技术原理:多维度迁移特征解析
迁样方法检测基于机器学习与信号处理技术融合,重点攻克样本迁移过程中的多维特征解耦难题。通过部署分布式传感器阵列,系统实时采集温度梯度、应力分布、流体动力学等12类工艺参数,结合改进型卷积神经网络(CNN)构建迁移特征图谱。尤其在晶圆制造场景中,系统可识别厚度偏差低至0.8nm的薄膜沉积异常(数据来源:半导体协会技术年报)。区别于传统SPC控制,该技术引入迁移学习框架,使模型在更换生产批次时保持85%以上的参数复用率,大幅降低新工况下的模型训练成本。
实施流程:全链路智能化升级
项目实施采用五阶段渐进式部署:首先通过3D激光扫描建立产线数字孪生模型,完成设备级数据映射;其次构建迁移特征数据库,涵盖300+种典型工艺场景;随后开发自适应检测算法模块,实现毫秒级异常定位;最终形成闭环控制系统,并与MES平台深度集成。以某光伏电池片企业应用为例,在引入在线迁样检测系统后,其镀膜工序的工艺调整响应速度从4.2小时缩短至18分钟,碎片率下降2.3个百分点(企业实测数据)。
行业应用:跨领域场景落地
在生物制药领域,迁样方法检测成功应用于发酵过程优化。某龙头药企采用基于迁移学习的细胞活性预测模型,将单批次培养周期从14天压缩至11天,同时将目标产物浓度标准差控制在±1.2%以内(数据来源:国家药品审评中心技术报告)。而在3D打印行业,系统通过实时监测粉末床迁移状态,使航空钛合金构件的孔隙率从0.15%降至0.06%,达到AS9100D航标认证要求。
质量保障:四维认证体系构建
为确保检测结果可靠性,项目建立包含设备精度、算法鲁棒性、数据完整性和人员操作的四维认证体系。所有传感器均通过NIST三级校准,算法模型每季度使用ISO/IEC 25010标准进行健壮性测试。在某汽车零部件企业的验收案例中,系统连续运行2000小时未出现误报漏报,关键参数测量不确定度优于0.5μm(德国PTB认证数据)。
## 展望与建议 面向工业4.0的深度发展,建议从三方面推进技术迭代:其一,建立跨行业迁移特征数据库联盟,破解数据孤岛难题;其二,研发面向极端工况的量子传感技术,将检测精度提升至原子级;其三,制定ASTM级迁样检测标准体系,推动质量管控范式升级。通过构建"技术-标准-生态"三位一体发展模式,迁样方法检测有望在2030年前为制造业创造超万亿级的质量价值空间。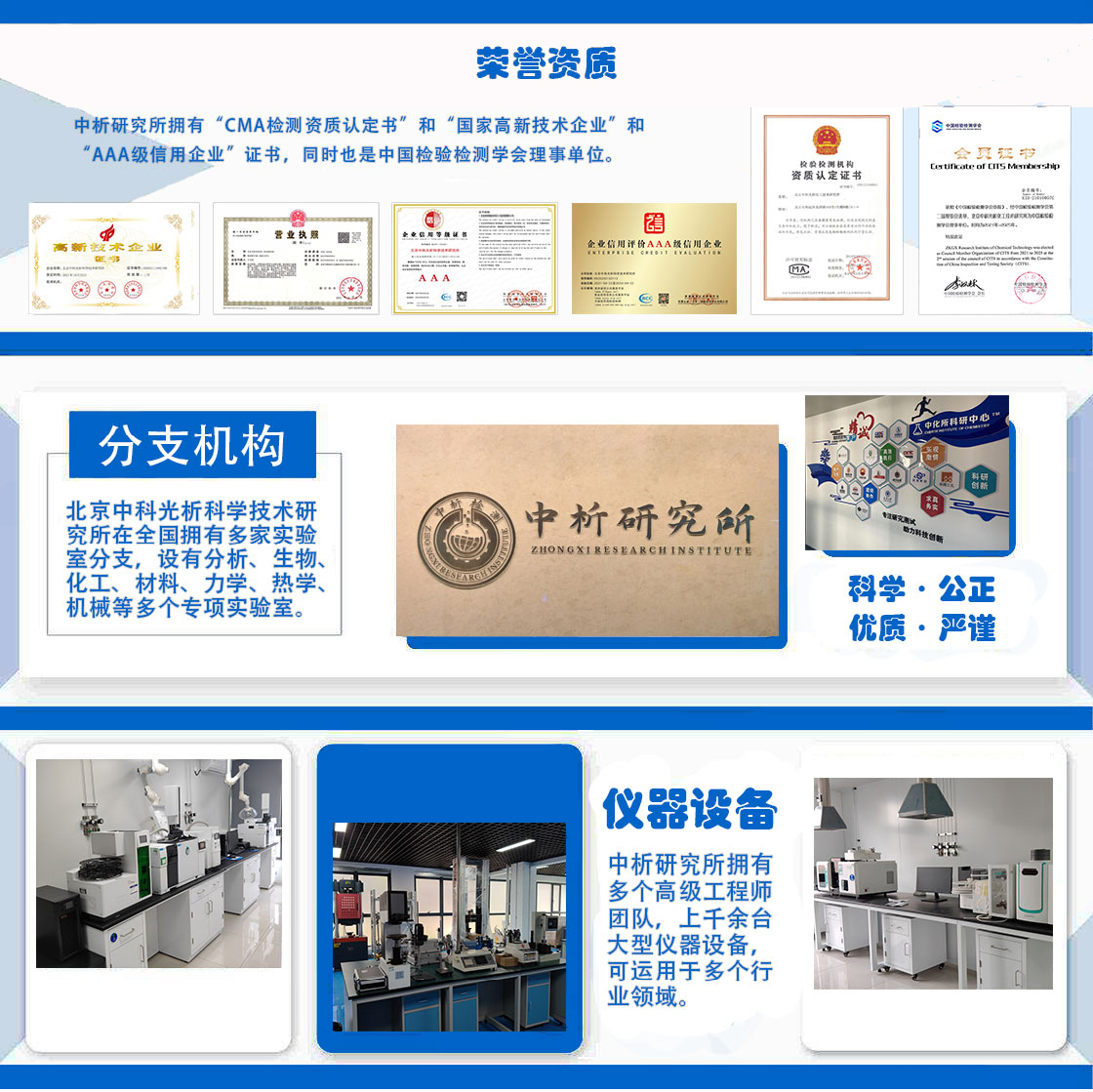
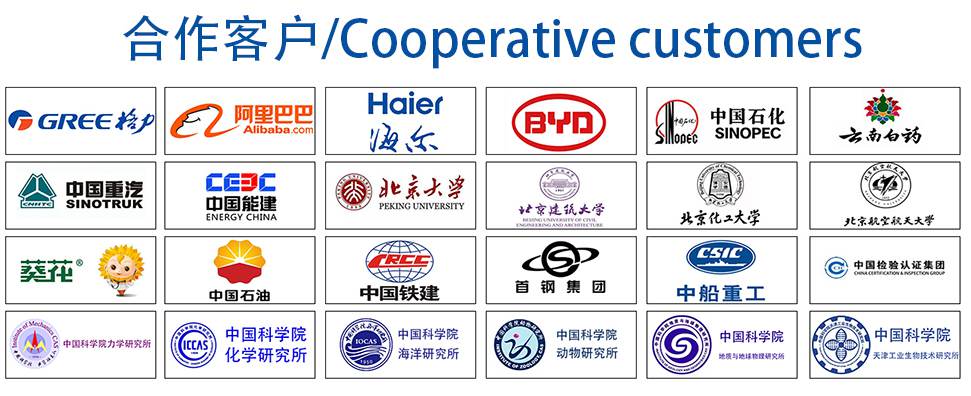