液压油污染度检测的重要性
液压系统作为工业设备的核心动力传输单元,其稳定性和寿命与液压油的清洁度密切相关。液压油污染是导致设备故障的常见原因之一,污染物包括固体颗粒、水分、空气以及化学降解产物等。这些污染物会加速液压元件磨损、堵塞精密阀芯、降低系统效率,甚至引发突发性停机事故。定期开展液压油污染度检测,不仅能评估油液状态,还能通过数据指导维护策略,延长设备使用寿命,降低运维成本。国际标准如ISO 4406和NAS 1638为污染度分级提供了科学依据,而现代检测技术则通过多种手段全面解析油液健康状况。
液压油污染度检测的核心项目
1. 固体颗粒污染分析
通过自动颗粒计数器(APC)或显微镜法,检测油液中不同尺寸颗粒的浓度。重点监测>4μm、>6μm和>14μm的颗粒数量,依据ISO 4406标准计算污染度等级(如18/16/13),判断是否超出设备允许的阈值。
2. 水分含量检测
使用卡尔费休库仑法、红外光谱法或离心分离法,定量分析油液中游离水和溶解水的含量。水分超标会导致油液氧化、添加剂失效及金属部件锈蚀,一般要求水分含量低于0.1%(体积百分比)。
3. 黏度与氧化程度评估
通过旋转黏度计测量油液黏度变化,判断是否因高温氧化或污染物混入导致性能劣化。同时结合红外光谱(FTIR)检测氧化产物(如羰基峰),评估油液老化程度。
4. 酸值与碱值测定
采用电位滴定法检测油液总酸值(TAN)和碱值(TBN)。酸值升高表明氧化反应加剧,可能腐蚀金属元件;碱值下降则反映添加剂消耗,需及时补充或更换油液。
5. 微生物污染检测
在潮湿环境中,液压油可能滋生细菌或真菌。通过培养法或ATP生物荧光技术检测微生物含量,防止生物膜堵塞滤芯或产生酸性代谢物。
检测方法与技术应用
现代液压油污染度检测普遍采用在线监测与实验室分析结合的模式。便携式颗粒计数器可实现现场快速筛查,而实验室级仪器(如激光粒度分析仪、气质联用仪)则用于深度诊断污染来源。部分企业引入物联网传感器,实时传输油液数据至云端平台,结合AI算法预测污染趋势,实现预防性维护。
污染控制与预防措施
根据检测结果,可针对性采取以下措施:①更换高精度滤芯;②使用真空脱水装置去除水分;③添加抗氧化剂或消泡剂;④优化油箱密封与呼吸系统;⑤控制工作温度在40-60℃范围内;⑥规范油液储存条件(避光、防潮)。建议每500工作小时或设备大修后执行系统化检测,建立污染度数据库以跟踪长期变化。
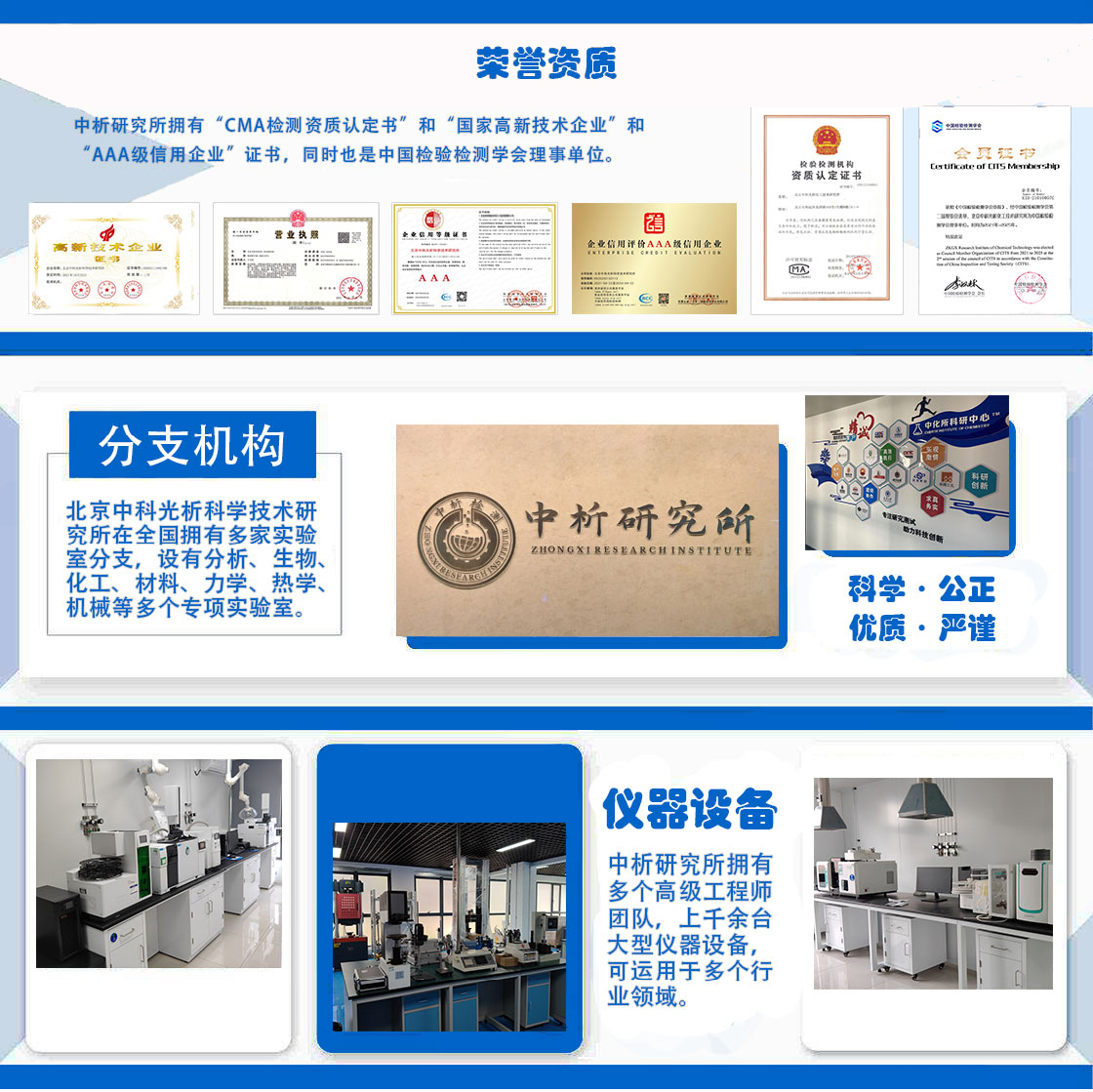
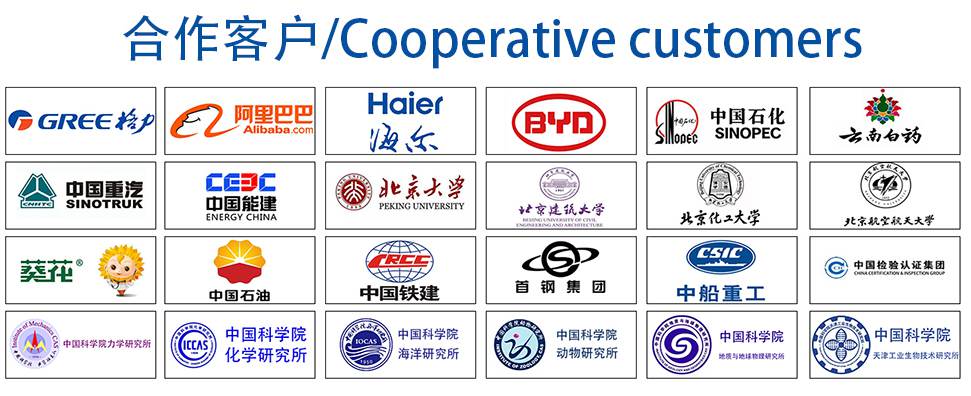