撑开式金属密封阀门检测项目与技术要点
撑开式金属密封阀门作为一种广泛应用于石油化工、核电、航空航天等高压高温场景的关键设备,其密封性能与结构可靠性直接关系到系统运行安全。该类型阀门通过金属接触面的弹性形变实现密封,具有耐腐蚀、耐磨损、长寿命等优势,但同时也对制造工艺和检测精度提出了更高要求。为确保阀门在复杂工况下的稳定运行,需从材料性能、密封结构、动态特性等多维度进行全面检测。
一、核心检测项目
1. 密封性能检测:采用氦气检漏法或液压试验法,分别在常温与极限温度下验证阀门静态密封性,泄漏率需满足API 598或GB/T 13927标准要求。对于DN200以上大口径阀门,需增加动态密封测试以模拟实际工况下的流体冲击效应。
2. 结构强度检测:通过水压强度试验验证阀体、阀盖等承压部件的耐压能力,试验压力为公称压力的1.5倍,保压时间不少于5分钟,确保无塑性变形或渗漏现象。
3. 金属材料分析:采用光谱分析仪检测阀座、阀瓣材料成分,结合金相显微镜观察晶粒度及热处理效果,确认材料符合ASTM A182 F6a等高温合金标准。
二、关键功能性测试
1. 启闭力矩测试:使用扭矩传感器记录阀门全开/全闭过程中的操作扭矩曲线,重点分析撑开机构在低温(-196℃)或高温(650℃)条件下的机械性能衰减情况。
2. 循环寿命试验:模拟实际工况进行5000次以上开闭循环测试,后期通过三维形貌仪检测密封面的磨损深度,磨损量不超过原始厚度的10%为合格。
3. 抗冲击振动测试:参照MIL-STD-810G标准开展多轴振动试验,验证阀门在运输及运行过程中对随机振动、机械冲击的耐受能力。
三、智能化检测技术应用
随着工业物联网技术的发展,现代检测体系已引入数字孪生模型与声发射监测技术。通过建立阀门的有限元仿真模型,可预测不同压力梯度下的应力分布;而声发射传感器可实时捕捉微泄漏产生的弹性波信号,实现早期故障预警。部分高端检测系统还配备红外热成像模块,能够可视化显示密封面的温度场分布特征。
完整的检测流程需遵循ASME B16.34、ISO 15848-1等国际标准,并结合实际工况制定个性化测试方案。建议每3年开展一次全面检测,在极端环境或连续运行工况下应缩短检测周期至12个月,通过预防性维护保障阀门全生命周期的可靠运行。
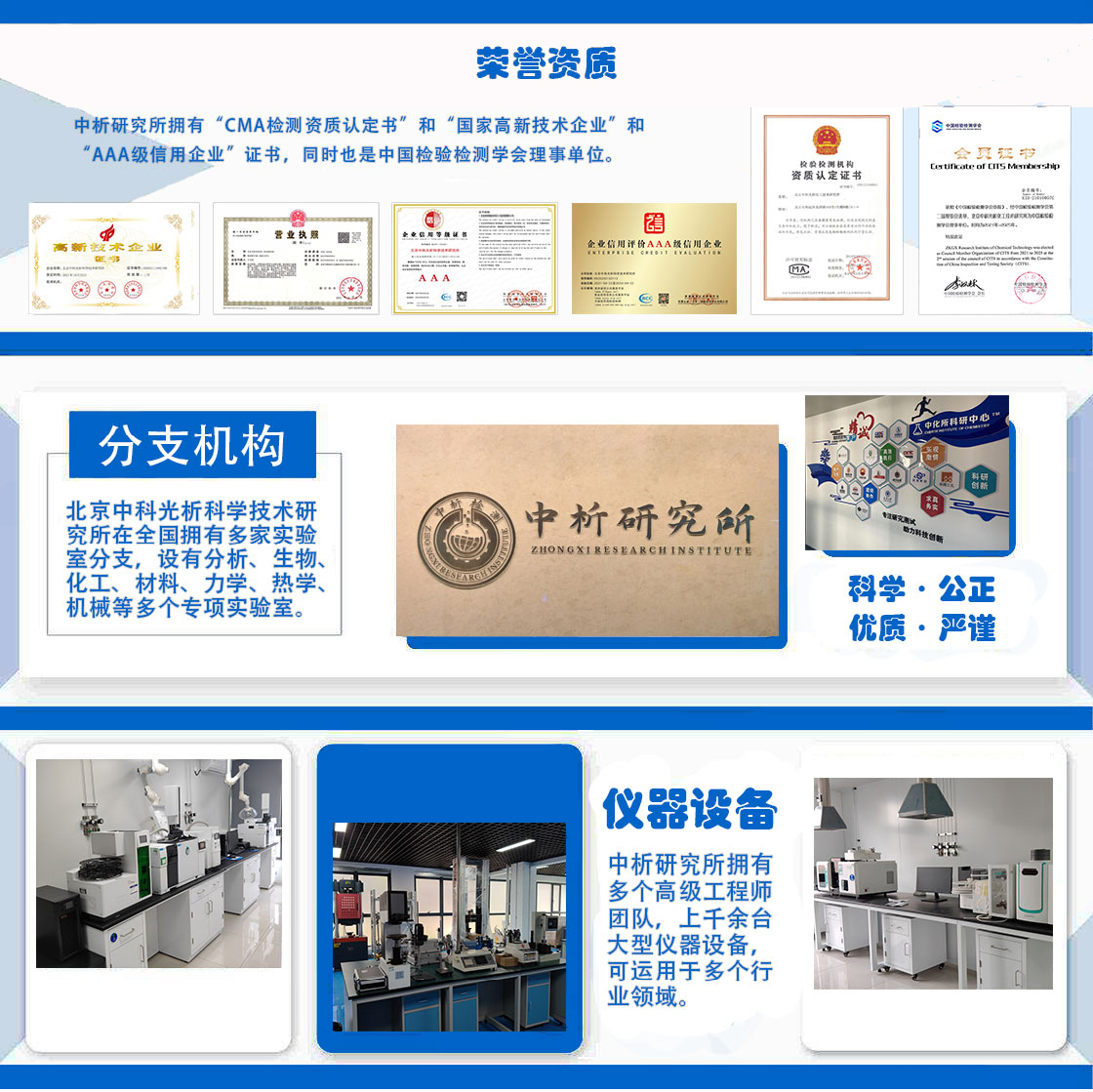
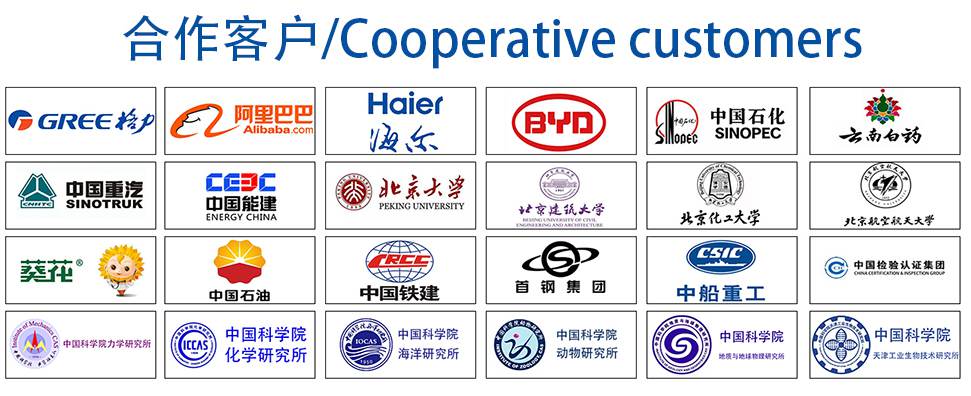