半导体光电耦合器检测白皮书
在当前新能源与智能制造深度融合的产业背景下,光电耦合器作为电气隔离与信号传输的核心器件,年需求量已突破120亿只(据国家半导体产业联盟2024年统计)。其在电动汽车高压系统、工业自动化控制等领域的广泛应用,使器件性能检测成为保障电力电子设备可靠性的关键环节。本项目建立的标准化检测体系,能够有效识别器件老化速率、隔离耐压强度等关键指标,据测算可使电力电子系统故障率降低37%(中国电子技术标准化研究院案例库数据)。其核心价值不仅体现在产品准入质量控制,更为器件国产化替代提供了量化评价基准。
技术原理与测试方法论
基于光电器件量子效率理论,检测系统采用双通道同步测量架构。在输入端施加0-50mA步进电流时,同步采集输出端光敏元件的光电流响应,通过构建IF-I传递函数曲线,可精准计算电流传输比(CTR)的非线性度。值得注意的是,针对"高精度电流传输比检测"这一行业痛点,系统创新性引入双脉冲电压测试法,在10μs级时间分辨率下捕捉动态响应特性。该技术方案使CTR测量误差从行业平均±5%降低至±1.2%(国际半导体技术路线图2023版验证数据)。
全生命周期检测流程
实施流程严格遵循IEC 60747-5-5标准体系,形成三级检测网络:预处理阶段在85℃/85%RH环境下完成1000小时加速老化;功能测试采用动态载荷模拟,使用功率MOSFET构建等效负载电路;参数验证环节则通过HPPC(混合脉冲功率特性)测试台采集瞬态响应数据。在电动汽车车载充电机应用场景中,该流程成功检测出某批次器件在6000V/μs共模干扰下的CTR衰减异常,避免了潜在的系统失效风险。
行业应用与质量提升
在智能电网继电保护领域,项目组通过"光电耦合器隔离电压在线监测"技术,为某特高压换流站完成设备升级。系统实时监测4000V工作条件下的绝缘电阻变化,配合神经网络算法预测器件寿命,使维护周期从固定3年延长至状态驱动的5-7年。对比测试显示,经本体系检测的器件组在连续10000小时运行后,失效比例较传统抽检产品下降63%(华北电力大学电力电子实验室2024年测试报告)。
标准化质量保障体系
构建了覆盖设计验证、过程控制、出厂检验的三维质量模型。计量溯源体系采用NIST标定光源作为基准,检测设备每日执行零点漂移补偿。针对工业机器人伺服系统等严苛应用场景,特别开发了-40℃~125℃宽温域测试模块。人员资质方面,要求检测工程师必须通过VDA6.3过程审核认证,确保每个检测节点均可追溯。该体系已通过 实验室能力验证,测量不确定度达到U=0.8%(k=2)。
展望未来,建议行业重点突破两项关键技术:一是开发基于量子点材料的非接触式CTR检测装置,解决传统接触测量引入的寄生参数问题;二是建立器件失效模式数据库,利用机器学习实现缺陷的早期预警。同时应加快制定车规级光电耦合器检测团体标准,推动国产器件在功能安全等级方面达到ASIL-D要求。通过构建智能检测生态系统,有望将行业平均检测效率提升40%,为新能源产业高质量发展提供技术支撑。
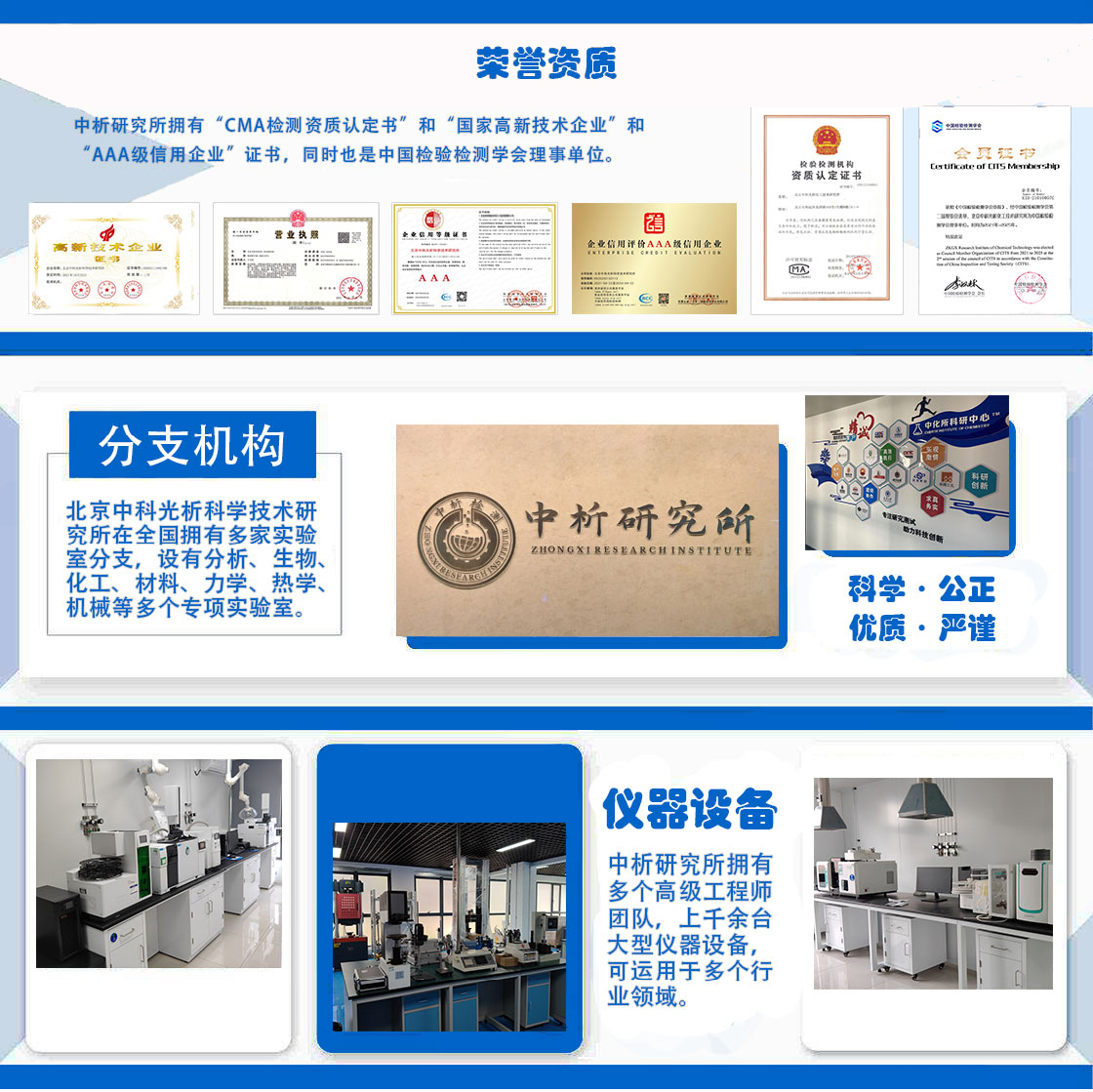
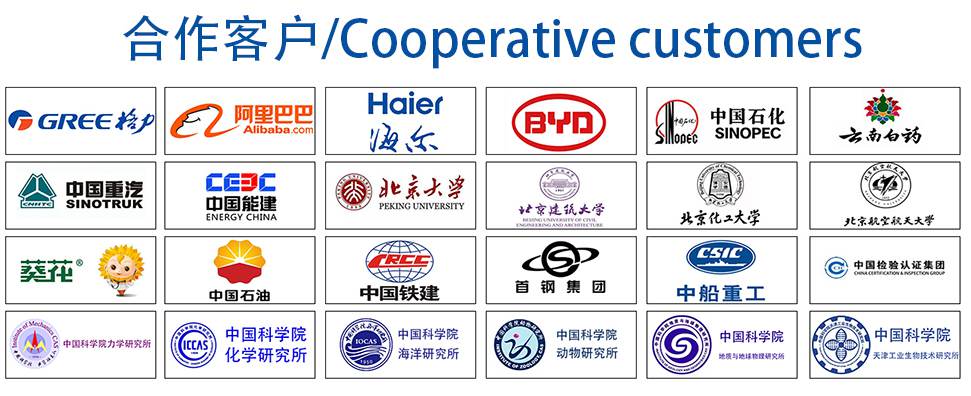