不锈钢焊接钢管检测的重要性
不锈钢焊接钢管因其优异的耐腐蚀性、高温稳定性和机械强度,广泛应用于石油化工、食品加工、医疗设备及建筑结构等领域。为确保其性能满足使用要求,避免因材料缺陷或工艺问题导致的失效风险,必须通过科学规范的检测流程对焊接钢管进行严格质量控制。检测过程涵盖原材料成分分析、焊接质量评估、力学性能测试及耐腐蚀性验证等多个维度,是保障产品安全性和可靠性的核心环节。
核心检测项目及方法
1. 化学成分分析
通过光谱分析仪对钢管母材及焊材的化学成分进行定量检测,重点验证铬(Cr)、镍(Ni)、钼(Mo)等关键元素的含量是否满足标准(如ASTM A312、GB/T 12771),确保材料具备预期抗腐蚀能力。碳(C)含量控制尤其重要,直接影响焊接热影响区的耐晶间腐蚀性能。
2. 力学性能测试
包括拉伸试验、弯曲试验和硬度测试:拉伸试验测定屈服强度、抗拉强度和延伸率;弯曲试验评估焊缝区域塑性变形能力;硬度测试(布氏/洛氏)检测热影响区硬化现象,防止脆性断裂风险。
3. 表面质量检测
采用目视检查与仪器测量相结合的方式,检查钢管内外表面是否存在裂纹、气孔、咬边等焊接缺陷,同时验证表面粗糙度、氧化色控制及酸洗钝化处理效果。工业内窥镜常用于小口径钢管内部探查。
4. 尺寸精度验证
使用卡尺、千分尺测量外径、壁厚公差,通过椭圆度检测仪评估截面圆度,并对钢管直线度进行全长检测。特殊应用场景还需检测焊缝余高,确保不超过标准允许值。
5. 耐腐蚀性能试验
根据使用环境选择盐雾试验(ASTM B117)、晶间腐蚀试验(GB/T 4334)或点蚀电位测试,模拟实际工况验证材料耐蚀性。对于双相不锈钢还需进行相比例分析,确保奥氏体-铁素体平衡。
6. 焊缝质量专项检测
采用渗透检测(PT)或磁粉检测(MT)排查表面微裂纹,X射线探伤(RT)或超声波探伤(UT)检测内部未熔合、夹渣等缺陷。金相显微镜分析焊缝组织形态,评估热输入对微观结构的影响。
7. 压力密封性测试
进行水压试验或气压试验,施加1.5倍设计压力并保压10-30分钟,检查管体是否泄漏或变形。高压工况用管需增加爆破压力测试,验证极限承压能力。
8. 第三方认证与标准符合性
针对出口产品或特殊行业应用,需取得API、CE、PED等认证,并依据ASME B36.19M、EN 10217-7等国际标准进行全项目复核,确保检测结果具有互认性。
结语
通过系统化的检测流程,可全面把控不锈钢焊接钢管的质量风险点。现代检测技术如数字射线成像(DR)和相控阵超声(PAUT)的应用,显著提升了缺陷识别精度与检测效率,为高端制造业的精密化需求提供技术支撑。
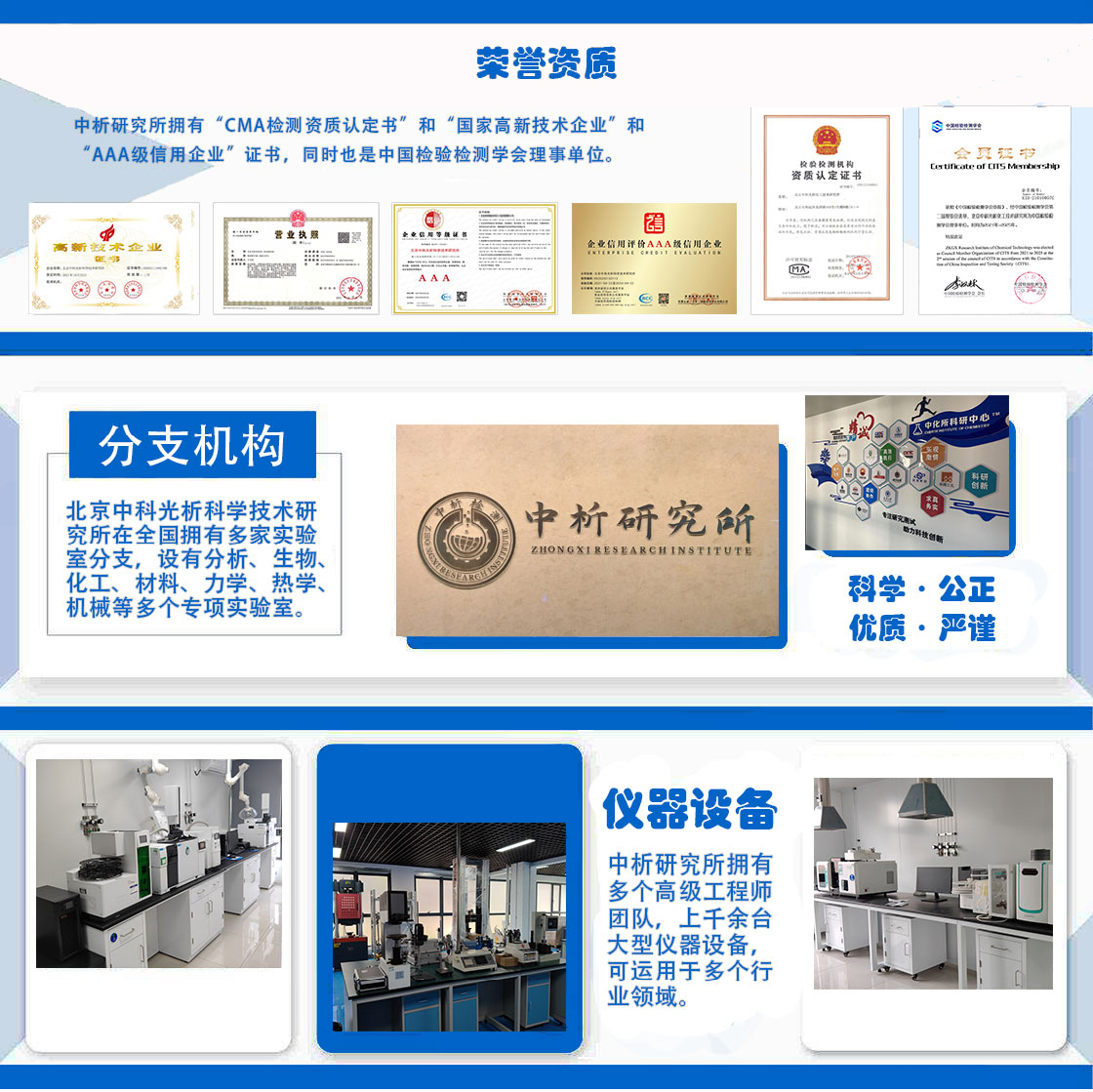
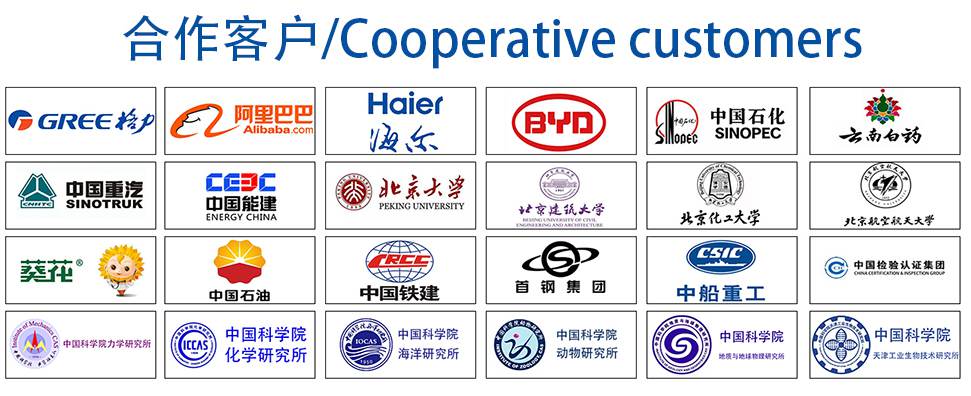