热喷涂金属及无机覆盖层中锌、铝及其合金的检测项目解析
热喷涂技术作为一种高效的材料表面强化与防护手段,广泛应用于航空航天、船舶制造、桥梁工程、石油化工等领域。通过将金属或无机材料加热至熔融或半熔融状态,并以高速喷涂至基体表面形成覆盖层,能够显著提升工件的耐腐蚀性、耐磨性和抗氧化性能。其中,锌(Zn)、铝(Al)及其合金涂层因其优异的防腐特性,成为热喷涂工艺中的主流选择。然而,涂层的性能与质量直接影响工件的使用寿命,因此必须通过科学、系统的检测项目确保其符合相关标准与技术要求。
核心检测项目及技术要求
针对热喷涂锌、铝及其合金覆盖层,需重点开展以下关键检测项目:
1. 涂层厚度检测
厚度是评价涂层防护性能的基础指标。过薄的涂层可能无法提供有效保护,而过厚则可能导致结合力下降或资源浪费。通常采用磁性测厚仪(适用于铁基基体)或涡流测厚仪(非铁基基体)进行测量,依据ISO 2064或GB/T 4956标准,要求厚度均匀且符合设计值,允许偏差一般不超过±20%。
2. 涂层成分分析
通过能谱分析(EDS)或X射线荧光光谱(XRF)测定涂层中锌、铝的纯度及合金元素(如镁、硅等)的含量。需确保其与设计配方一致,避免杂质超标导致耐蚀性下降。例如,Al-Mg合金中镁含量需控制在3%-5%以优化耐海水腐蚀性能。
3. 结合强度测试
采用拉伸试验法(ASTM C633)或划痕试验法(ISO 26443),评估涂层与基体的结合力。锌、铝涂层的结合强度通常需≥10MPa,特殊应用场景(如高温环境)需提高至≥20MPa。
4. 孔隙率检测
通过金相显微镜观察或渗色法(如铁氰化钾溶液渗透)测定涂层孔隙率。锌涂层的孔隙率应<5%,铝涂层因氧化膜自修复特性可放宽至<8%,但关键部件需控制在<3%以内。
5. 硬度与耐磨性测试
使用显微硬度计(HV0.1)测定涂层硬度,锌涂层硬度范围约为60-100HV,铝涂层为80-120HV。耐磨性可通过Taber磨损试验或喷砂试验评估,要求质量损失率低于0.5g/m²·h。
6. 耐腐蚀性能评价
依据ISO 9227进行中性盐雾试验(NSS),锌涂层在2000小时内需无红锈出现,铝涂层则需通过3000小时测试。此外,电化学阻抗谱(EIS)可量化涂层的极化电阻与腐蚀速率。
7. 表面形貌与微观结构分析
利用扫描电镜(SEM)观察涂层表面颗粒分布、层间结合及氧化情况,确保无裂纹、未熔颗粒等缺陷。铝涂层还需检测氧化铝(Al₂O₃)层的连续性与致密性。
检测方法与标准依据
检测需遵循国际/国内标准:ISO 14918(热喷涂质量要求)、ASTM B833(锌/铝线材标准)、GB/T 9793(热喷涂金属涂层通用规范)等。实验室检测与现场快速检测结合,确保数据的准确性和工程适用性。
检测意义与应用方向
通过对锌、铝涂层的全面检测,可有效预防涂层剥落、早期腐蚀等问题,延长设备寿命并降低维护成本。例如,在海洋平台中,合格的铝镁合金涂层可将防腐周期提升至15年以上。未来,随着智能化检测设备(如无人机搭载涂层测厚系统)的普及,检测效率与覆盖范围将进一步提升。
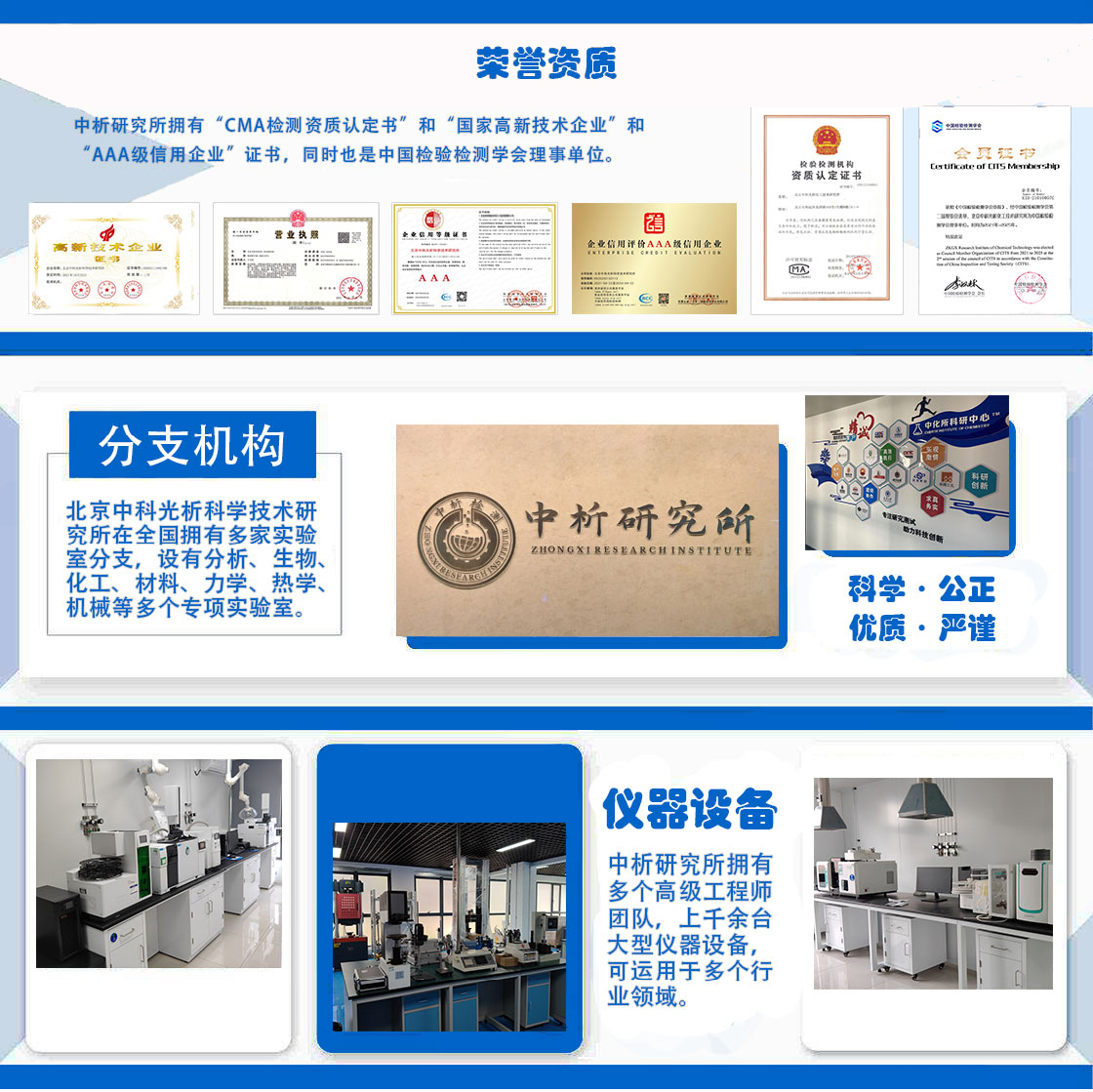
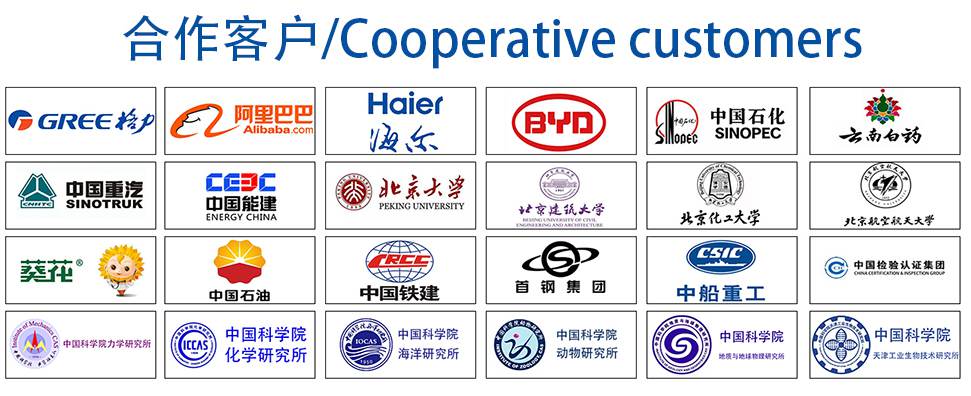