一、刹车系统组成与检测目标
- 刹车盘组件(碳/碳复合材料或钢制刹车盘)
- 作动系统(液压活塞、蓄压器、阀门)
- 传感器系统(温度、压力、磨损监测)
- 防滑控制系统(ABS功能模块)
二、核心检测项目分类
1. 目视与基础检查
-
- 检测内容:刹车盘表面裂纹、分层、烧蚀痕迹;作动机构油液泄漏、腐蚀。
- 工具:高倍放大镜、内窥镜(针对隐蔽区域)。
- 标准:依据AMM(飞机维护手册)判定缺陷等级。
-
- 检测内容:刹车盘厚度、摩擦材料剩余量(对比初始厚度)。
- 工具:数显卡尺、激光测厚仪。
- 标准:磨损超过制造商规定的最大允许值(通常为原始厚度的50%)需更换。
2. 功能测试
-
- 检测内容:液压作动压力稳定性、响应时间。
- 方法:模拟刹车指令,记录压力上升速率及峰值是否符合手册阈值(如波音737NG要求液压压力≥3000 psi)。
- 工具:压力传感器、数据采集系统。
-
- 检测内容:防滑控制逻辑、作动频率。
- 方法:在试验台模拟滑移条件,验证系统能否快速调整刹车压力。
- 标准:刹车力矩波动幅度需控制在±5%以内。
3. 性能测试
-
- 检测内容:不同压力下的制动力矩输出。
- 工具:力矩传感器、动态加载装置。
- 标准:输出力矩需与手册曲线匹配,偏差>10%判定为异常。
-
- 检测内容:模拟多次刹车循环(如起飞中断时的最高能量刹车)。
- 方法:在台架试验中施加高能载荷(如能量密度≥200 MJ/m²),检测刹车盘是否有热裂纹或变形。
- 标准:连续10次循环后,刹车效率下降不得>15%。
4. 无损检测(NDT)
-
- 检测内容:刹车盘内部微小裂纹、材料缺陷。
- 工具:涡流探伤仪,频率范围1-5 MHz。
- 标准:缺陷深度>0.5 mm或长度>3 mm需报废。
-
- 检测内容:复合材料刹车盘的分层、脱粘。
- 方法:使用纵波探头,检测信号衰减情况。
- 标准:分层面积超过5%总表面积需修复或更换。
5. 特殊环境测试
-
- 检测内容:-40℃环境下液压油黏度对刹车响应的影响。
- 方法:环境舱模拟极寒条件,测量作动延迟时间。
- 标准:延迟时间<1.5秒(参考SAE AS1245)。
-
- 检测内容:金属部件(如活塞杆)的耐腐蚀性。
- 标准:按ASTM B117进行48小时测试,表面锈蚀面积<0.1%。
三、检测周期与记录管理
- 周期要求:
- 日常航线检查:每次飞行后目视检查。
- 深度检测:每500次起落或1年(以先到者为准)。
- 数据管理:使用电子履历系统(如TRUEngine)记录检测结果,关联部件序列号,实现全寿命追溯。
四、案例分析:典型故障与检测对策
-
- 故障现象:着陆时刹车震颤。
- 检测手段:涡流检测发现深度1.2 mm裂纹。
- 处理措施:更换刹车盘并升级为抗疲劳涂层型号。
-
- 故障原因:低温下密封圈硬化导致泄漏。
- 解决方案:更换氟橡胶密封件,并通过压力曲线测试验证。
五、
上一篇:飞机航空机轮和刹车装置检测下一篇:氟苯尼考(氟甲砜霉素)检测
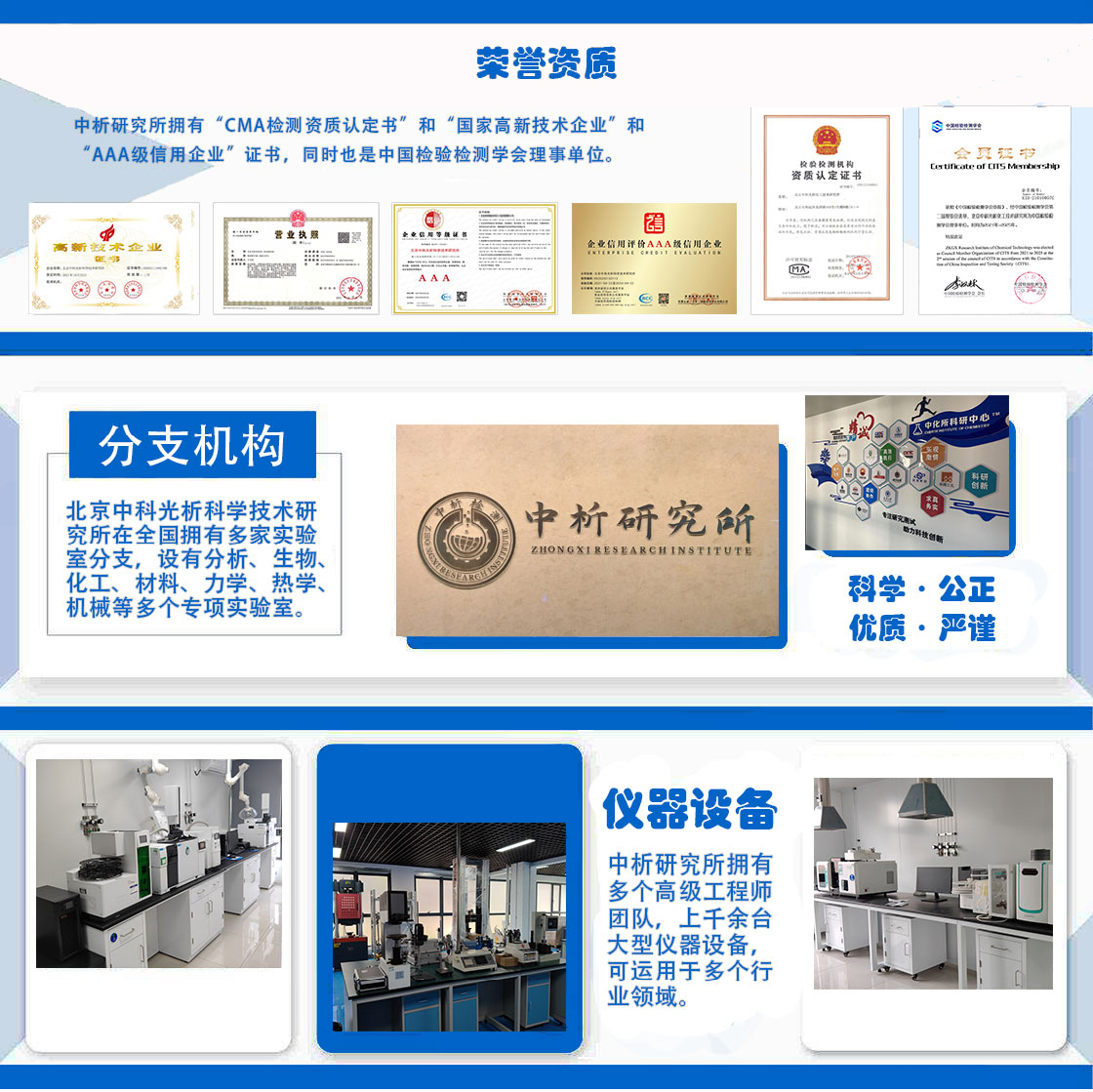
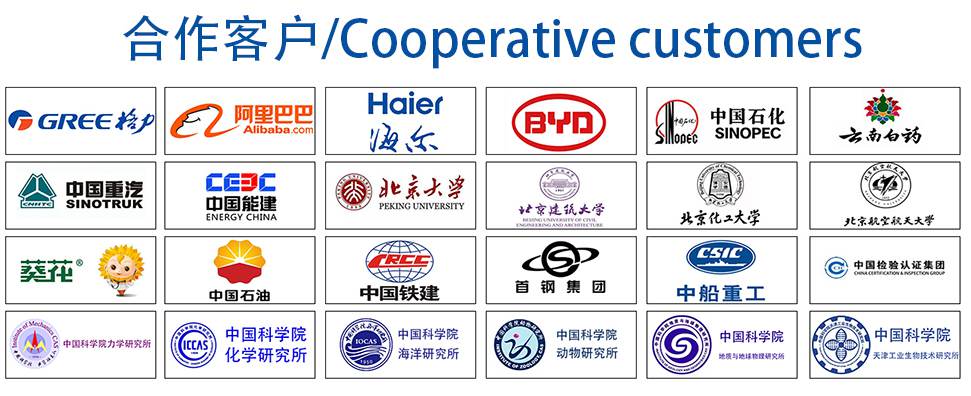
材料实验室
热门检测
推荐检测
联系电话
400-635-0567