双转子反击式破碎机检测项目及技术要点
双转子反击式破碎机作为矿山、建材、冶金等领域的关键破碎设备,凭借其双转子联动结构实现了高效率的中细碎作业。由于长期承受高冲击载荷和物料磨损,其核心部件易出现疲劳损伤和性能劣化。定期开展系统性检测是保障设备稳定运行、预防突发故障及延长使用寿命的核心手段。本文将针对双转子反击式破碎机的核心检测项目展开详细解析。
1. 转子系统专项检测
对上下双转子进行360°可视化检查,测量转子轴的同轴度(偏差需≤0.2mm/m)与径向跳动(≤1.5mm)。使用超声波测厚仪检测锤盘厚度衰减率(警戒值为初始厚度15%),锤头磨损量超过25%或出现贯穿裂纹时应强制更换。需在额定转速下进行动平衡测试,残留不平衡量应控制在G6.3等级以内。
2. 反击板与衬板磨损评估
采用三维扫描仪建立衬板三维模型,与原始CAD数据进行对比分析,厚度磨损超过40%或出现50mm以上裂纹需更换。调整板锤与反击板间隙至10-15mm基准范围,使用塞尺多点检测间隙均匀性,确保出料粒度控制在设定值±5mm偏差带。
3. 传动系统精密诊断
使用振动分析仪采集轴承座三维振动值(建议报警阈值:速度4.5mm/s,加速度10g),频谱分析重点监测齿轮啮合频率及其倍频成分。采用红外热像仪监测减速箱温升(温升≤45℃),齿轮油铁谱分析显示磨粒浓度>100ppm时需换油。皮带传动系统应检查张紧力(挠度值控制在1.6%跨距)和V带同步磨损情况。
4. 壳体结构完整性检测
使用磁粉探伤法检测焊接区域裂纹,壳体变形量超过5mm/m需进行矫正。采用负压检测法验证密封性能,在风机全开状态下,破碎腔负压值应稳定在-200Pa至-500Pa区间。重点检查观察门密封条压缩量(≥原始厚度30%)和锁紧装置可靠性。
5. 电气控制系统测试
模拟测试过载保护响应时间(应≤0.5秒),校验电流互感器精度(1级精度允许误差±1%)。使用PLC诊断软件检查程序逻辑,验证转速同步控制偏差(≤2%额定转速)。对温度传感器进行三点校准(0℃、80℃、150℃),确保测温误差≤±1.5%FS。
6. 整机性能综合测试
空载运行2小时后检测轴承温升(≤35℃),负载试验时监测功率波动(≤额定功率10%)。采用激光粒度分析仪检测出料产品,要求P80值达到工艺要求且超粒率<5%。同步记录吨能耗指标(kWh/t),对比设计值偏差应控制在8%以内。
通过建立包含300+检测点的标准化检测体系,可精准预判双转子反击式破碎机的健康状态。建议每800运行小时进行常规检测,大修周期不超过12000小时,结合状态监测数据实现预测性维护,将设备故障率降低60%以上,显著提升生产系统的综合效益。
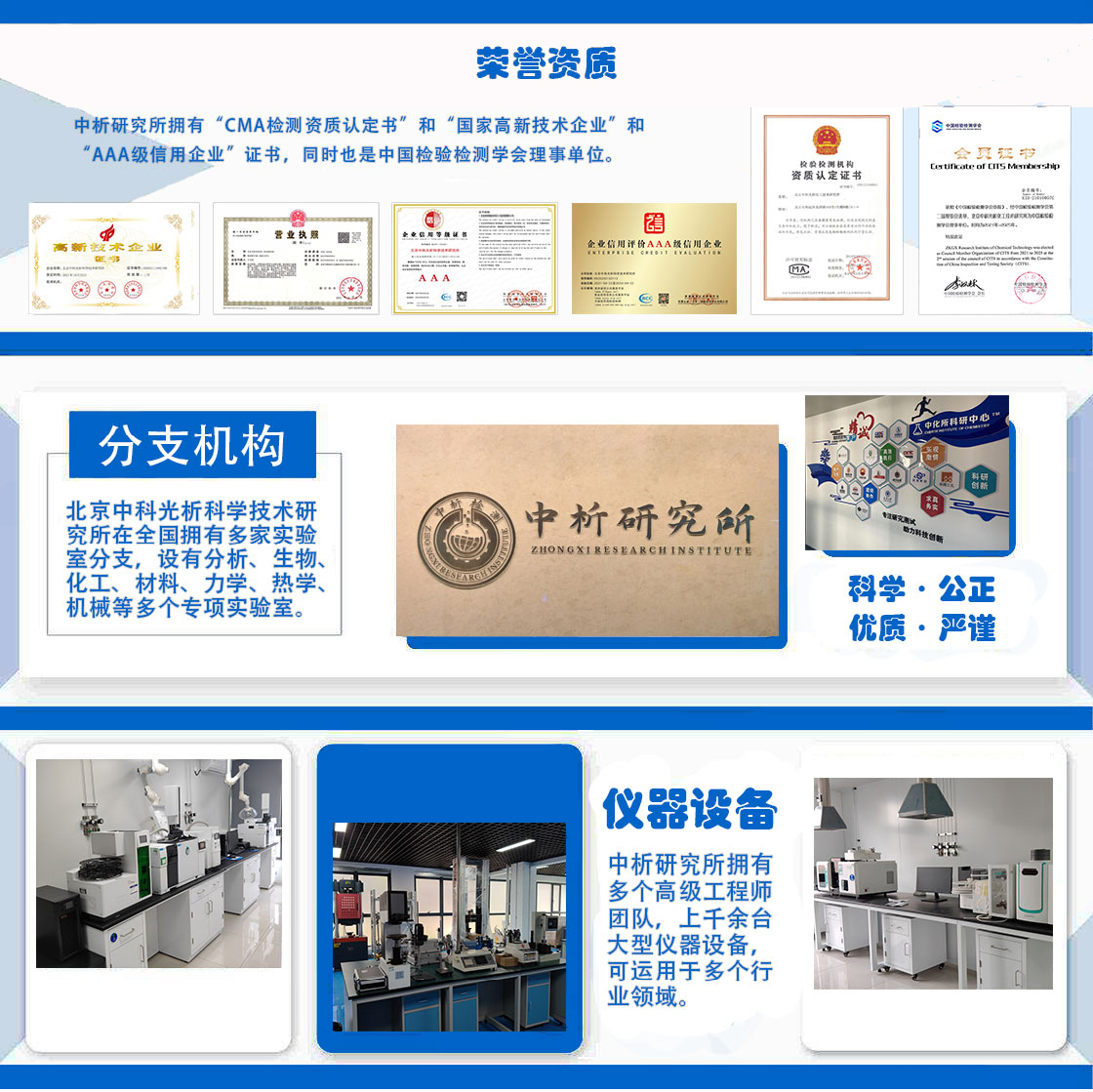
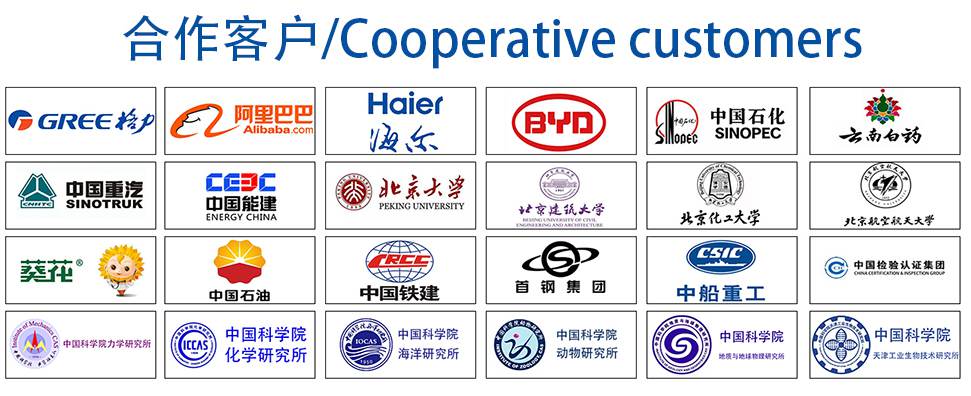