冶金用石灰石检测的重要性与技术要求
在冶金工业中,石灰石作为重要的辅助原料,广泛应用于炼钢、炼铁等工艺中,主要发挥助熔剂、脱硫剂和造渣剂的作用。其质量直接关系到金属冶炼效率、炉渣流动性及最终产品的品质。冶金用石灰石需具备高纯度、低杂质和稳定的物理化学性能,因此开展系统性检测是确保生产过程稳定性和产品质量的关键环节。
核心检测项目及方法
1. 化学成分分析
通过X射线荧光光谱仪(XRF)或化学滴定法测定以下指标:
- 氧化钙(CaO)含量:主成分需≥52%,决定有效利用率
- 氧化镁(MgO)含量:控制在≤3%,过高会导致炉渣黏度增加
- 二氧化硅(SiO2)含量:要求≤1.5%,过量将增大渣量
- 硫(S)、磷(P)等有害元素:需分别小于0.08%和0.02%
2. 物理性能测试
包含堆积密度(1.4-1.6g/cm³)、莫氏硬度(3-4级)及抗压强度检测,确保在高温环境下保持结构稳定性。
3. 粒度分布检测
采用激光粒度仪进行分级:
- 转炉用石灰石:10-40mm占比≥90%
- 高炉用石灰石:20-80mm占主体
- 粉末率(<5mm)需≤5%
4. 烧失量测定
通过高温煅烧(950℃±25℃)计算CO2释放量,合格品烧失量应≤43%,反映碳酸钙分解程度。
5. 杂质综合分析
包括粘土质矿物、有机质及重金属检测,采用岩相分析法结合ICP-MS,确保Al2O3<1.2%、Fe2O3<0.5%。
6. 活性度测试
模拟实际冶炼条件,在4N盐酸溶液中测定10分钟的中和反应速度,优质石灰石活性度应≥350ml。
检测标准与质量控制
检测过程需严格执行GB/T 3286.1-2012《冶金石灰》标准,结合企业冶炼工艺特点制定内控指标。重点监控批次间稳定性,对CaO波动幅度要求≤±0.8%,建立数字化检测数据库实现质量追溯。
通过上述系统性检测,可有效保证冶金用石灰石的熔剂活性、造渣效率及冶金反应动力学特性,为现代冶金工业的绿色高效生产提供基础保障。
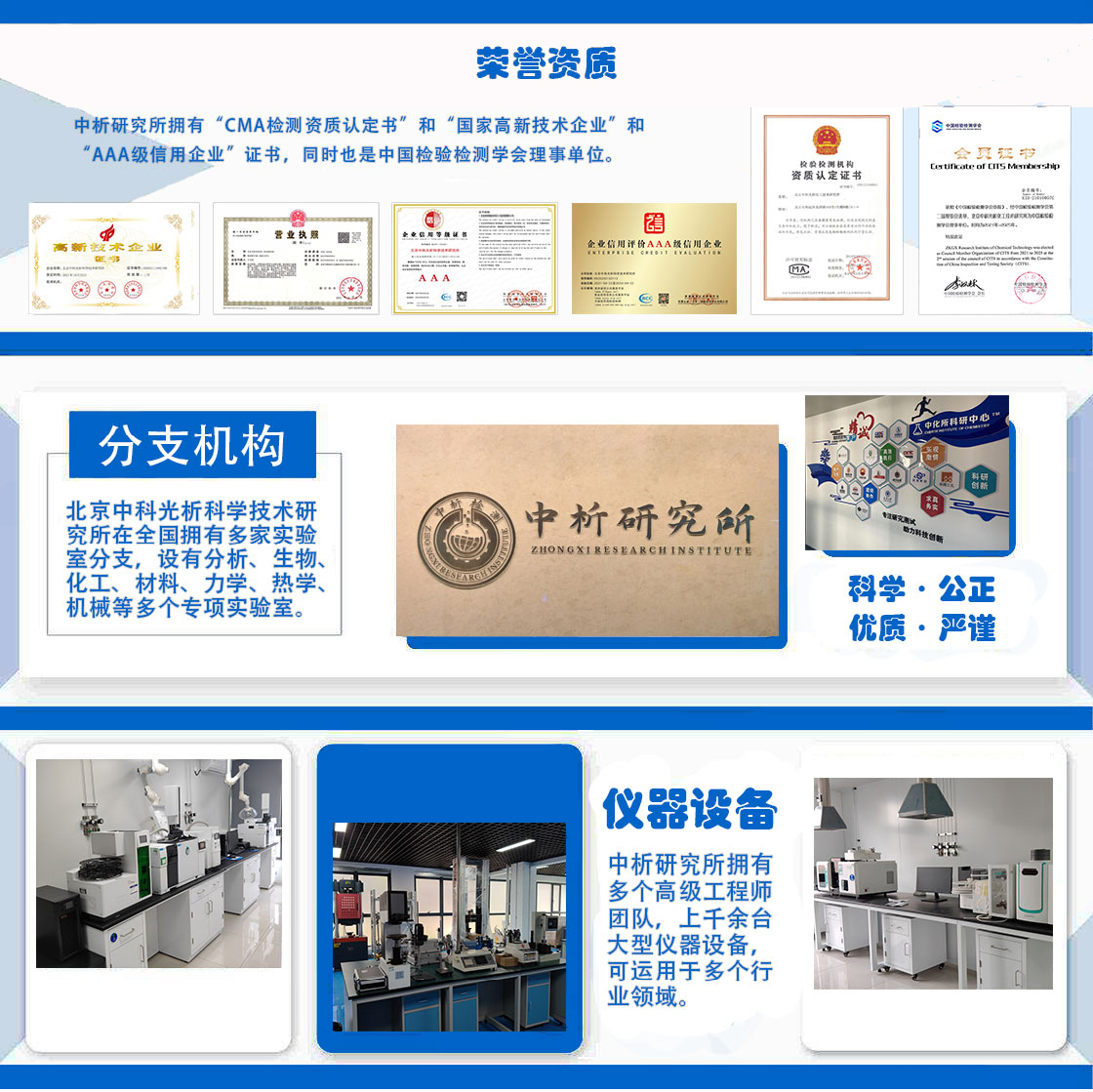
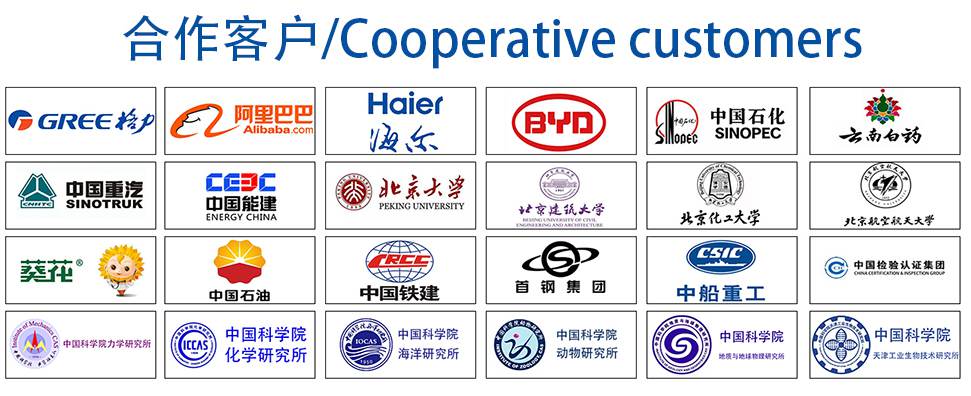