电站弯管检测项目及技术解析
一、外观检查
- 检测目的 发现表面裂纹、机械损伤、腐蚀坑、氧化层剥落等直观缺陷。
- 方法与工具
- 目视检查:使用强光手电、放大镜(10~20倍)观察表面状态。
- 内窥镜检查:对无法直接观察的弯管内壁,采用柔性工业内窥镜(如Olympus IPLEX NX)检测焊缝及弯折区域。
- 表面清洁度评估:执行GB/T 8923标准,清除油污、锈迹后判定清洁等级(Sa2.5以上为合格)。
二、尺寸与几何公差检测
- 关键参数
- 弯曲半径偏差(±5%设计值)
- 椭圆度(≤3%公称直径)
- 角度偏差(±1°)
- 检测技术
- 激光三维扫描:采用HandySCAN 3D等设备生成点云模型,对比设计图纸分析形变。
- 模板比对法:对大口径弯管(DN>300mm)使用定制弧度模板检测弯曲轮廓。
- 壁厚分布测量:使用超声波测厚仪(如Olympus 38DL),按TSG D7006标准在弯管外拱、内拱及中性面抽检12个点位。
三、无损检测(NDT)
-
- 应用场景:检测内部裂纹、夹渣及壁厚减薄。
- 探头选择:双晶聚焦探头(5MHz)用于内壁缺陷,相控阵探头(PAUT)用于复杂几何区域扫描。
- 验收标准:按DL/T 820-2021,裂纹类缺陷不允许存在,气孔直径≤1.5mm。
-
- 技术要点:采用Ir-192或Se-75源,配合CR成像板(如Dürr HD-CR 35 NDT)对焊缝进行全景成像。
- 缺陷评级:参照NB/T 47013.2-2015,II级及以上为合格。
-
- 工艺参数:湿法荧光磁粉(A1-30/100),磁化电流DC 1200A,提升力≥177N。
- 缺陷显示:线性缺陷长度>3mm需记录,密集气孔区域判定为不合格。
四、材料性能分析
-
- 使用手持式XRF光谱仪(如Niton XL3t)快速筛查Cr、Mo、Ni等合金元素含量,偏差超过GB/T 5310规定值的±10%需复检。
-
- 取样要求:在弯管直段切取拉伸试样(GB/T 228.1)、冲击试样(GB/T 229)。
- 性能指标:高温段弯管需测定400℃下的屈服强度,降幅不得超过室温值的15%。
-
- 制备截面试样,观察是否存在σ相析出、晶间腐蚀等劣化现象(参照DL/T 884标准)。
五、耐压与残余应力测试
-
- 试验压力:1.5倍设计压力(ASME B31.1规定),保压时间≥30分钟,无渗漏、无宏观变形。
-
- 采用X射线衍射法(如Proto iXRD)测量弯管外表面应力,冷弯管件残余应力值应<60%材料屈服强度。
六、腐蚀状态评估
- 壁厚腐蚀速率计算
- 根据历年检测数据,按ASME B31G公式计算剩余寿命。
- 点蚀深度测量
- 使用深度规或3D轮廓仪,最大点蚀深度超过壁厚40%需降级使用。
七、特殊工况附加检测
- 蠕变损伤检测:对运行超过10万小时的高温弯管(>450℃),采用复膜金相法评估蠕变孔洞等级(按EN 10319标准)。
- 振动疲劳监测:安装应变片监测振幅,防止共振引起的疲劳裂纹(频率避开50±5Hz范围)。
检测周期规划
参数 | 常规检测周期 | 超期服役检测周期 |
---|---|---|
壁厚测量 | 2年 | 6个月 |
超声波检测 | 4年 | 1年 |
金相分析 | 8年 | 2年 |
转成精致网页
上一篇:多能互补及能源微网系统检测下一篇:水轮机检测
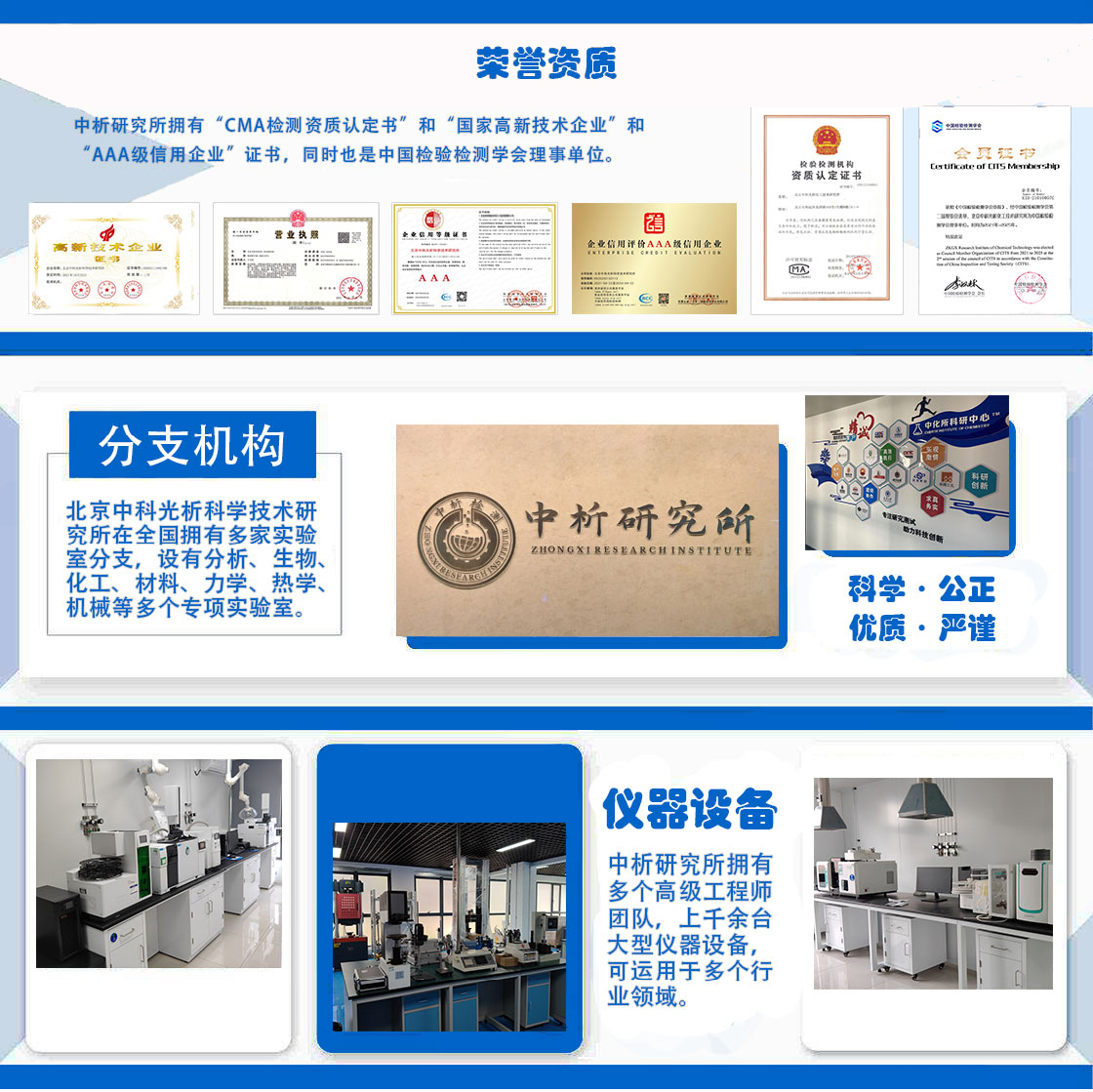
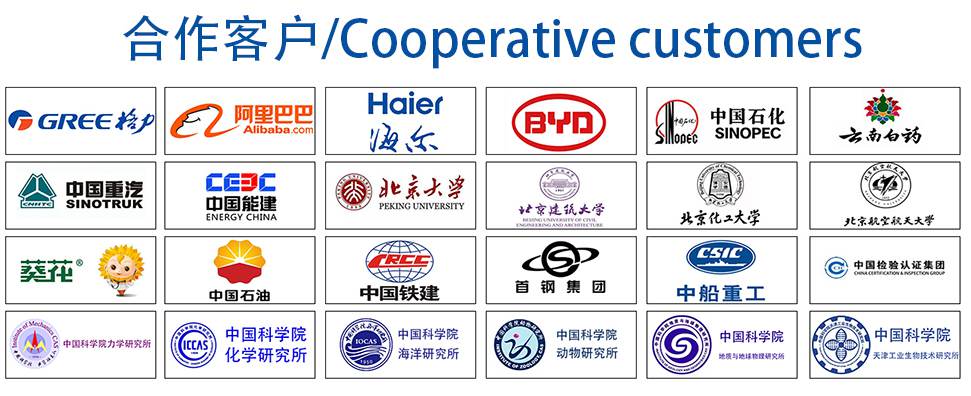
材料实验室
热门检测
17
15
21
23
28
25
22
20
18
14
17
23
21
22
22
17
17
16
23
22
推荐检测
联系电话
400-635-0567