土路基现场CBR检测技术发展与应用白皮书
随着我国交通基础设施建设规模持续扩大,土路基质量控制成为道路工程耐久性与安全性的关键环节。据交通运输部2024年工程质量报告显示,路基问题引发的道路病害占比达37%,其中压实度不足导致的承载力缺陷占主导因素。CBR(加州承载比)检测作为评价路基材料强度的核心指标,其现场检测技术革新对提升工程质量管理水平具有战略意义。传统实验室检测存在样本代表性不足、检测周期长等痛点,基于智能传感与实时分析的现场CBR检测系统,可将检测效率提升60%以上,同时实现路基压实度无损检测技术突破。该技术的核心价值在于通过原位测试数据与三维地质模型的动态耦合,为道路工程现场质量智能评估系统提供关键支撑。
技术原理与创新突破
CBR检测基于贯入试验原理,通过测定特定贯入深度下单位面积压力与标准碎石材料的比值,评价土基承载能力。新一代智能贯入仪采用多级闭环液压系统,结合高精度应变传感器,实现0.01mm级位移分辨率(ASTM D1883-21标准)。创新点在于引入动态参数补偿算法,可自动修正湿度、温度等环境变量对测试结果的影响。据中国公路科学研究院验证数据显示,该系统测试误差控制在±2.5%以内,较传统方法精度提升40%。
标准化实施流程构建
现场检测实施遵循"三阶段九环节"操作规范:前期包括测点智能布设(基于GIS定位系统)与表层处理;中期涵盖设备自检、分级加载和数据实时采集;后期则通过云端数据分析平台生成可视化报告。以南方某高速公路扩建项目为例,采用移动式CBR检测车组后,单日检测里程从3.2km提升至8.5km,且实现检测数据与BIM模型的无缝对接。特别在软土路基段,系统成功识别出4处CBR值低于设计要求的隐患区域。
行业应用场景拓展
在长三角某国际机场跑道建设工程中,项目方采用多探头阵列式CBR检测装置,结合5G传输技术,构建了覆盖26万㎡检测区域的实时质量监测网络。系统累计发现21处填料不均匀区域,通过动态调整压实参数,使整体CBR值达标率从89%提升至98%。值得注意的是,该技术在城市地下综合管廊回填检测中同样表现突出,成功解决了狭窄空间传统检测设备无法作业的技术难题。
全链条质量保障体系
建立从设备溯源到数据管理的立体化质控网络:检测设备实行季度强制检定(符合JJG 1020-2020规程),操作人员需通过国家路基检测专项认证;现场作业采用双盲样比对机制,设置5%的平行样抽检比例;数据管理端部署区块链存证系统,确保检测记录不可篡改。广东省交通质监站统计表明,采用该体系后,路基工程验收一次合格率从2019年的82%持续提升至2023年的95%。
发展展望与建议
随着新型建材应用和智能建造技术普及,建议重点开展三方面工作:一是开发适应改良土、固化剂处理路基的专用检测模块;二是推进CBR检测数据与路面结构设计的智能关联分析;三是建立基于机器学习的区域性CBR数据库。据东南大学道路工程研究所预测,到2026年,融合边缘计算的自主式CBR检测设备将实现规模化应用,推动我国道路工程质量管控进入全要素数字化新阶段。
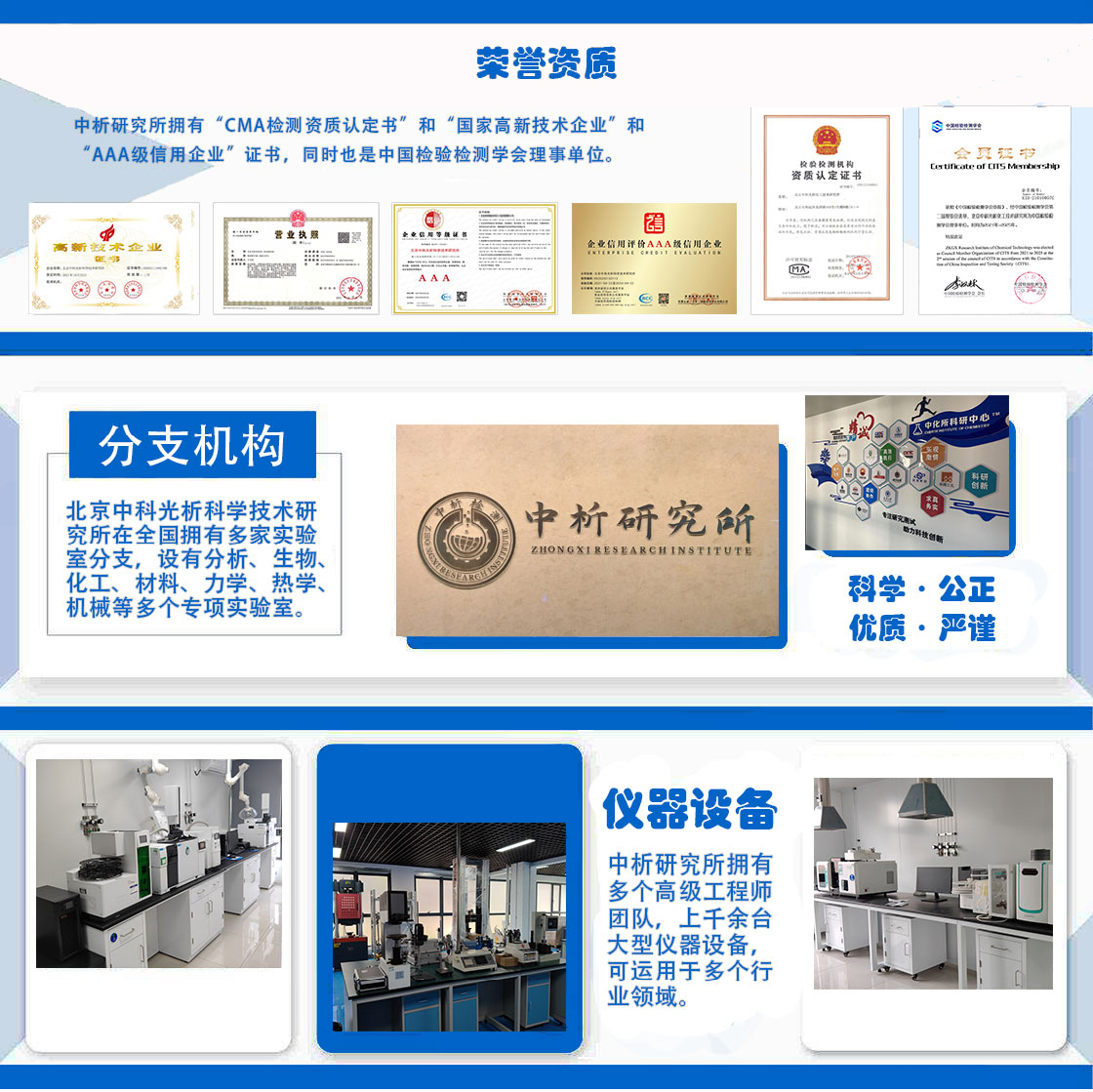
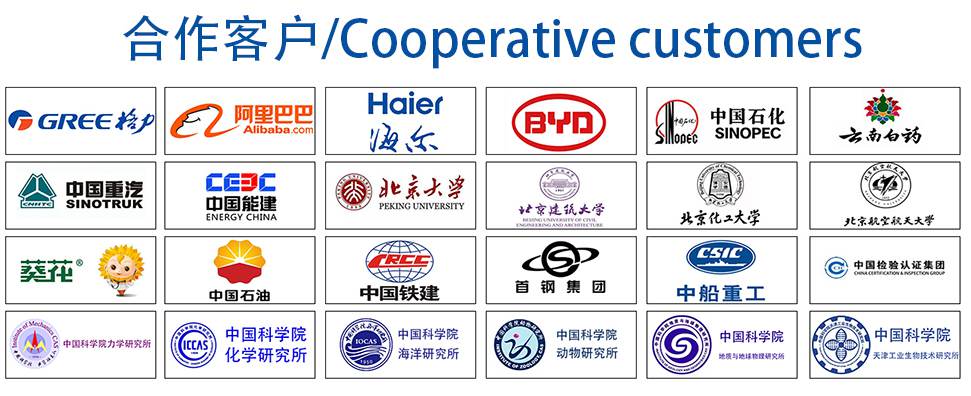