整车尺寸检测:汽车制造工艺中的关键质量关卡
在现代化汽车制造体系中,整车尺寸检测作为核心质量控制环节,贯穿于产品研发、生产制造及出厂检验全流程。这项系统化检测工程通过精确测量车辆长宽高、轮距轴距、关键零部件配合间隙等200余项参数,确保每辆汽车不仅符合设计规范,更能满足安全行驶、操控稳定和外观协调的要求。在智能化工厂中,该检测项目的误差控制精度已达到±0.5mm级别,为汽车品质筑起坚实的技术防线。
核心检测项目体系
1. 外廓尺寸测量
采用激光跟踪仪与三维摄影测量系统,精确获取车辆总长、总宽、总高等基础参数。重点监测前后悬长度匹配度,确保符合国家机动车外廓尺寸限值标准(GB1589-2016),误差控制在±2mm范围内。
2. 轴距轮距检测
运用非接触式轮距测量仪配合电子水平仪,测量前后轴中心距与左右轮间距。该数据直接影响车辆转向性能和高速稳定性,对于四驱车型还需检测传动系统对称度。
3. 车身轮廓扫描
通过移动式三维激光扫描装置,建立整车数字孪生模型。重点验证车门、引擎盖等开闭件与车身的匹配度,检测区域包括:
- 车门与门框间隙(标准值3.5±0.5mm)
- 引擎盖与前大灯接缝平顺度
- 尾门与后保险杠对齐度
4. 底盘架构检测
使用高精度全站仪检测悬挂安装点定位,确保前后悬架几何参数符合设计值。关键指标包括:
- 主销后倾角(Caster)公差±0.5°
- 车轮外倾角(Camber)公差±0.3°
- 前束角(Toe)公差±0.2°
智能检测技术演进
随着工业4.0技术应用,整车尺寸检测已进入智能化阶段:
1. 机器视觉系统实现360°自动测量,检测效率提升300%
2. 在线测量(In-line Metrology)技术实现白车身尺寸100%全检
3. 大数据平台实时分析测量数据,自动生成SPC过程控制图表
4. AR辅助检测系统提供可视化指导,降低人工判读误差
在新能源汽车快速发展的背景下,整车尺寸检测更需关注电池舱密封性、电机安装定位等新增项目。通过构建全流程数字化检测体系,汽车制造商正将尺寸合格率从传统98%提升至99.98%水平,为消费者打造真正"毫米不差"的精致座驾。
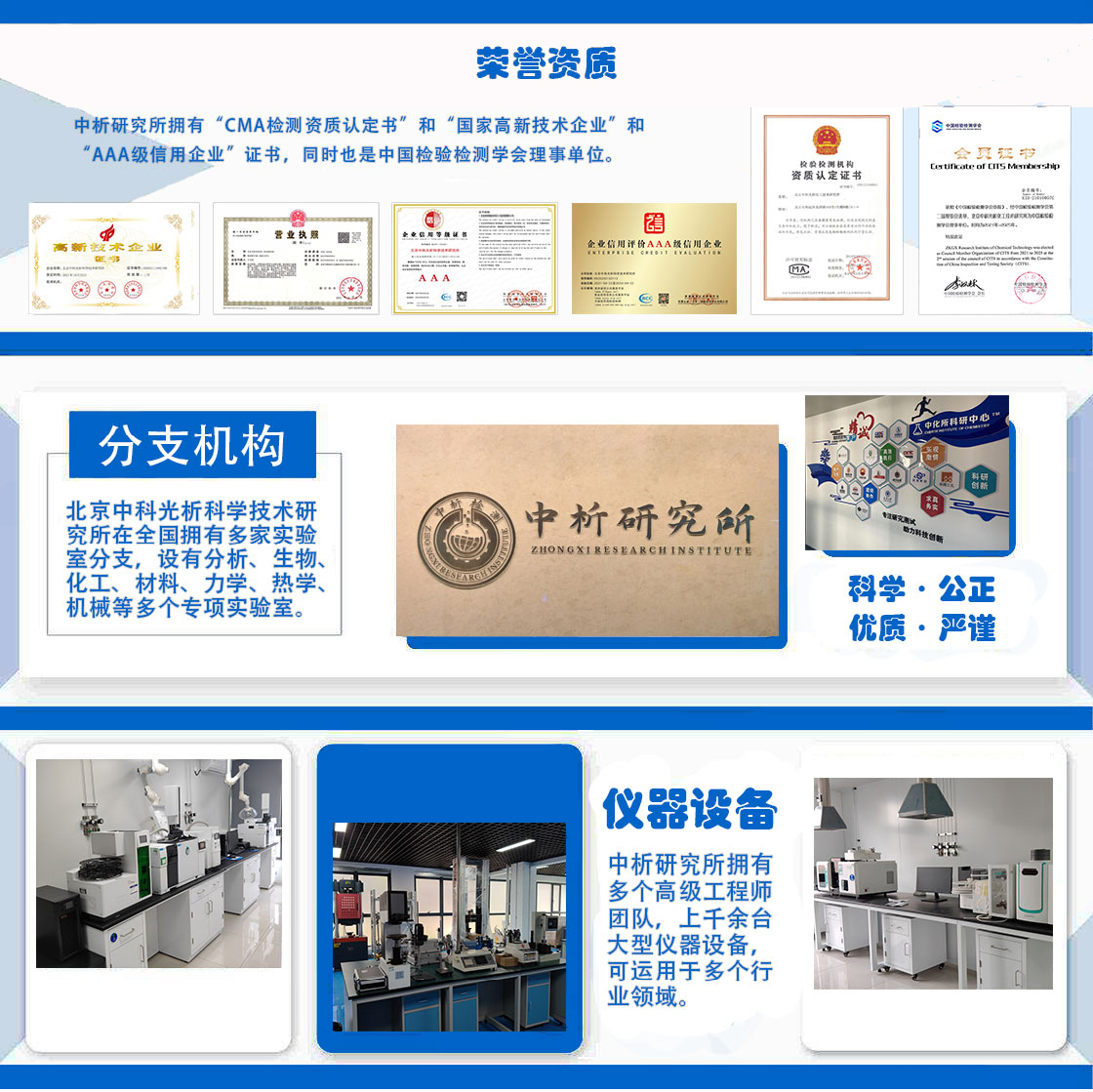
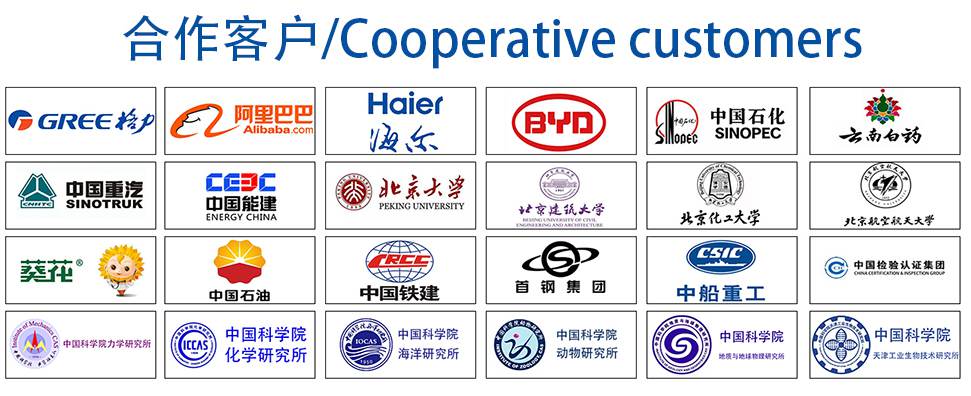