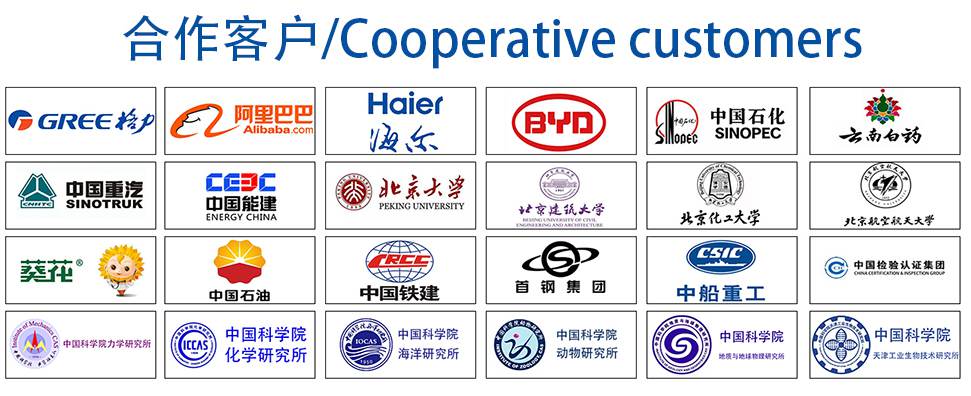