摩擦材料检测以ASTM E2515、GB 5763-2018等标准为技术框架,涵盖静摩擦系数、动摩擦系数及磨损率等核心参数。通过计算机控制的惯性测功机模拟实际工况,可获取材料在速度0-360km/h、压力0-10MPa条件下的动态特性曲线。值得关注的是,对于新能源车用制动片,需额外进行"再生制动工况模拟测试",以评估电机能量回收与传统制动协同作用下的材料性能变化。中国汽车工程研究院的对比试验表明,经系统检测优化的陶瓷基摩擦片,其热衰退率较传统材料降低42%。
### 全生命周期检测实施流程标准检测流程包含五个阶段:样品预处理(切割、研磨、表面活化)、基础性能测试(洛氏硬度、压缩强度)、工况模拟试验(温度-100℃至800℃梯度测试)、微观结构分析(SEM扫描电镜观察摩擦膜形成)及数据建模评估。在高铁制动闸片检测中,采用"制动能量-温度-磨损量"三维耦合模型,可精准预测1,500次紧急制动后的材料厚度变化,误差率控制在±0.15mm以内。该流程已在国内CRH380系列动车组维保体系成功应用。
### 行业典型应用场景解析在航空领域,波音787配套刹车片检测采用"多环境因子叠加测试法",同时模拟海拔12,000米低温(-65℃)与跑道盐雾腐蚀环境。检测数据显示,经优化后的碳陶复合材料,其湿态摩擦系数波动范围从±0.08缩减至±0.03。而风电制动器检测中,针对海上高湿度环境开发的"盐雾-振动复合试验台",可将产品质保期从3年延长至5年(据金风科技2023年技术白皮书)。
### 质量保障体系构建路径国家级检测实验室采用"三级校验体系":一级校验通过标准物质(如NIST SRM 661)完成设备基准校准;二级校验实施盲样比对,参与ILAC能力验证项目;三级校验建立区块链数据存证系统,确保检测过程可追溯。某龙头企业实践表明,该体系使检测报告国际互认率提升至92%,产品出口认证周期缩短30个工作日。
## 未来发展建议 面对智能网联装备对摩擦材料提出的新需求,建议重点突破三方面:一是建立"材料-部件-系统"级联检测标准;二是开发基于机器视觉的磨损面智能分析系统;三是构建涵盖热带、寒带等极端气候的检测数据库。同时,行业协会应牵头制定《智能制动系统摩擦材料检测规程》,推动检测技术从被动验证向主动预防转型,为下一代交通装备发展奠定质量基石。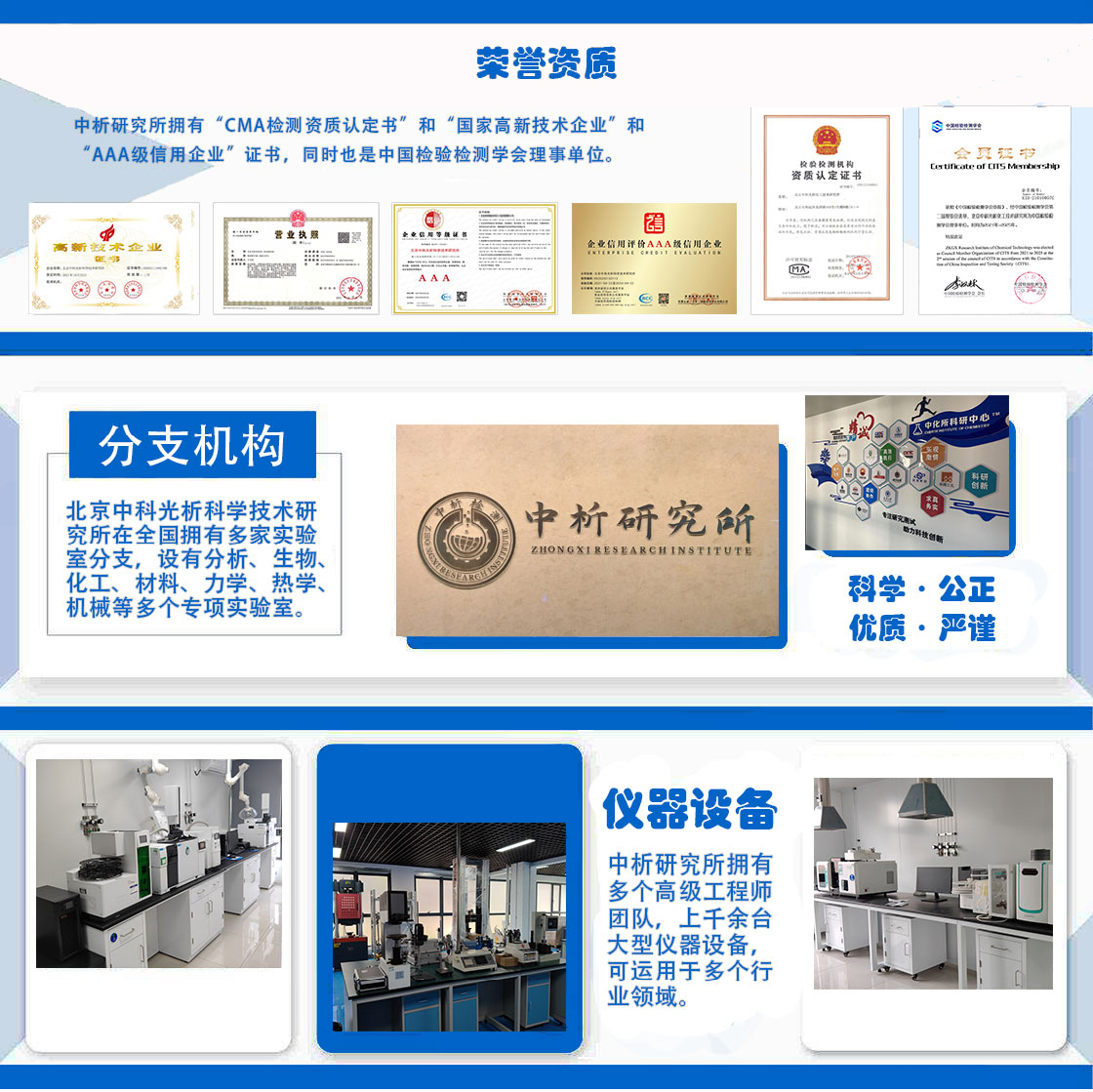
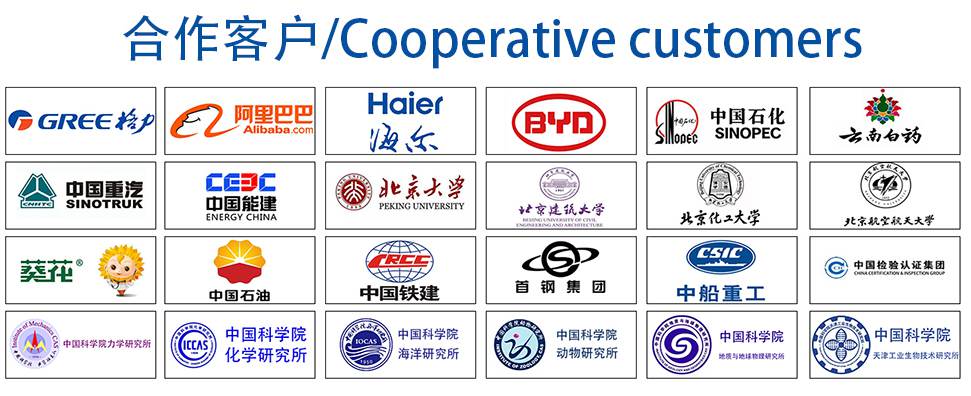