多功能水泵控制阀检测的重要性与应用场景
多功能水泵控制阀作为供水系统、消防工程及工业循环水系统的核心组件,承担着流量调节、压力稳定、防回流和缓闭消能等关键功能。随着智能化控制技术的发展,其结构复杂性显著提升,涵盖机械传动、电子传感和自动化控制等多技术领域。定期开展专业检测能够确保阀门运行的可靠性,避免因密封失效、响应延迟或控制异常导致的系统故障,同时降低能耗并延长设备使用寿命。目前行业内普遍依据GB/T 13927《工业阀门压力试验》、CJ/T 167《多功能水泵控制阀》等标准进行系统性检测。
核心检测项目分类与实施要点
功能性检测
通过模拟实际工况进行启闭动作测试,记录阀门从全开到全闭的时间响应曲线,要求启闭时间偏差不超过标称值的±10%。采用精密流量计检测不同开度下的流量调节精度,重点关注小流量工况下的控制稳定性。背压防护测试需在1.25倍额定压力下持续30分钟,观察是否有渗漏或结构变形。
性能参数检测
使用高精度压力传感器测量阀体承压部位的应力分布,评估最大工作压力下的结构完整性。流量-压降特性曲线测试需覆盖10%-100%流量范围,绘制特性曲线并与设计参数对比。水力损失检测需在额定流量下测量进出口压差,确保能量损耗符合JB/T 5296标准要求。
密封性检测
采用气压和液媒双重检测法,分别进行0.6MPa气密性测试和1.5倍工作压力的水压试验。重点检测阀座密封面、阀杆填料函等关键部位,使用内窥镜观察密封面磨损情况。API 598标准的泄漏率检测要求每分钟气泡数不超过规定阈值。
材料与结构检测
对阀体、阀瓣等承压部件进行金属材料成分分析,验证是否符合ASTM A216标准。使用超声波测厚仪测量关键部位壁厚,对比设计图纸允许公差。焊接部位需进行X射线探伤,检测未熔合、气孔等缺陷,符合ASME B16.34规范要求。
智能控制检测
对电动执行器的控制精度进行闭环测试,验证4-20mA信号反馈的线性度。模拟电网波动(±10%电压变化)测试控制模块的稳定性。通过Modbus、Profibus等通信协议测试数据传输完整性,确保远程监控系统的可靠性。
环境适应性检测
在环境试验箱中进行-20℃~80℃温度循环测试,验证密封材料的耐温性能。湿度测试需在95%RH环境下持续48小时,检测电子元件的防护等级。振动测试模拟ISO 10816-3标准的III类振动环境,评估机械结构的抗振性能。
检测结果分析与改进建议
检测数据应形成完整的QCD(质量-成本-交付)分析报告,对不达标项进行FTA故障树分析。建议建立检测数据库,通过大数据分析预测阀门寿命周期。对于频繁出现的密封失效问题,可推荐采用PTFE+石墨复合密封结构改进方案。
通过系统化的检测流程,可降低30%以上的非计划停机风险,延长阀门使用寿命2-3倍。建议用户单位建立定期检测机制,优先选择具有CMA/ 资质的专业检测机构,确保检测数据的法律效力与工程参考价值。
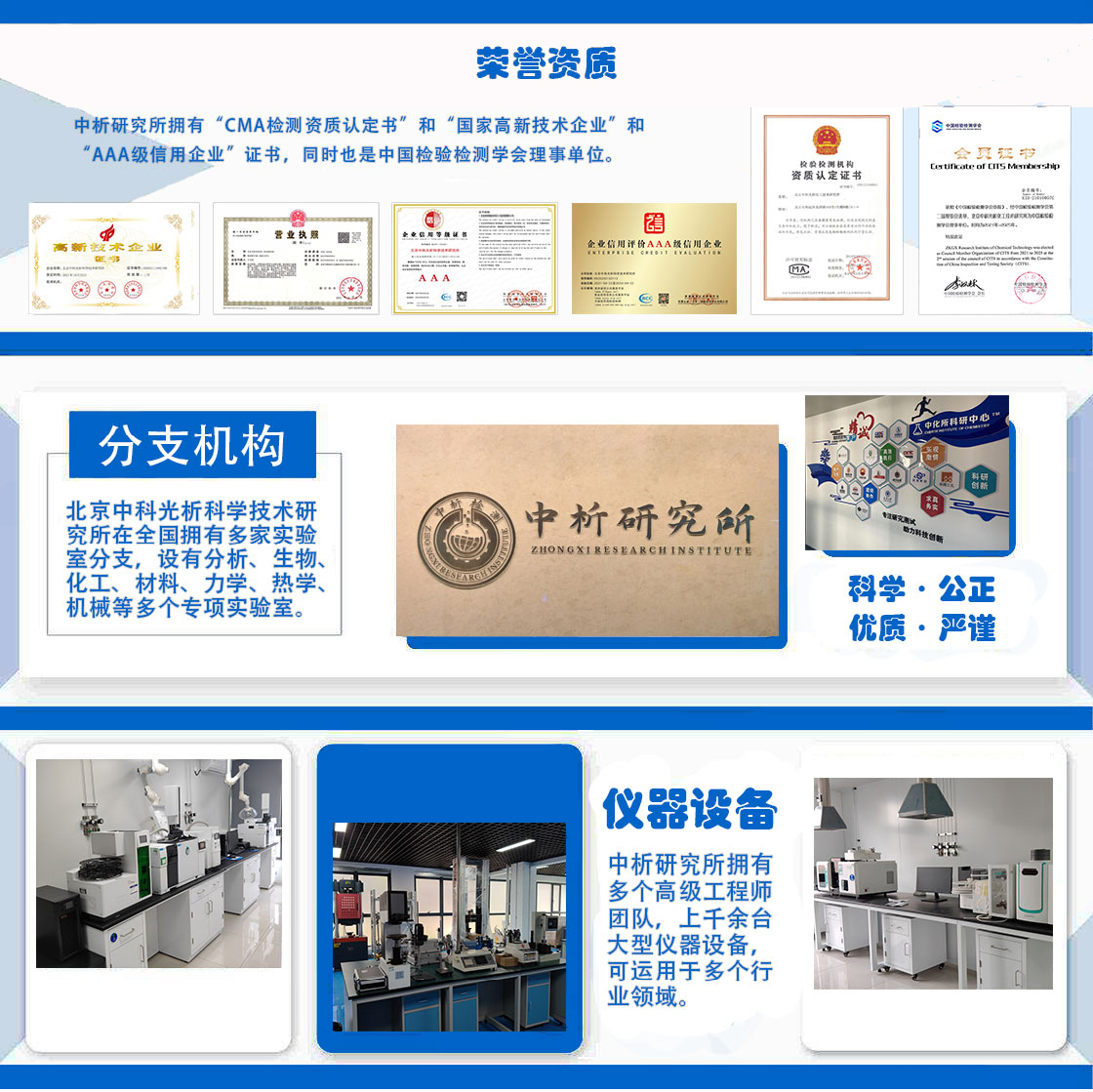
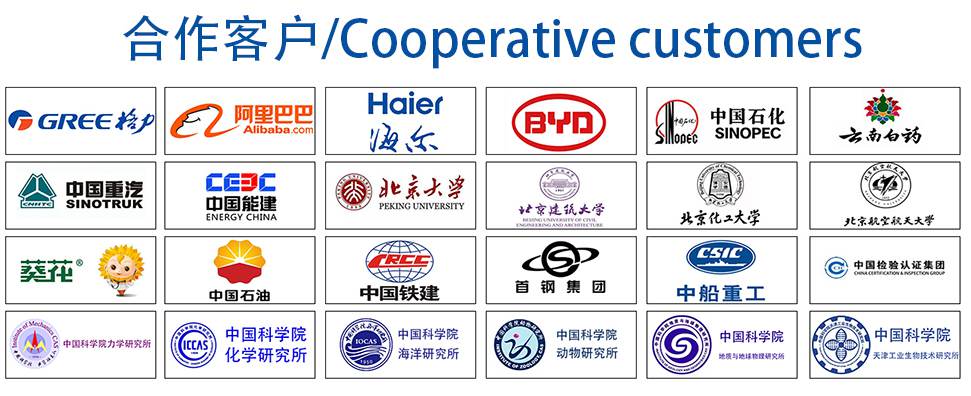