载货汽车制动器衬片检测的核心项目与重要性
载货汽车作为物流运输的核心工具,其制动系统的可靠性直接关系到行车安全和运营效率。作为制动系统关键零部件的制动器衬片,需定期进行严格的性能检测,以确保其在复杂工况下的稳定性与耐久性。检测项目主要围绕材料性能、结构完整性和实际工况模拟展开,需遵循国家强制标准GB/T 5763-2018《汽车用制动器衬片》及行业规范。
一、制动器衬片材料性能检测
1. 摩擦系数测试:通过定速式摩擦试验机测量不同温度(100℃~350℃)下的动摩擦系数,要求波动值不超过±15%
2. 磨损率检测:模拟连续制动场景,计算单位面积质量损失率(标准限值≤0.7×10⁻⁷cm³/N·m)
3. 热膨胀性测试:评估高温(300℃)状态下的厚度膨胀率(需<3%)
4. 压缩应变特性:检测不同压力下的变形量,确保制动时压力传递有效性
二、结构完整性检测项目
1. 厚度均匀性检测:使用数显千分尺多点测量,偏差需控制在±0.2mm以内
2. 表面裂纹检查:借助工业内窥镜和放大镜进行微观裂纹观察(裂纹深度<1.5mm)
3. 背板粘结强度测试:通过拉力试验机验证衬片与背板的剥离强度(≥3MPa)
4. 铆接/粘接质量检测:使用超声波探伤仪检查内部缺陷
三、动态性能验证测试
1. 惯性台架试验:模拟实际车辆载荷,进行连续20次紧急制动测试
2. 制动效能衰退率:检测高温反复制动后的性能保持能力(衰退率≤30%)
3. 涉水恢复测试:浸水后验证制动效能的恢复时间(≤5次制动内恢复)
4. 振动耐久性测试:模拟3万公里道路振动条件下的结构稳定性
四、环保与安全专项检测
1. 重金属含量分析:铅、汞、镉等有害物质检测(符合ELV指令要求)
2. 石棉成分筛查:采用XRD衍射法确保零石棉含量
3. 制动噪音测试:在消音室进行不同速度段的噪音值采集(≤75dB)
4. 粉尘排放量测定:使用颗粒物收集装置评估制动粉尘生成量
专业检测机构通常配备D-MS定速试验机、CHASE台架等设备,建议每行驶5万公里或更换新衬片时进行强制检测。检测报告应包含摩擦性能曲线、热衰退率矩阵图等关键数据,帮助运营单位准确掌握制动器衬片的实际工况适应能力。通过系统化的检测程序,可有效预防制动失效事故,延长制动系统使用寿命,保障载货汽车的安全运营。
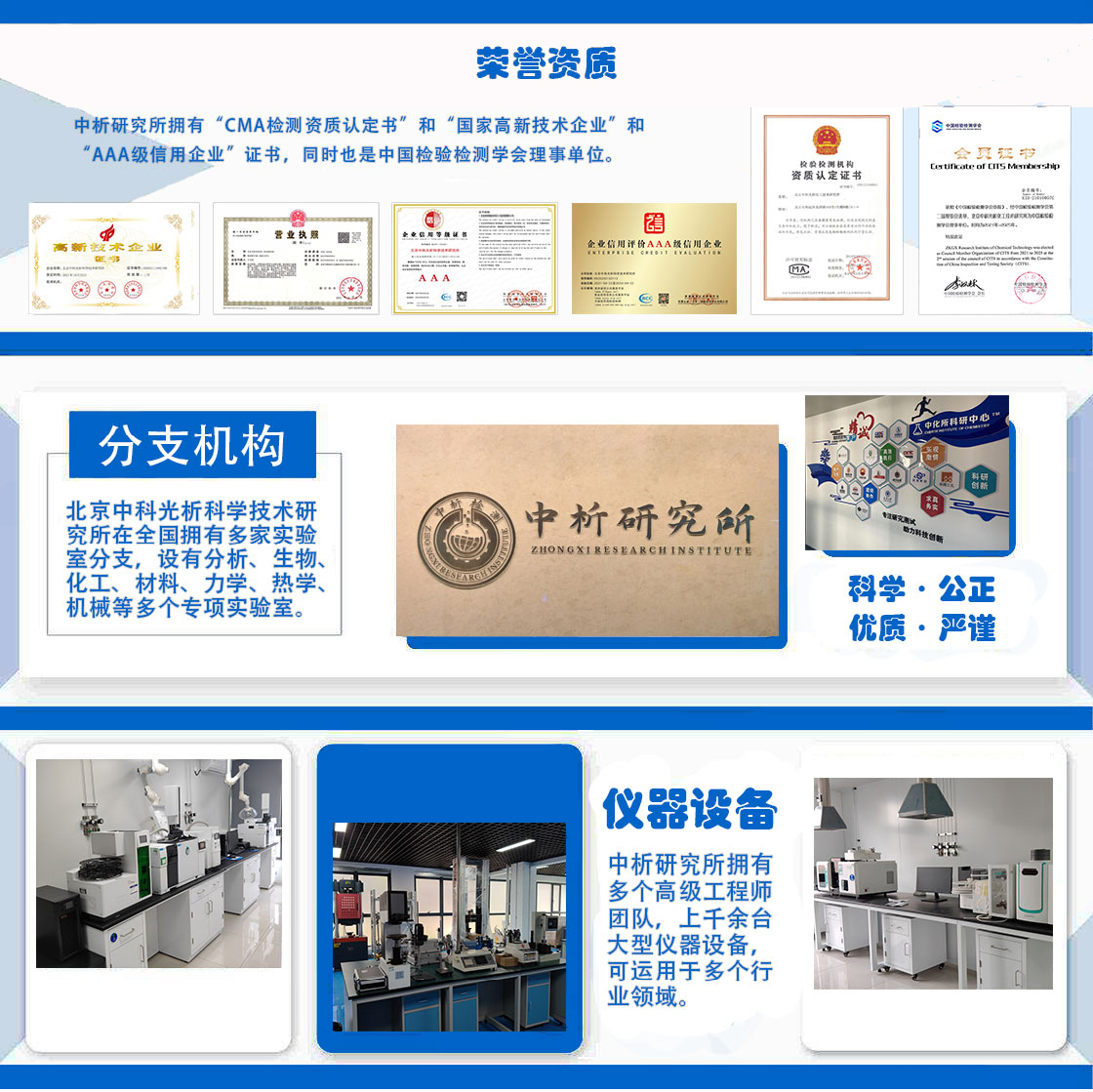
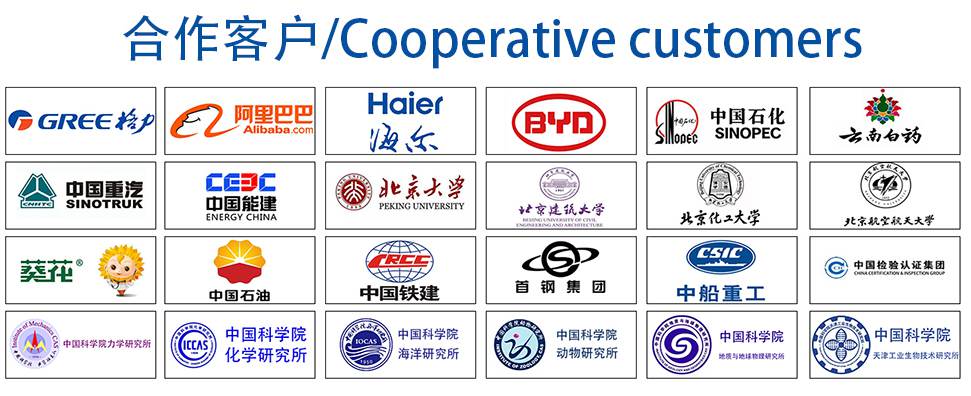