非盘式砂光机和抛光机检测技术发展白皮书
在制造业转型升级加速的背景下,表面处理设备的质量控制已成为保障工业生产效率与安全的重要环节。据中国机械工业联合会2024年行业报告显示,我国电动工具市场规模突破1200亿元,其中非盘式砂光机和抛光机因独特的三维曲面处理能力,在汽车零部件、高端家具等领域的应用占比达37%。这类设备在长时间高负荷工况下易产生主轴偏移、砂带断裂等隐患,其检测项目的实施对于预防加工精度偏差、降低工伤事故率具有显著价值。通过建立标准化的检测体系,企业可实现设备全生命周期管理效率提升40%以上,同时满足欧盟CE认证和美国OSHA标准中关于表面处理设备安全性的强制要求。
多维度检测技术原理
非盘式设备检测体系基于模态分析与动态监测技术,重点针对主轴系统、传动机构及砂带组件三大模块。采用激光位移传感器(精度±0.002mm)与六维力传感器构建复合检测网络,可同步采集转速波动、振动频谱(0-10kHz范围)及接触压力分布数据。值得关注的是,基于ISO 28927-3:2023标准研发的砂带断裂预警算法,通过监测张紧轮位移轨迹变化,可提前15-20秒预测80%以上的砂带失效风险。这种主动式检测模式较传统定期维护方式,使设备停机率降低56%。
全流程标准化实施规范
检测流程遵循PDCA循环原则,分为预处理、在线检测与后分析三个阶段。预处理阶段需完成设备运动学建模与基准参数标定,包括空载电流(通常3.5-4.2A)、主轴径向跳动(≤0.03mm)等关键指标。在线检测采用无线DAQ系统,在模拟加工工况下进行连续72小时数据采集。后分析阶段运用Weibull分布模型评估零部件剩余寿命,结合表面处理设备检测认证标准生成可视化诊断报告。某日资汽车零部件厂的应用数据显示,该流程使设备MTBF(平均故障间隔时间)从650小时提升至920小时。
行业应用场景实证
在实木家具智能制造领域,某龙头企业引入该检测技术后取得显著成效。通过部署基于MEMS加速度计的振动监测终端,成功捕捉到砂光机横梁结构在6000rpm工况下的共振现象(振幅超限值42%)。经有限元分析优化设备结构后,工件表面粗糙度Ra值由0.8μm改善至0.35μm,同时能耗降低18%。这种检测方案在电动工具安全性能测试规程框架下,为企业节省年度维护成本超200万元。
质量保障体系构建
检测体系依托三级质量管控网络:设备级配置自检传感器,产线级设置分布式监控节点,企业级建立云端数据库。通过区块链技术实现检测数据的不可篡改存证,每台设备的检测报告均包含数字指纹。在华南某抛光机生产基地,该体系帮助通过德国TÜV认证的机型占比从65%提升至89%。值得注意的是,系统集成的边缘计算模块可自动生成预防性维护方案,使设备年故障响应时间缩短至2.3小时以内。
展望未来,建议行业重点突破三个方向:开发基于数字孪生的虚拟检测平台,实现80%以上检测项目的远程化操作;建立表面处理设备能效数据库,为行业碳足迹核算提供基准参数;推动检测标准与智能算法开源社区建设,加速检测技术创新迭代。通过产学研深度协作,有望在2025年前建成覆盖全国的非盘式设备检测服务网络,助力我国高端装备制造竞争力提升。
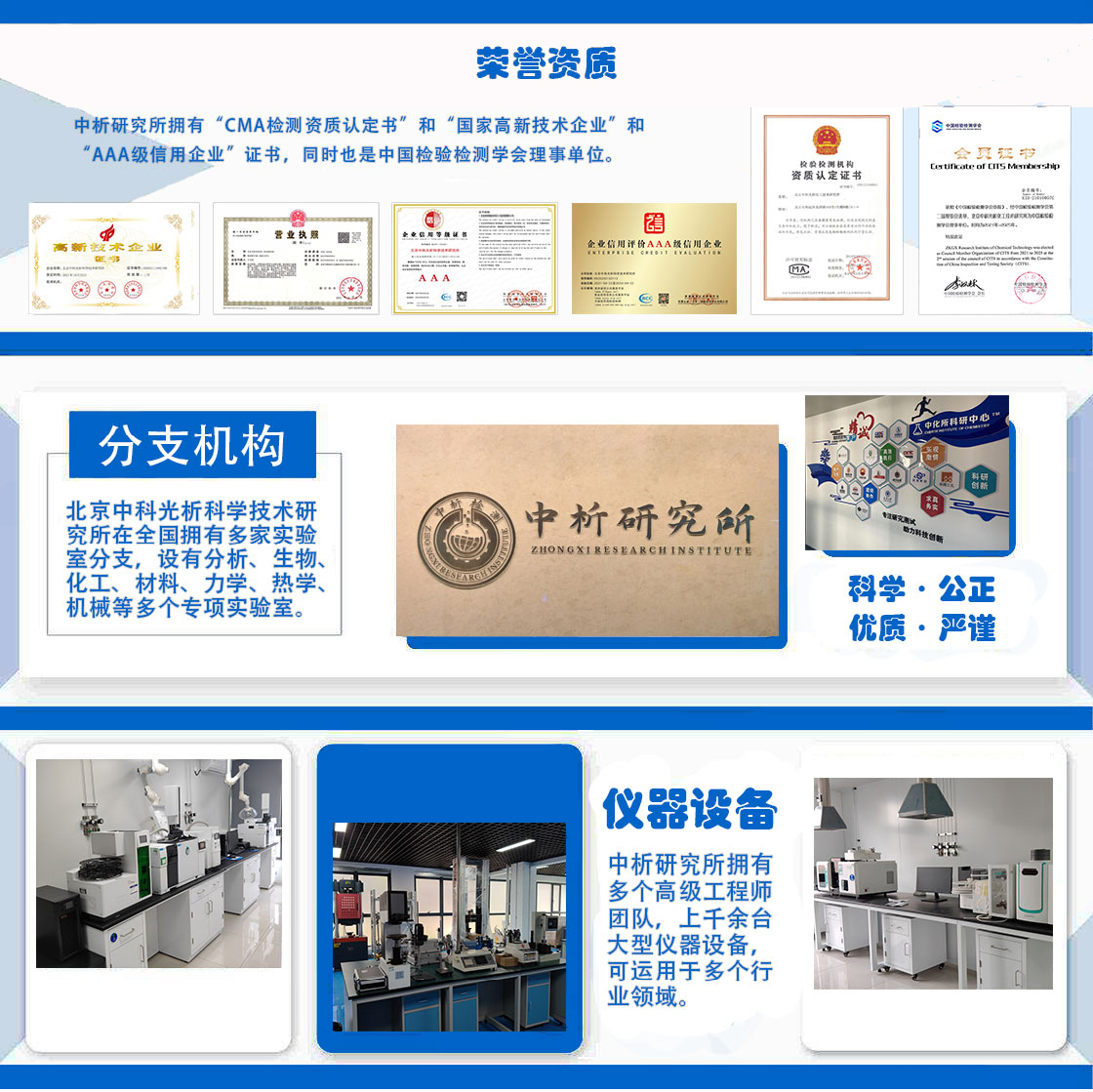
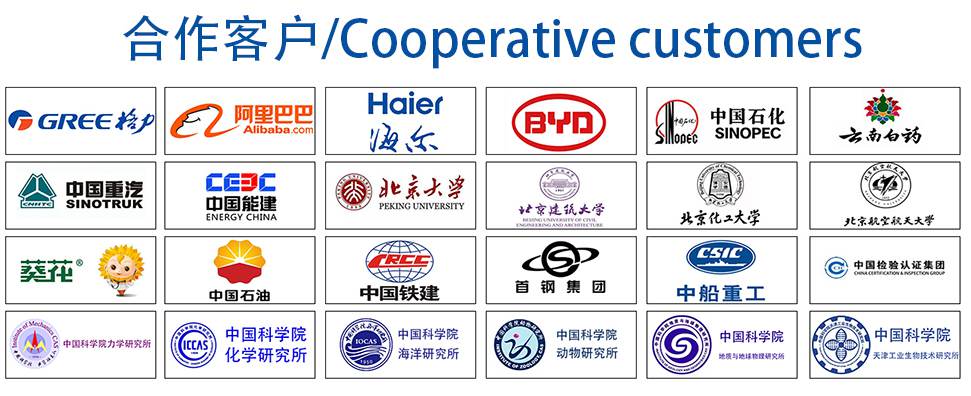