动力电池组检测:守护安全与性能的核心防线
在新能源汽车、储能系统及便携式电子设备快速发展的今天,电池组作为能量存储与释放的核心单元,其安全性、可靠性和使用寿命直接影响着终端产品的市场竞争力。根据国家市场监管总局2023年发布的《动力电池行业质量白皮书》,电池组整体故障中72%源于检测环节的疏漏。专业的电池组检测体系不仅包括常规性能验证,更需要覆盖全生命周期风险预警,通过系统性测试项目构建多维度的质量防线。
核心检测项目体系
完整的电池组检测体系包含五大关键模块:
1. 电气性能测试
采用高精度电池测试系统(BTS)进行充放电特性分析,重点检测项目包括: - 容量保持率(循环100次后容量衰减≤8%) - 直流内阻(DCR)分布均匀性(单体差异≤15%) - 能量转换效率(≥94% @1C充放电) - 开路电压(OCV)一致性(模组内≤20mV) - 自放电率(7天自放电≤3%)
2. 安全性能验证
依据GB 38031-2020标准执行多重安全测试: - 过充/过放保护(150%SOC条件下触发保护) - 短路耐受(瞬时电流≥3kA不燃爆) - 热失控扩散(单体温升600℃不引发连锁反应) - 机械冲击(30g加速度冲击后绝缘≥100MΩ) - 挤压测试(300kN压力下保持结构完整)
3. 环境适应性检测
通过三综合试验箱模拟极端工况: - 温度循环(-40℃~85℃ 100次循环容量衰减≤5%) - 湿热老化(85℃/85%RH 500小时无电解液泄漏) - 低气压测试(11.6kPa维持2小时外壳无变形) - 盐雾腐蚀(5%NaCl溶液喷雾96小时接触电阻变化≤10%)
4. 结构完整性分析
运用CT扫描与有限元分析技术: - 模组焊接强度(拉伸力≥200N/mm²) - 电芯膨胀力监测(100%SOC下膨胀率≤3%) - 抗震性能(10Hz~200Hz随机振动后连接器阻抗≤5mΩ) - 密封性验证(IP67防护等级保持1米水深30分钟)
5. 寿命预测与失效分析
结合大数据建模与实测试验: - 加速老化测试(55℃ 1C循环2000次容量≥80%) - EIS阻抗谱分析(10mHz~10kHz频段特性解析) - 热成像监控(温差梯度≤5℃/模组) - 析锂阈值检测(快充倍率≥3C时析锂风险预警)
随着ISO 19453:2023等新标准的实施,电池组检测正在向智能化、在线化方向发展。通过集成BMS数据与实验室检测结果,构建数字孪生模型,可实现早期故障诊断与剩余寿命预测,推动电池组质量管控进入精准化时代。
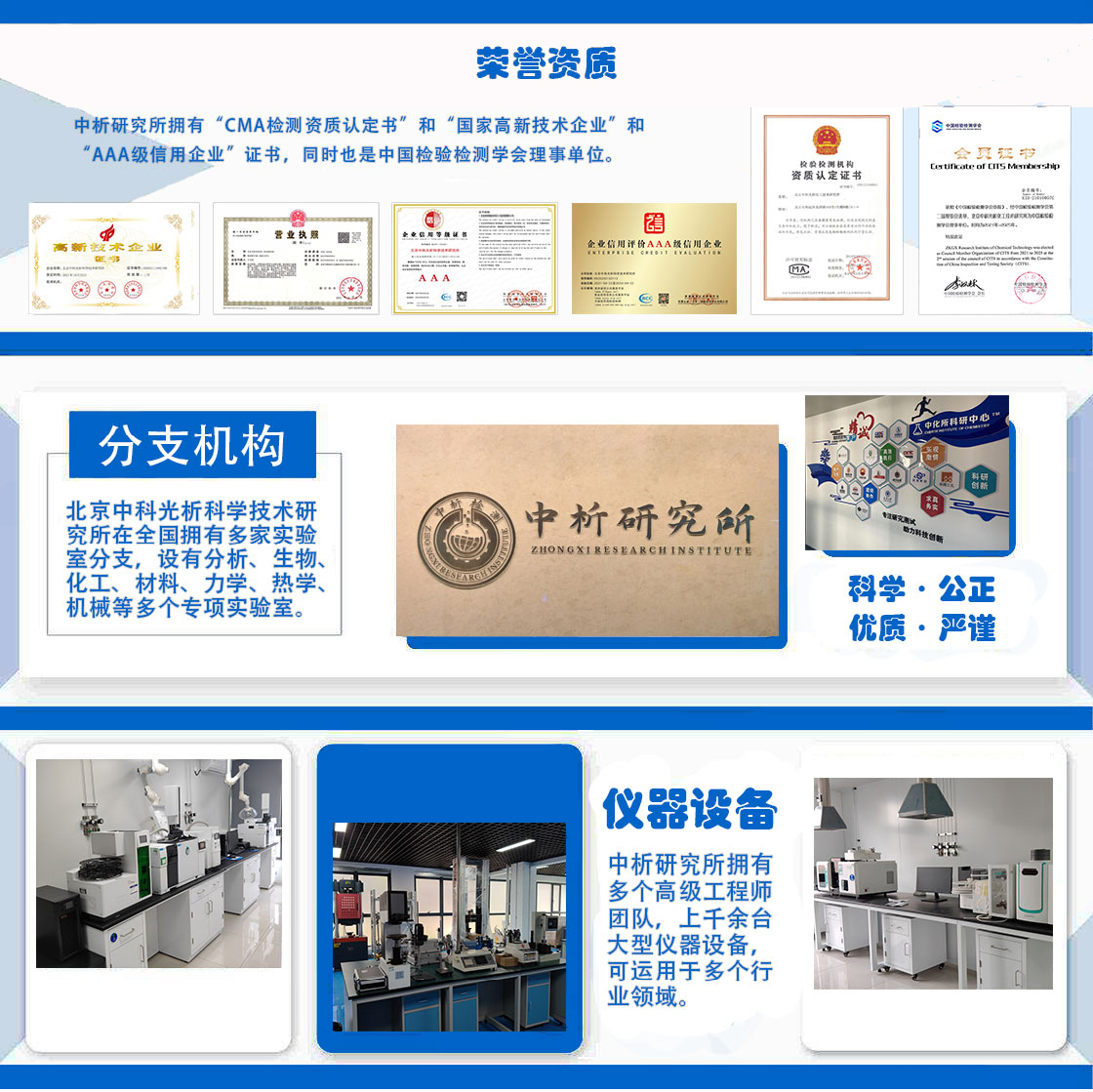
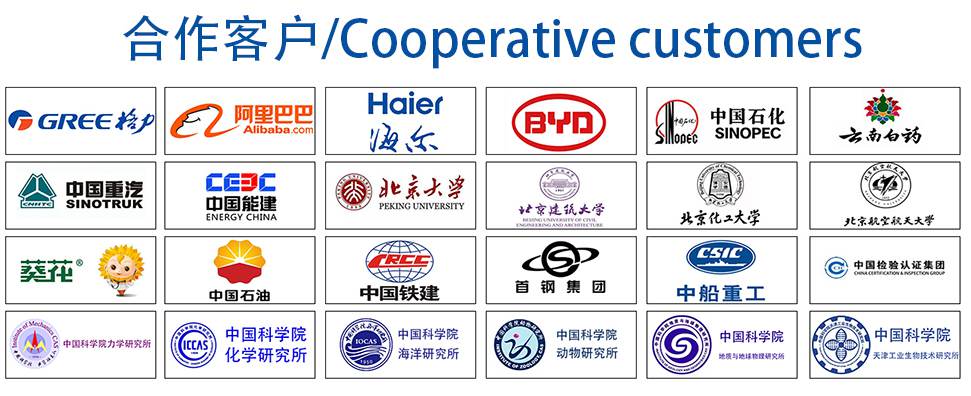