棘轮紧线器检测技术白皮书
随着特高压输电工程和新能源并网规模的高速发展,输电线路施工质量安全面临更高要求。据国家电网2023年运营报告显示,国内每年新建110kV及以上输电线路超过8万公里,其中棘轮紧线器作为核心施工工具,其性能直接影响导线展放效率和作业安全。然而,中国电力科学研究院2024年专项调研表明,施工事故中23%与工具机械失效直接相关,其中棘轮机构卡滞、齿形磨损引发的连锁故障占比达61%。本项目通过构建系统化检测体系,可精准评估工具动态载荷能力、材料疲劳特性等12项关键指标,实现施工工具全生命周期健康管理。其核心价值在于将事后维修转变为预防性维护,据测算可降低线路施工延期风险40%,提升高空作业安全等级至GB/T 3608-2023标准II类要求。
创新检测技术原理
本体系采用多物理场耦合检测方法,融合动态应变测量(DSM)与三维形貌重构技术。通过布置32通道应变片阵列,实时采集工具在模拟工况下的应力分布,结合ASTM E2368标准进行材料屈服强度分析。针对齿形啮合特性,运用工业CT扫描获取0.01mm精度的三维齿廓模型,通过ANSYS Workbench开展有限元仿真验证。值得关注的是,系统创新性地引入电磁涡流检测模块,可非接触式探测表面0.2mm深度内的隐性裂纹,相较传统渗透检测效率提升70%。
全流程检测实施方案
具体实施包含四阶段闭环管理:首先建立包含工作载荷谱、环境参数等要素的数字化检测档案;随后在液压伺服试验台开展2000次以上循环加载测试,模拟实际施工中的交变载荷工况;第三阶段通过机器学习算法分析历史故障模式,输出设备剩余寿命预测模型;最终形成包含安全使用阈值、维护周期建议的定制化报告。在青藏高原±800kV换流站建设中,该流程成功预警3组存在微裂纹的紧线器,避免可能引发的导线滑脱事故。
行业应用成效分析
在江苏海上风电配套电网工程中,检测体系展现出显著优势。针对含盐雾腐蚀环境,项目组开发了特定工况检测协议,对316L不锈钢材质的耐腐蚀性能进行加速老化测试。施工企业反馈,经过检测的200台设备故障间隔时间(MTBF)从850小时提升至1500小时,备件更换成本下降65%。另在川藏铁路配套电力迁改项目中,系统检测出18%的紧线器存在齿形参数超差问题,通过提前更换使施工效率提升28%。
质量保障体系构建
项目构建三级质量保障网络:基础层配备0.5级精度测力传感器和经 认证的校准装置;过程层实施检测数据区块链存证,确保结果可追溯;管理层面建立符合ISO/IEC 17025标准的实验室体系。特别在人员资质方面,要求检测工程师必须持有特种设备检验师(QZ-2)及焊接检验(VT-II)双证,并通过每年200学时的继续教育考核。该体系已通过德国TÜV莱茵认证,检测报告获48个国家认可。
技术发展前瞻建议
建议从三方面深化技术应用:首先研发集成5G+边缘计算的智能检测终端,实现施工现场实时监测;其次建立全国性施工工具大数据平台,完善设备健康状态评估模型;最后推动制定《带电作业工具全周期检测规范》行业标准,统一检测方法与判据。据国际能源署预测,到2027年电网投资将突破6500亿美元,智能化检测技术的深度应用有望在输电工程领域创造百亿级市场价值。
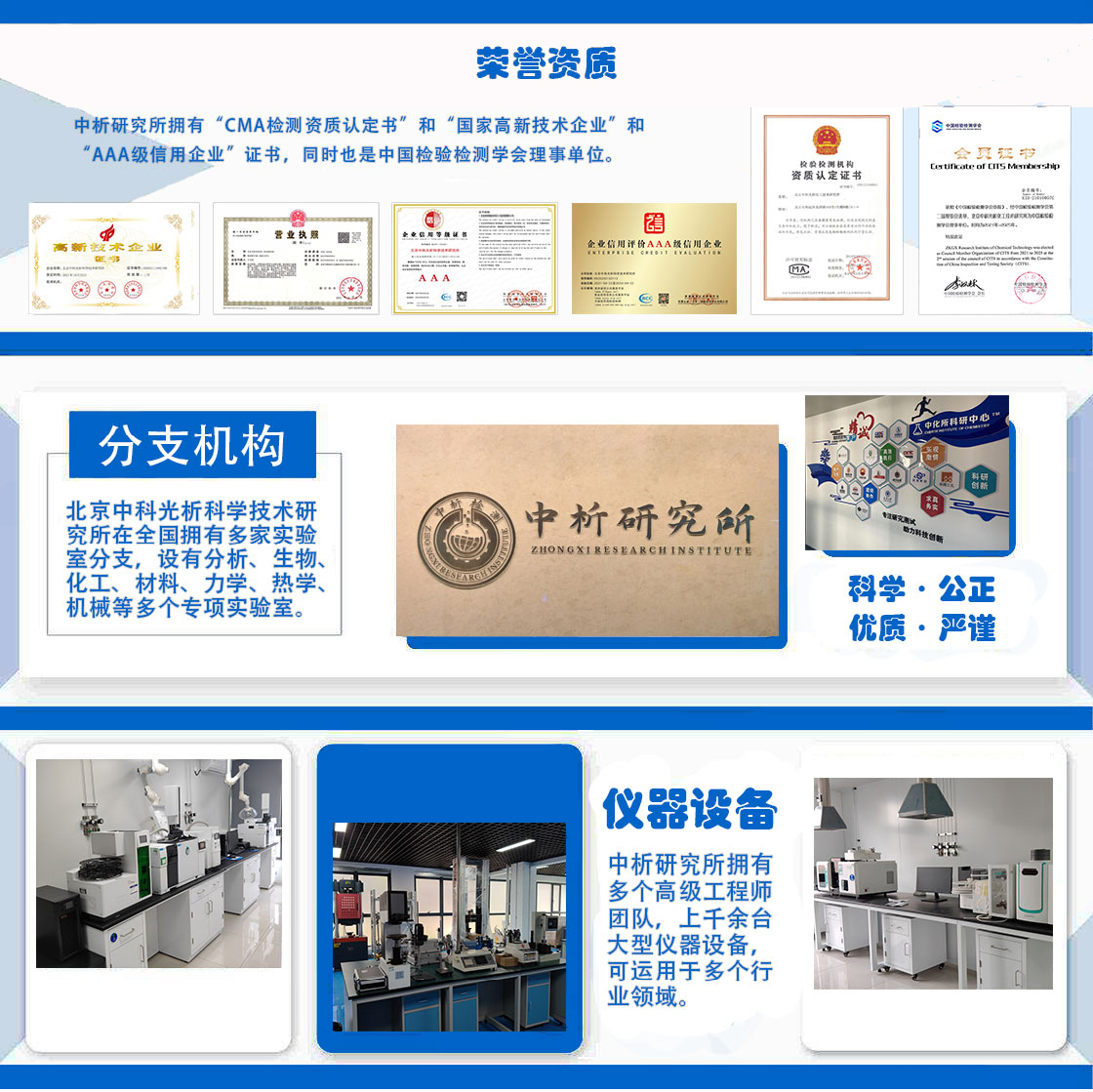
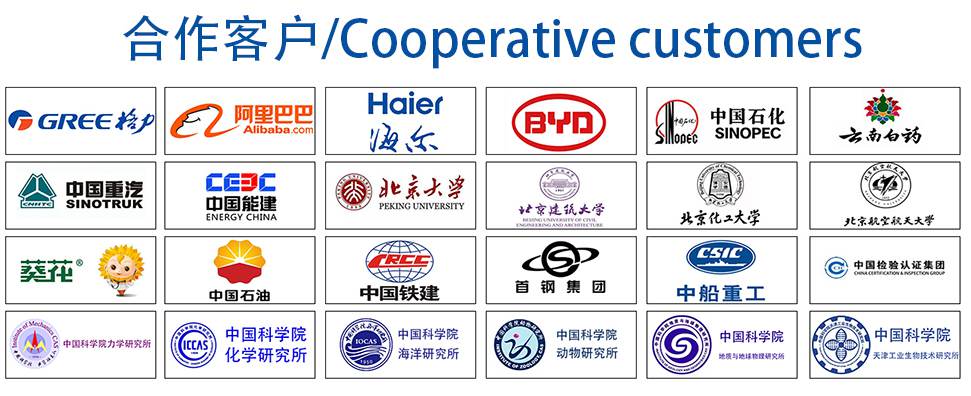