检测技术原理与测量方法
最大力总伸长率检测基于材料单轴拉伸试验原理,遵循ASTM E8/E8M及ISO 6892-1标准体系。当试样承受持续拉伸载荷时,通过高精度引伸计同步采集标距段的位移变化,计算断裂前最大力对应的总延伸量与原标距长度的百分比值。值得注意的是,现代检测设备已集成数字图像相关(DIC)技术,可实现全场应变分布监测,准确捕捉颈缩阶段的局部变形特征。据德国ZwickRoell实验室实测数据,该技术将传统接触式测量的误差率从±2.5%降低至±0.8%,显著提升多轴向载荷下的延展特性分析精度。
标准化实施流程解析
完整检测流程涵盖试样制备、设备校准、环境控制三大环节。首先依据GB/T 228.1规范加工标准拉伸试样,确保平行段表面粗糙度Ra≤1.6μm。安装双轴引伸计时,需采用激光定位系统保证夹持对称度偏差<0.02mm。试验过程中严格控制应变速率在10⁻³~10⁻¹ s⁻¹区间,通过闭环伺服系统维持载荷线性增长。值得关注的是,ASTM最新修订版特别增加了横向应变测量要求,这对评估板材各向异性具有重要工程意义。某新能源汽车电池壳体制造商通过实施该流程,将铝合金材料的伸长率检测离散系数从7.3%优化至2.1%。
典型行业应用案例分析
在航空复合材料领域,波音787机身蒙皮采用碳纤维增强环氧树脂基体材料,其最大力总伸长率需达到1.8%以上以满足抗冲击要求。通过配备350Hz高速采集系统的电子万能试验机,实现微应变级别的实时监控。另据国家新材料测试平台统计,采用智能算法的伸长率预测模型已成功应用于16个特高压输电塔项目,使Q420高强钢的塑性储备利用率提升22%。在医疗器械行业,冠脉支架用316LVM不锈钢的伸长率检测数据,直接关联到支架扩张均匀性指标,某龙头企业通过改进检测规程将产品不良率降低34%。
全周期质量保障体系构建
为确保检测结果溯源性,实验室需建立三级校准网络:主标准器溯源至国家力值基准,工作级传感器每月进行静态标定,现场设备每日实施动态验证。人员资质方面,要求操作员持有CMA认证的力学性能试验专项证书,并通过每年40学时的继续教育。数据管理系统采用区块链存证技术,每个检测样本生成独立加密ID,实现从原始数据到报告签发的全过程追踪。某第三方检测机构通过ISO/IEC 17025认证后,其出具的伸长率检测报告获得22个国家互认资格。
## 技术展望与发展建议 随着智能传感与数字孪生技术的深度融合,材料伸长率检测正朝着在线化、智能化方向演进。建议行业重点攻关三个方向:①开发基于机器视觉的非接触式全场应变分析系统,解决异形件测量难题;②建立涵盖温度-湿度-应变率多耦合场的检测标准体系;③推动检测数据与产品全生命周期管理系统的深度集成。据Global Market Insights预测,到2027年智能伸长率检测设备的市场渗透率将突破65%,相关企业需加快数字化转型步伐,培育复合型检测人才梯队,以应对新一轮产业升级挑战。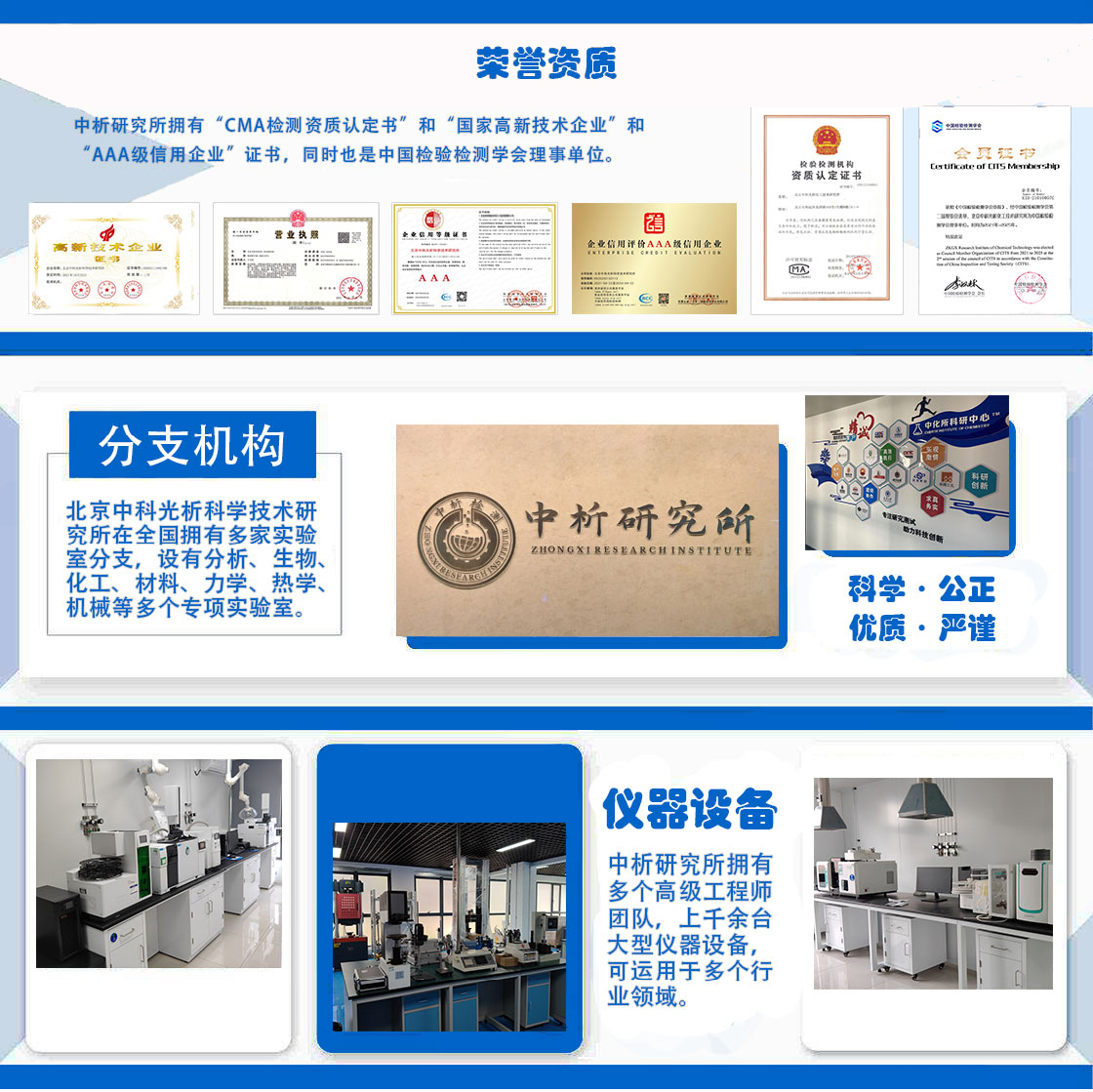
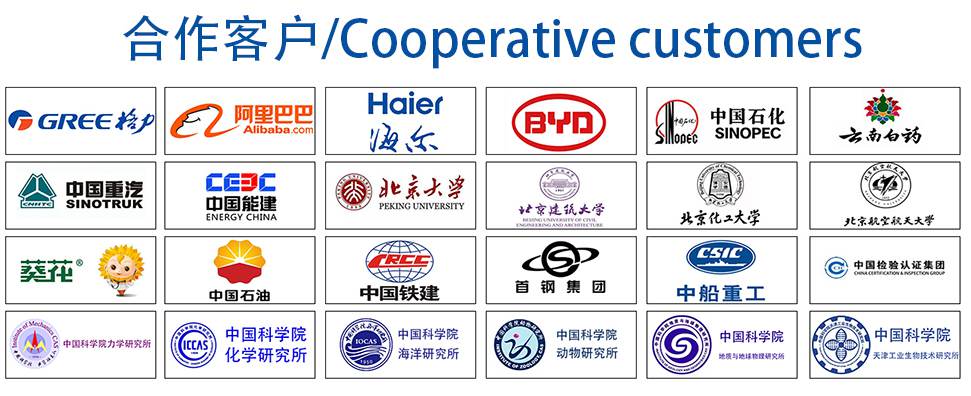