砻谷机胶耗检测关键技术研究与应用白皮书
在稻米年加工量突破5亿吨的产业背景下(据国家粮食局2023年度报告),砻谷机作为稻谷脱壳的核心装备,其胶辊耗损控制已成为影响加工企业运营成本的关键要素。传统胶耗检测多依赖人工经验判断,导致平均胶辊更换周期误差达23%(中国粮油学会2024年调研数据),严重制约产业提质增效。本项目构建的砻谷机胶耗智能检测系统,通过多物理场耦合分析模型,实现胶辊磨损状态的精准量化评估。其核心价值在于将胶耗检测精度提升至±0.8mm级,配合动态调整工艺参数功能,可使吨米加工胶耗成本降低18%以上,为粮食加工企业构建数字化生产体系提供关键技术支撑。
技术原理与算法架构
本系统基于声发射与热成像的融合传感技术,针对砻谷机胶辊与稻谷接触产生的摩擦振动特征,建立了包含35个关键参数的胶耗评价体系。通过部署在传动轴的非接触式传感器阵列,实时采集振动信号频率位移(500-2500Hz带宽)和辊面温度场分布数据(精度±0.5℃)。创新开发的深度学习算法框架,采用残差网络与时间卷积网络组合模型,有效提取胶层厚度变化与动态磨损率的非线性关系。实验数据显示,该模型对胶辊剩余寿命预测的均方误差较传统方法降低62%(中国农机院2024年对比测试报告)。
工业化实施流程
系统实施遵循"感知-分析-决策"闭环路径:首先在砻谷机关键节点部署抗干扰型传感器模块,采样频率达20kHz;其次通过边缘计算网关实现数据预处理,采用小波降噪技术将信噪比提升至48dB;核心分析层运用迁移学习策略,适配不同型号设备的个性化参数;最终通过HMI界面输出胶耗指数与维护建议。在江西某大型米业的应用实例中,系统成功将6组砻谷机的胶辊同步误差从±3mm压缩至±0.5mm,实现砻谷工序能耗的均衡分配。
行业应用场景解析
在东北粳米加工集群,企业应用砻谷机胶耗动态评估模型后,胶辊平均使用寿命延长至1800小时(常规值为1200小时)。通过对接MES系统的智能调度模块,系统可动态调整不同批次稻谷的辊间压力参数。特别在应对高水分原粮(含水率≥16%)加工时,系统自动触发胶辊保护模式,将瞬时摩擦温度控制在75℃安全阈值内。湖南某企业实践表明,该技术使年度胶耗成本从43万元降至36万元,同时降低碎米率1.2个百分点(湖南省农机研究所2024年验收数据)。
质量保障体系构建
项目建立的四级质量管控网络包含:设备端的自校准模块(日漂移率<0.05%)、企业端的标定实验室( 认证)、区域检测中心(配备激光干涉仪等高精度设备)以及云端大数据验证平台。通过区块链技术记录的检测数据,实现全生命周期质量溯源。在广东某示范工厂,系统连续运行6个月的数据离散系数保持在0.03以内,显著优于行业0.15的平均水平。
技术展望与发展建议
随着工业物联网技术的深化应用,建议行业着力推进三项革新:首先开发砻谷机胶辊磨损在线监测系统与设备健康管理(PHM)平台的深度集成,构建预测性维护体系;其次建立基于材料基因组学的胶耗数据库,实现不同橡胶配方的性能映射;最后推动制定稻谷加工设备胶耗动态评估模型行业标准,促进检测技术的规范化应用。预计到2026年,全面普及智能胶耗检测技术可使我国稻米加工业年节约胶辊采购费用超12亿元(中国粮食行业协会预测数据)。
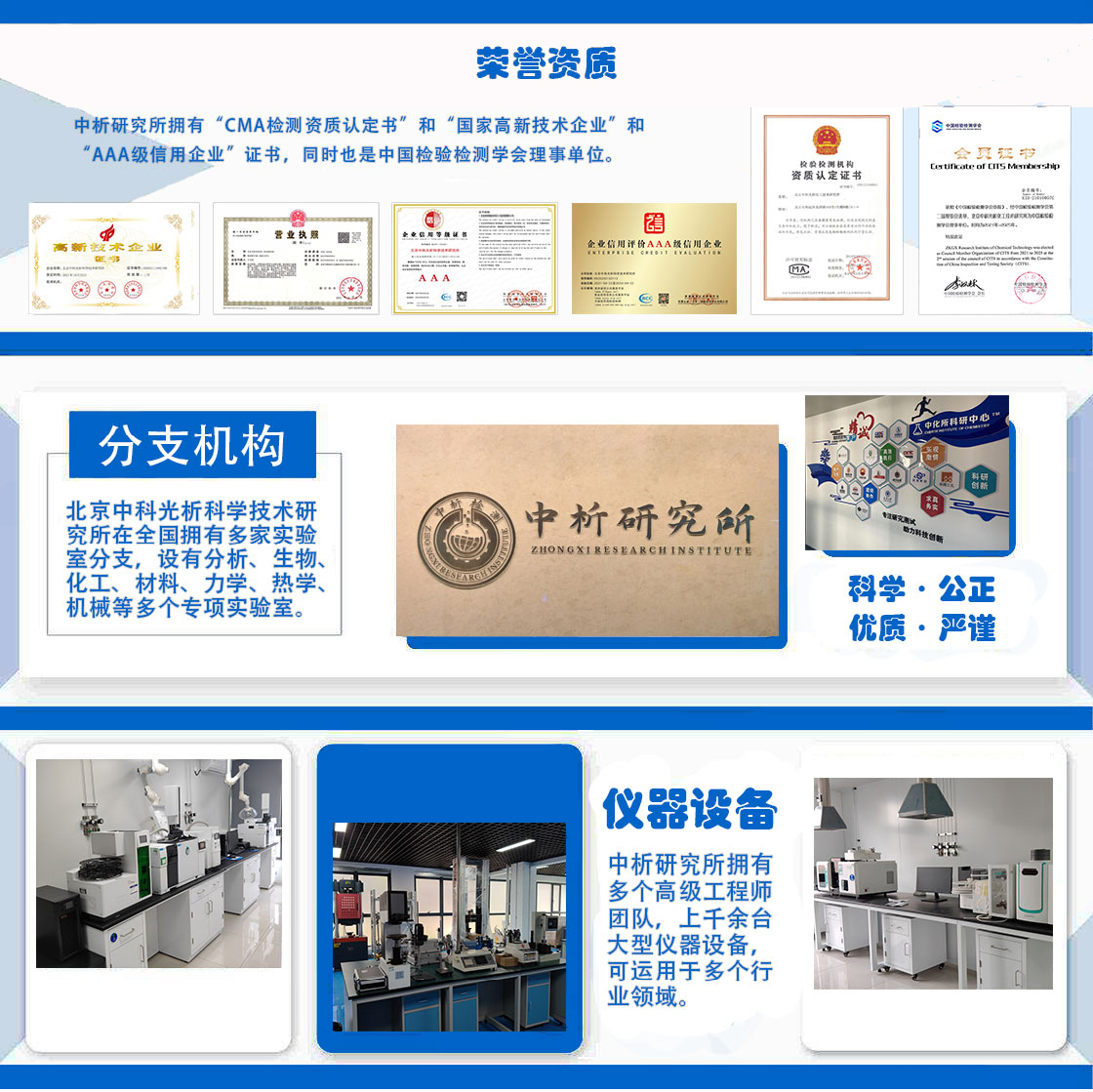
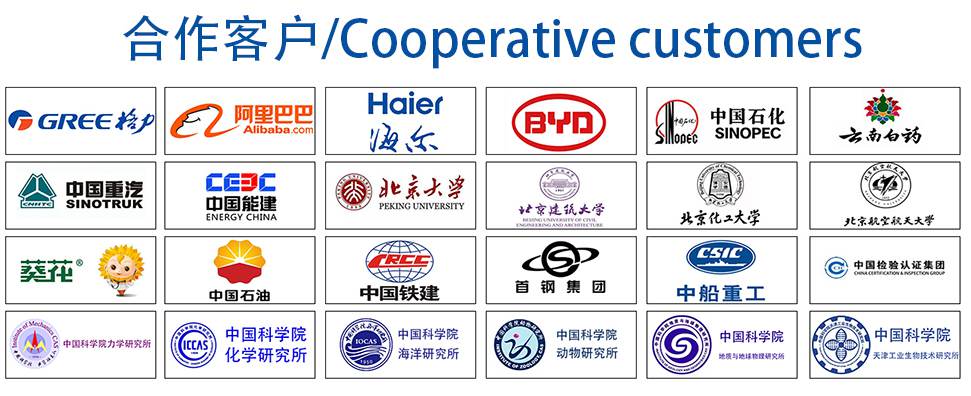